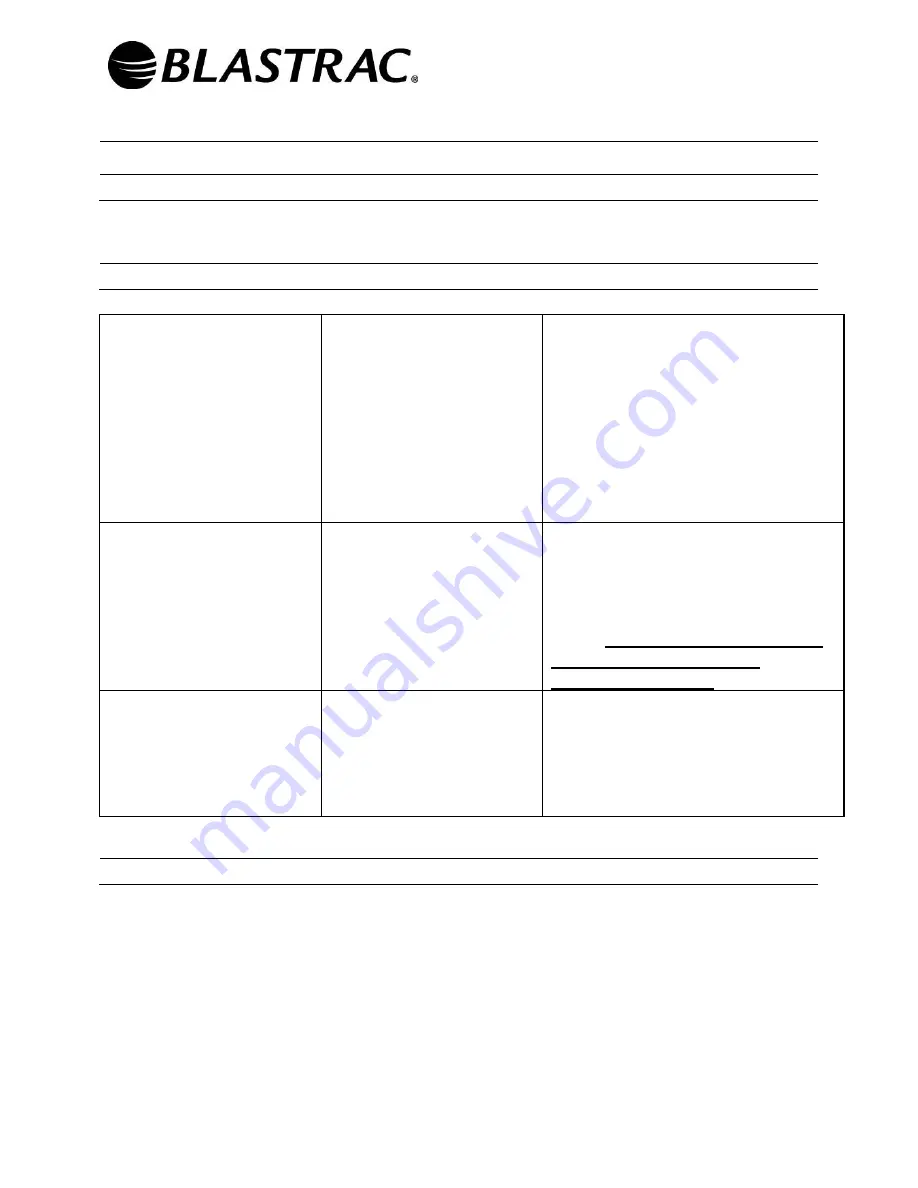
Operating Instructions 1-8DEC 230V
Troubleshooting
10.1 Continued
Abrasive leakage.
Improper sealing.
Feed spout
Improper control cage
setting.
Abrasive valve setting
Check all seals for wear.
Check feed spout alignment and
rubber seal.
Abrasive rebounding from side of
machine. Check blast pattern.
Be sure abrasive valve closes
when handle is released. Readjust
if necessary.
Machine hang-up.
Uneven work surface/
floor obstruction.
Pull up on steering handle to raise
machine to clear small obstructions
or uneven work surfaces. Shut
abrasive valve if obstruction cannot
be cleared. Pull back machine to
clear.
Use caution when raising
seal due to high velocity
abrasive exposure.
Loss of cleaning action.
Machine travel speed too
fast.
Abrasive contaminated.
Slow travel speed.
Clean storage hopper and replace
abrasive. Check ventilation
system.
10.2 Troubleshooting
– Ventilation System (Dust Collector)
Note: Once the Dust Collector has been in operation for several minutes, a stable
operating level will result. Sudden changes in operation can usually be traced to a
malfunction.
43
Содержание 1-8DECMKI
Страница 8: ...Operating Instructions 1 8DEC 230V Operator Responsibilities Section 2 2 1 Operator Responsibilities 7...
Страница 18: ...17...
Страница 19: ...18...
Страница 20: ...19...
Страница 29: ...Operating Instructions 1 8DEC 230V Edging Mode Section 6 6 1 Edging Mode 28...
Страница 31: ...30...
Страница 32: ...Operating Instructions 1 8DEC 230V Equipment Calibration Section 7 7 1 Equipment Calibration 31...
Страница 35: ...Operating Instructions 1 8DEC 230V Wear Parts Section 8 8 1 Wear Parts 8 2 Maintenance Log 34...
Страница 38: ...Operating Instructions 1 8DEC 230V Blast Wheel Replacement Section 9 9 1 Blast Wheel Replacement 37...
Страница 50: ...Operating Instructions 1 8DEC 230V Specifications Section 12 12 1 Specifications 49...