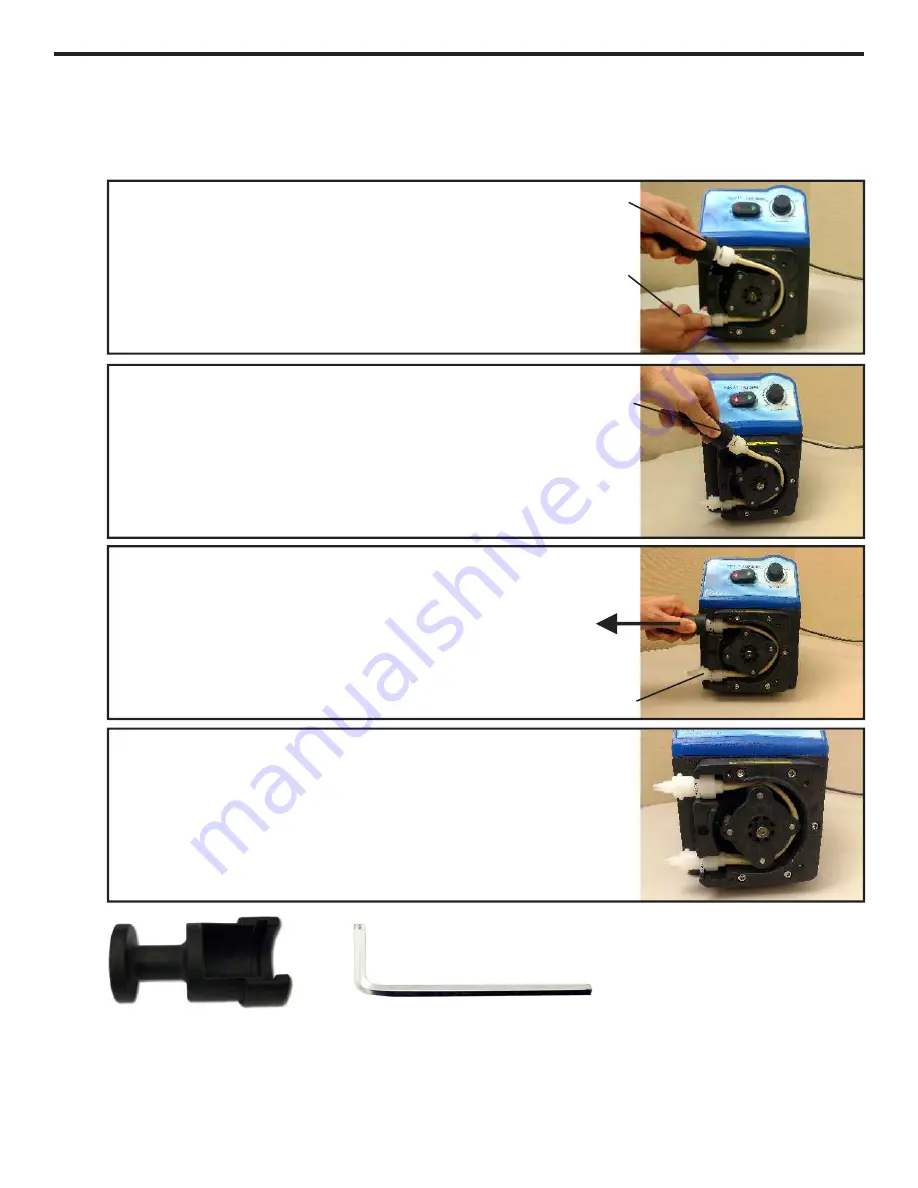
Page 12
9.2
Tube Installation
Step 1
Step 2
NOTE
: Your hand should only come in contact with the
installation tool.
Place the switch in the Manual (MAN) position.
Use the installation tool to leverage the tubing into the pump
head while the rotor is rotating.
Step 3
PULL
Step 4
Suction side
tube adapter
Installation Tool
Installation Tool
Discharge side
tube adapter
Tube Installation Tool
90002-278
NOTE
: Thoroughly clean the pump head and rotor. Rotor can be removed by pulling straight out. After the
cleaning process, push the rotor back on the shaft. Refer to the drawing below for proper assembly.
NOTE
: For the rotor direction, the word, “FRONT,” on the rotor must face forward (front of the pump).
®
FlexFlo
Ensure the pump is stopped.
With the pump stopped, press the suction side of tube
adapter securely into the pump head.
Clip tube installation tool to discharge side of tube adapter.
NOTE
: Always keep fingers away from the rollers and rotor.
Continue to hold onto the installation tool
Allow rotor to rotate a few times. This will stretch tubing out.
After a few rotations, pull the installation tool and tubing in
the direction of rotation.
Press the discharge side of tube adapter securely into the
pump head.
Place the switch in the OFF position.
The suction and discharge tube adapter ends should be
securely held in place on the pump head as illustrated in
photo.
Secure the pump head cover to the pump head using the
four black thumb screws (maximum torque 6-8 in. lbs.).
Page 13
10.0 Pump Maintenance
Always wear protective clothing, face shield, safety glasses and gloves when working on or
near your metering pump. Additional precautions should be taken depending on solution
being pumped. Refer to MSDS precautions from your solution supplier.
Routine Inspection and Maintenance
The pump requires minimal maintenance. However, the pump and all the accessories should be checked weekly,
especially when pumping chemicals. Inspect all the components for signs of leaking, swelling, cracking, discolor-
ation, or corrosion. Immediately replace worn out or damaged components.
Cracking, crazing, or discoloration during the first week of operation are signs of a severe chemical attack. If this
occurs, perform the following steps:
1. Immediately remove the chemical from the pump.
2. Determine which parts are being attacked.
3. Replace the damaged parts with parts that have been manufactured using more suitable materials.
4. After servicing, operate the pump to verify normal operation.
NOTE
: The manufacturer does not assume responsibility for damage to a pump that has been caused by a
chemical attack.
How to Clean and Lubricate the Pump
>
The pump will require occasional cleaning, and it will depend on the severity of service.
>
When changing the pump tube assembly, the pump head chamber, the roller assembly, and the pump head
cover should be wiped of any dirt and debris.
>
Clean the motor shaft with a clean towel, and then apply a small amount of grease to the shaft. This will help
prevent the rotor from sticking to the motor shaft.
>
Periodically, or when necessary, grease the pump head cover bearing. Apply a small amount of grease
(Aeroshell aviation grease #5 or equivalent).
>
100% silicone lubrication may be used on the roller assembly.
>
Periodically clean the injection fitting /check valve assembly, especially since injecting fluids, like sodium
hypochlorite, can calcify. These lime deposits and other buildups can clog the fitting, increase back pressure,
and interfere with the check valve operation.
>
Periodically clean the suction strainer.
!
CAUTION
Allen Wrench
90008-162
®
FlexFlo