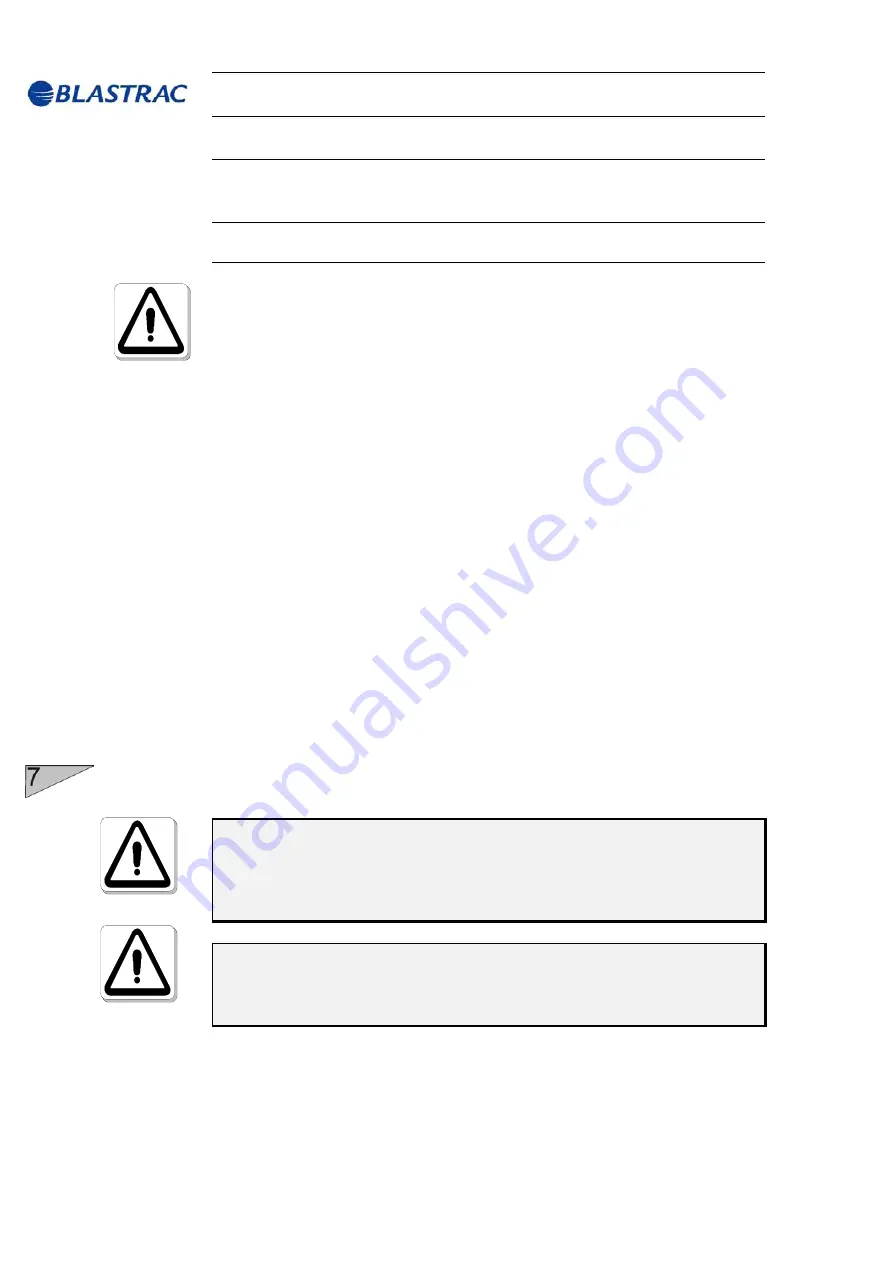
Service Manual
Side shift & adapter 2-45D
Maintenance
2
7.1 Recommendations
With maintenance and inspection works, please observe Chapter 2
"
Safety instructions
".
Failures due to inadequate or incorrect maintenance may generate
very
high repair costs
and long standstill periods.
Regular
maintenance is therefore imperative.
Operational safety and service life of the side shift and machine
adapter depend, among other things, on proper maintenance.
The following table shows recommendations about time, inspection
and maintenance for the normal use of the side shift and machine
adapter.
The time indications are based on uninterrupted operation. When the
indicated number of working hours is not achieved during the
corresponding period, the period can be extended. However a full
overhaul must be carried out at least once a year.
Due to different working conditions it cannot be foreseen how
frequently inspections for wear checking’s, inspection, maintenance
and repair works ought to be carried out. Prepare a suitable
inspection schedule considering your own working conditions.
Our specialists will be happy to assist you with more advice.
Prior to any repair works on the side shift and machine
adapter, secure the equipment against unintentional
switching-on. Put the side shift and machine adapter to its
safety off position
.
The supplier’s operating and maintenance instructions
should also be followed during service and maintenance.
IMPORTANT: First read the Service Manual!
Содержание 2-45D
Страница 1: ...Operating Instructions 2 45D MAN 2 45D EN Freightliner...
Страница 3: ......
Страница 43: ...Operating Instructions 2 45D Operation 4...
Страница 75: ...Service Manual Side shift adapter 2 45D MAN SA2 45D EN...
Страница 109: ...Side shift adapter 2 45D Service Manual Hydraulic system Contents Chapter 8 8 1 Hydraulic diagram...
Страница 121: ...Operating Instructions 2 45TDC MAN 2 45TDC EN Freightliner...
Страница 169: ...2 45TDC Operating Instructions Electrical hydraulic systems Contents Chapter 8 8 1 Circuit diagram 8 2 Hydraulic diagram...