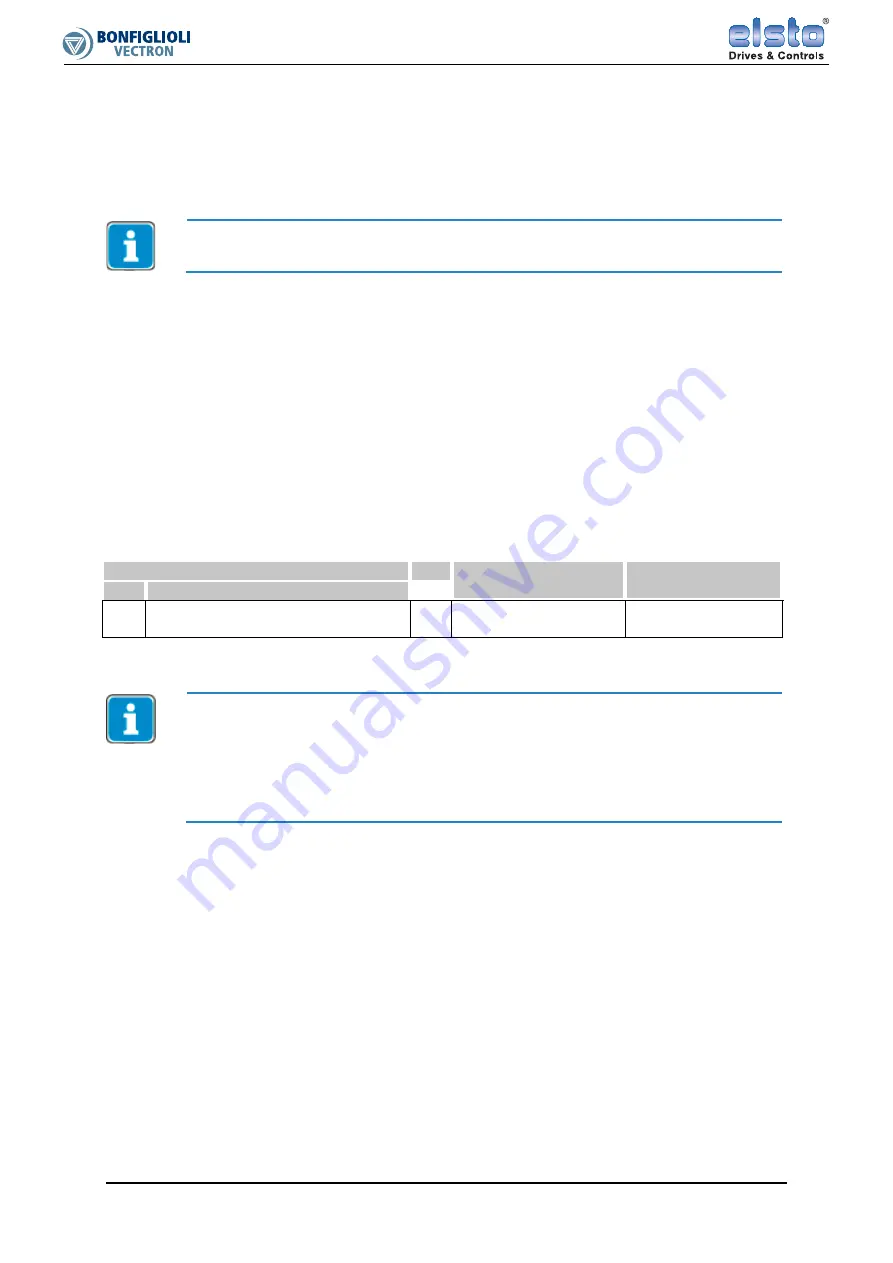
Voorhout • Groningen • Weert • Hoogerheide
T
+31(0)88 7865800
I
elsto.eu
Rated torque M
rated
of the machine in [Nm] is calculated from the motor data:
60 ·
P.376
· 1000
M
rated
=
——————————
2 ·
π
·
P.372
with
P.376
= rated power in [kW]
P.372
= rated speed in [rpm]
5.5
Compensation calculator (Torque Compensation)
The compensation calculator provides the torque required for compensation of losses in the system
and acceleration of the drive. The torque output by the compensation calculator is added to the value
to be output by the speed controller. Thus, it is not subject to the limitations that can be made in the
speed controller.
CAUTION
If the parameters are configured incorrectly, the drive might race. Before commission-
ing, Parameter
Frequency Switch-off Limit
417
should be set to the maximum permis-
sible frequency.
It is important that the parameters be configured in the right order (as described be-
low).
5.5.1
Compensation of system losses
Via Parameters
865
and
866
described in the following, a static and a dynamic (speed-dependent)
value for compensation of system losses is configured. System losses are the components of the
torque to be applied which don't contribute neither to acceleration of the drive nor to building up the
web tension.
5.5.1.1
Compensation of static frictional losses
Static friction mainly occurs in the bearings of the winder shaft, gear box and motor. To compensate
these frictional losses, the torque must produce an additional constant torque. This torque is set via
Parameter
Static Friction Compensation
865
in % of the rated torque of the drive.
During commissioning, the value is determined as follows:
•
Limit the torque which can be output by the speed controller to 0 by the following parameter set-
tings, see Chapter 5.4 “Limitation of web tension (Tension Setpoint)”:
−
Parameter
860
= 6 – On
−
Parameter
861
= 0%
•
Start drive at a preset speed (with empty winder).
•
Increase the value of Parameter
865
carefully until the drive starts turning slowly.
•
Reduce the value of Parameter
865
again slowly until the drive no longer turns.
Parameter
Unit
Setting range
Default settings
No.
Identifier
865
Static Friction Compensation
%
0.00 .. 30.00
0.00
11/13
ACU
Winding Drive
35
5.5.1.2
Compensation of dynamic frictional losses
Dynamic frictional losses are speed-dependent. They are produced, for example, by the viscosity of
the gear oil and - if a motor fan is installed - by fan losses.
Compensation is done via Parameter
Dynamic Friction Compensation
866
.
This Parameter may only be set after Parameter
865
.
The value should be determined at rated speed if possible as follows:
•
Start drive (speed-controlled).
•
Once the reference speed is reached, monitor the output of the speed controller using the Scope
function (
Q.24
).
•
Adjust the value of Parameter
866
until the speed controller outputs approx. 0.
•
Then, deactivate the speed controller again, i.e. limitation of torque to 0 by the following settings:
−
Parameter
860
= 6 – On
−
Parameter
861
= 0%
•
To verify the setup, accelerate to different reference speed values. The actual speed should adjust
to approximately the reference value in each case.
Parameter
Unit
Setting range
Default settings
No.
Identifier
866
Dynamic Friction Compensation
%/
Hz
0.00 .. 30.00
0.00
In the case of indirect tension control, the reference speed is set too high via the gear
stage so that the speed controller works at its limit. As a result, the compensation cal-
culator will also receive a reference frequency which is too high.
Parameter
Dynamic Friction Compensation
866
must be reduced, after completion of
parameterization of all compensations, by the percentage used for overdriving the
speed controller (normally 5-10%).
36
ACU
Winding Drive
11/13