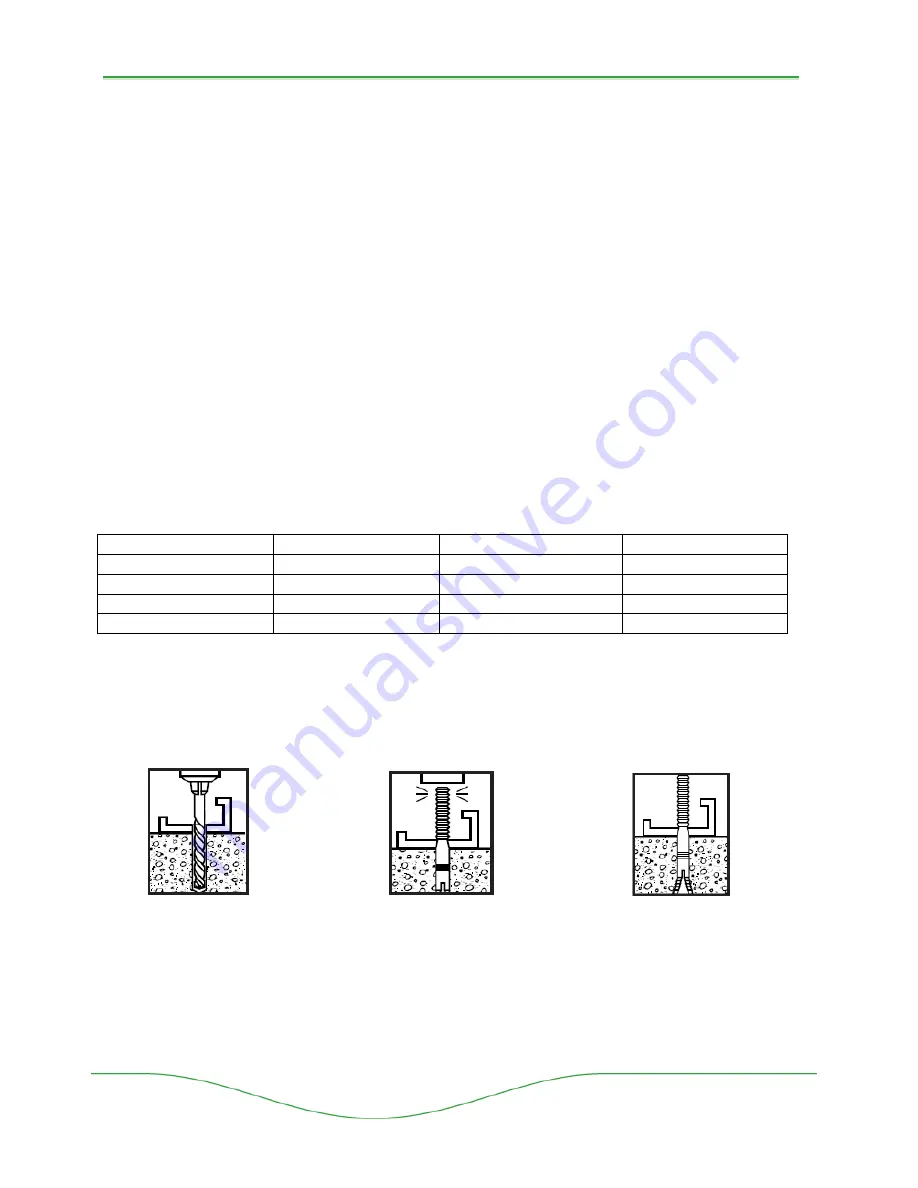
THT-100
20
Boon Edam Inc.
402 McKinney Parkway
Version: Rev A6 10/28//2011
Tel. 910-814-3800 fax 910-814-3899
Issue: THT-100-IMM-USA
5.2 Tool and Manpower List
Typical THT-100 installations require two men for standing and lifting materials into place. The
following tools are needed for installation.
•
Metric End wrench set
•
Basic Metric Socket Set
•
Metric Allen Wrench Set
•
Precision Flat Blade Screw Driver, 1.5-4mm
•
Hammer Drill with rotary hammer drill bits (3/8” for concrete anchoring)
•
4’ Level
•
6’ Ladder
•
Tape Measure
•
Electrical Fish Tape (for pulling ACS and power control wires)
•
Electrical Wire Stripping and Cutting Pliers.
•
4” to 6” Nylon Cable Ties
5.3 Bolt Torque Specifications
Use the following torque values for bolt connections, unless stated differently in the installation
manual or mechanical drawings.
Bolt Size
Thread Size
Torque Value ft lbs
Torque value nm
M5
0.8
4.13
5.6
M6
1.0
7.1
9.6
M10
1.5
34
46.09
3/8
16
40
54.23
5.4 Anchor Techniques
Boon Edam recommends using 3/8” minimum anchor bolts supplied with the hardware kit.
1. Drill hole
same
diameter as
anchor to
be
embedment
2. Drive Anchor
with expander
plug in bottom
through material
to be fastened
3. Expand
anchor by
driving
anchor over
plug with
hammer.