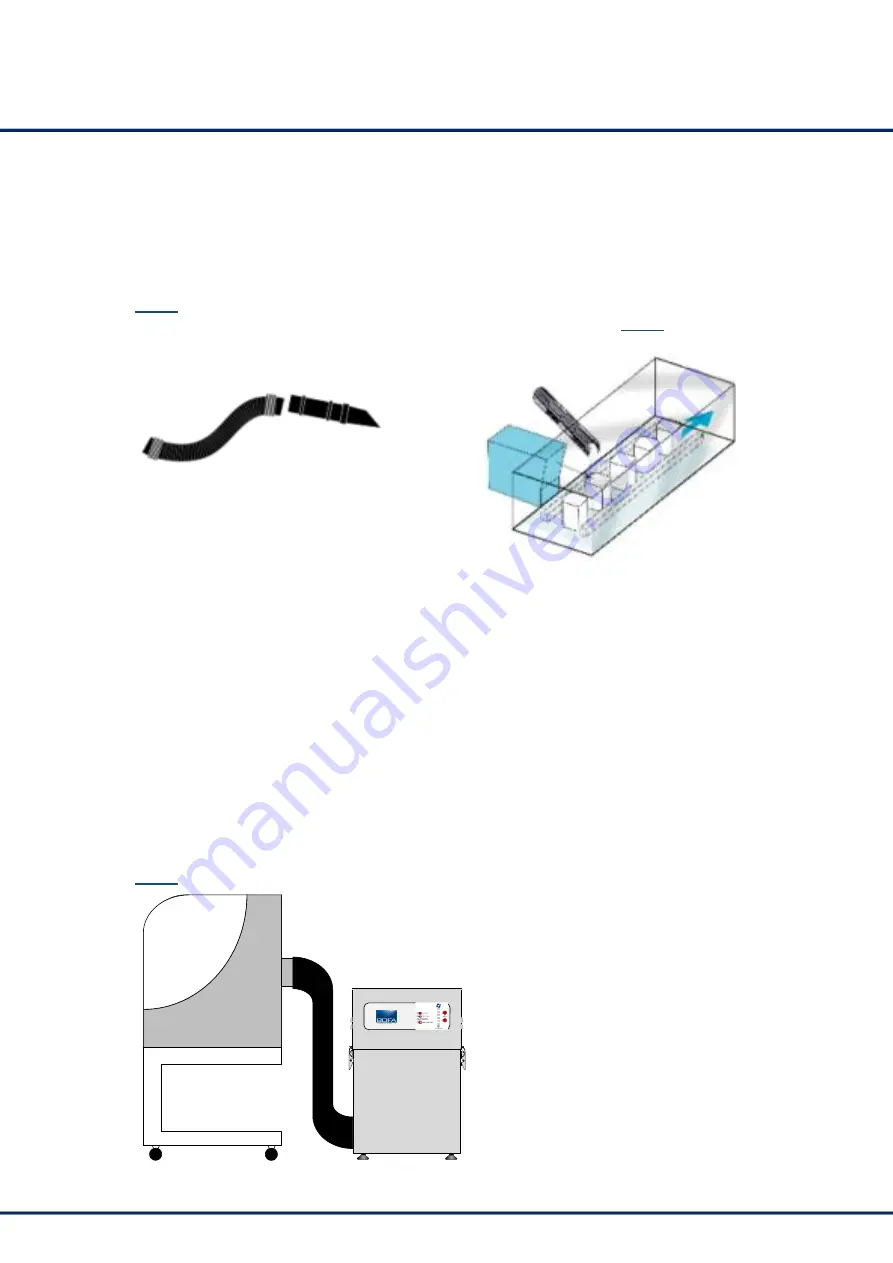
6
Version 10.08.2011
Purge air should be kept to a minimum, where possible, to prevent the fume being
blown away from the nozzle
High speed bottling lines may need bigger scoops or nozzles both sides of the bottles
because of the turbulence caused by the speed of the bottles
Fig. 2
Fig. 3
Enclosures
Extraction can be attached to an enclosure around the marking zone provided
the extraction point is situated within 50 -75mm of the marking point.
(See fig. 3)
Cabinets
(See fig. 4) Cabinets normally have a 75 or 100mm spigot for fume extraction.
For best performance use the same diameter hose as the spigot and reduce
at extractor if necessary. Keep the hose run as short as possible.
Extraction units should be sited in a well ventilated room.
Fig. 4
LASER UNIT