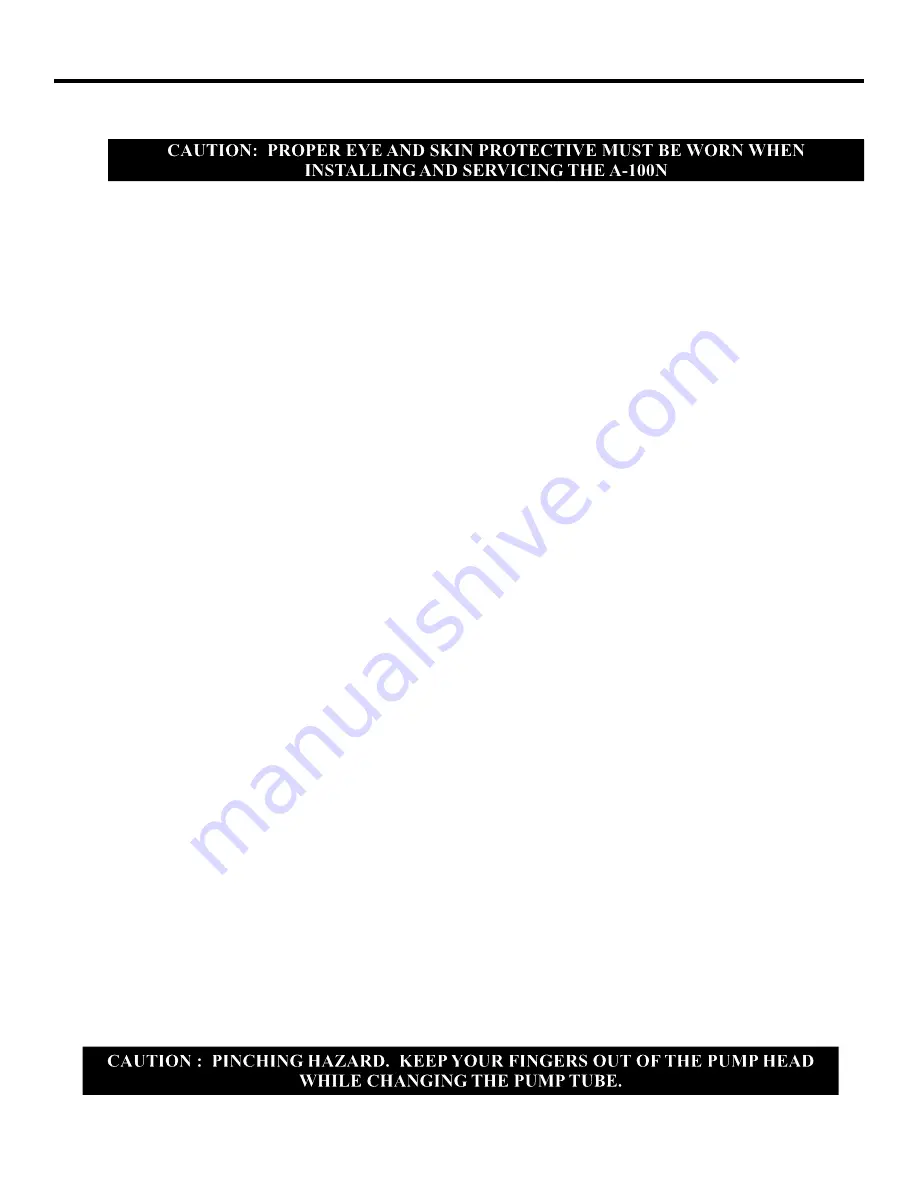
A-100N
7.4.1
How to Remove the Old Pump Tube
The pump roller assembly spins in a counter clockwise direction. The pump head inlet (suction) side is
located at the bottom of the pump and the outlet (discharge) is located at the top of the pump head.
7.4.1.1
Release any pressure that may be in the
discharge tubing.
7.4.1.2
Disconnect the suction and discharge tubes
from the pump tube.
7.4.1.3
Remove the pump head cover.
7.4.1.4
With the pump running, pull the inlet fitting
out of the pumphead. Guide the tube counter
clockwise away from the rollers. Pull the
outlet fitting out of the pump head.
7.4.2
How to Install a New Pump Tube
Be sure the pump head chamber is clean and free of any debris. Remove and inspect the roller assem-
bly. Be sure the rollers spin freely. If required, apply a small amount of grease to the pump head cover
bearing. Silicone oil
only
may be used on the tubing and rollers. See section 7.2.
6.4.2.1
With the pump running, insert the inlet (suction) side of the Pump Tube fitting into the lower retaining
slot in the pump head. Fig. 7.2.
6.4.2.2 Carefully
guide the Pump Tube into the pump head. Stretch the tube slightly and insert the outlet
(discharge) fitting into the upper retaining slot in the pump head. Fig. 7.3.
6.4.2.3
Place the clear cover on the pump head and secure with three screws.
FIG. 7.2
FIG. 7.3
Page 17
7.4
How to Replace the Pump Tube
The pump tube assembly will eventually break if not replaced. The tube has been designed for a
minimum service life of 500 hours. However, the life of the tube is affected by many factors such as the
type of chemical being pumped, the amount of back pressure, the motor RPM, temperature and others.
The pump tube assembly must be inspected and replaced regularly.
After replacing the pump tube, press the RUN/STANDBY button and the DIGIT button at the
same time to reset the service warning timer.
A-100N
7.0
How to Maintain the A-100NV
7.1
Routine Inspection and Maintenance
The A-100NV requires very little maintenance. However, the pump and all accessories should be
checked weekly. This is especially important when pumping chemicals. Inspect all components for
signs of leaking, swelling, cracking, discoloration or corrosion. Replace worn or damaged components
immediately.
Cracking, crazing, discoloration and the like during the first week of operation are signs of severe
chemical attack. If this occurs, immediately remove the chemical from the pump. Determine which
parts are being attacked and replace them with parts that have been manufactured using more suitable
materials. The manufacturer does not assume responsibility for damage to the pump that has been
caused by chemical attack.
7.2
How to Clean and Lubricate the A-100NV
The A-100NV will require occasional cleaning and lubricating. The amount will depend on the severity
of service.
]
When changing the pump tube assembly, clean the pump head chamber, TFD sensors, roller assembly
and pump head cover.
]
The pump head cover bearing may require grease periodically. Apply a small amount of grease
(Aeroshell aviation grease #5 or equivalent) when necessary.
]
Silicone oil
ONLY
may be used on the roller assembly and tube assembly.
]
The injection/check valve assembly
must be cleaned
periodically, especially when injecting fluids that
calcify such as sodium hypochlorite. These lime deposits and other build ups can clog the fitting
increasing the back pressure which can interfere with the check valve operation and possibly damage the
fitting and/or the pump. See section 4.3.4. Fig. 4.7.
]
Periodically clean the suction strainer. Fig.4.5.
]
Periodically inspect the air vents located under the motor compartment and on the rear panel. Clean if
necessary.
7.3
500 Hour Service Warning Timer
The A-100NV is equipped with a service warning timer. After 500 hours of accumulated running time,
the
SERVICE
icon will light. This is a reminder that the pump tube is nearing its minimum life expec-
tancy and should be replaced.
Your actual tube life will depend on many factors such as the chemical
used, back pressure, temperature, viscosity, and motor RPM.
Simultaneously press the
RUN/STANDBY
and
DIGIT
buttons to reset the service timer to zero.
Note:
Pressing the
FIELD
and
DIGIT
buttons will display the currently accumulated time value.
Page 16
Inlet Adapter
Outlet Adapter
Pump Head
FIG. 7.1
RUN
STANDBY
RUN
FIELD
DIGIT
MODE
PROGRAM
STAND-BY
PRIME
MINIMUM
MAXIMUM
INPUT MODES
1 - MANUAL
2 - 4-20mA
3 - 0-10VDC
4 - PULSE (Hz)
PROGRAM
RESET SERVICE
PRIME
DISPLAY
VARIABLE SPEED PUMP
% SPEED
1
MODE
VDC
SERVICE
1000
ALARM
mA
Hz