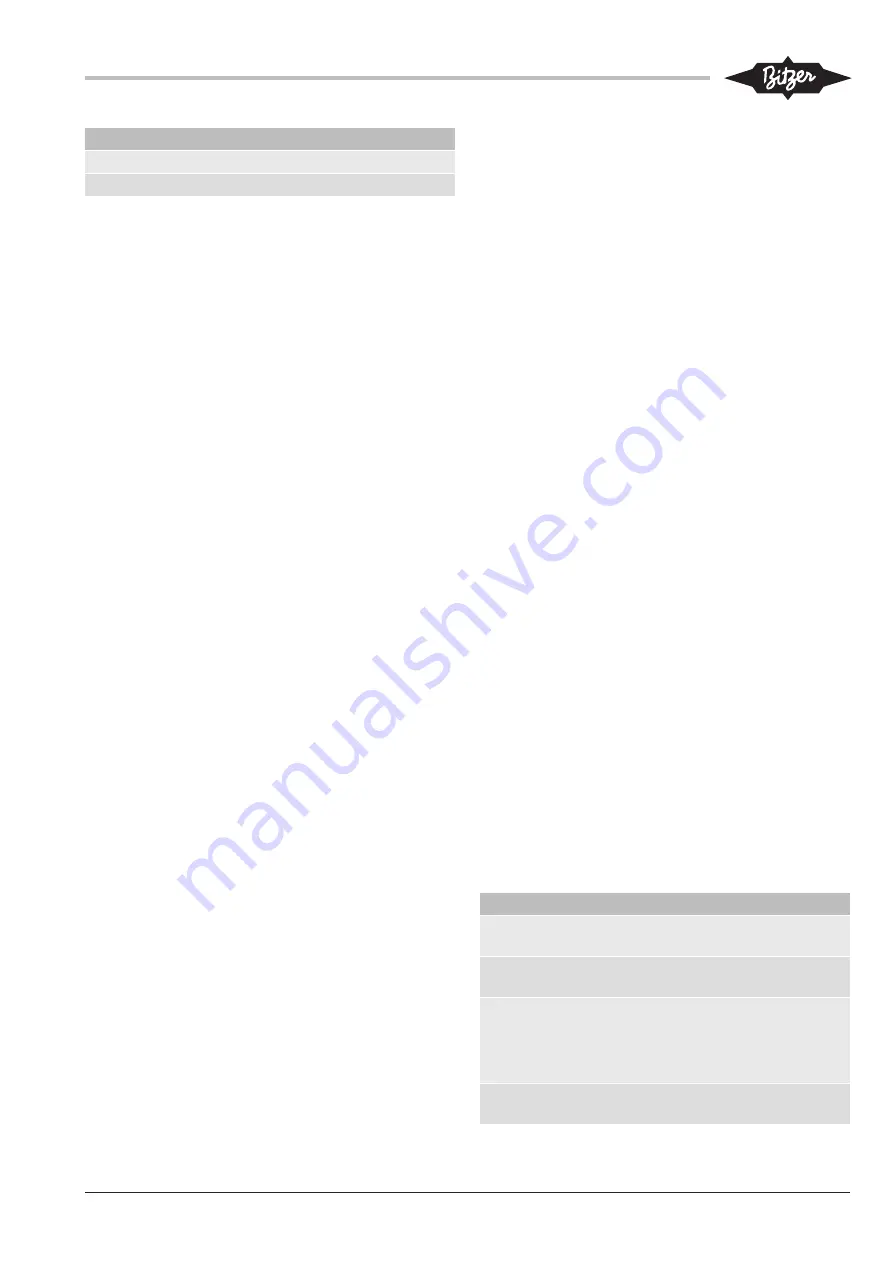
KT-230-1
7
Connection positions
D
LED sight glass
D
Terminal box
Dimensional drawings for 4JE-13Y .. 8FE-70(Y) upon
request.
Upon market launch, a high pressure switch with a cut-
out pressure of 32 bar is mounted at position 2 and
electrically connected to the CM-RC-01. For the com-
pressors 4VES-6Y to 4NES-20(Y), a high pressure lim-
iter is used. For all other compressors, a high pressure
cut-out is used.
4
Control and monitoring functions
4.1
Control functions
This chapter describes all control functions including
the options.
Capacity control CRII
The CM-RC-01 provides virtually stepless adjustment
of the compressor capacity depending on the setpoint
of the superior system controller. This is done by
switching the CRII solenoid valves. 4-cylinder com-
pressors with 2 and 6-cylinder compressors with 3 in-
stalled capacity regulators are regulated between full
load and 10% part load, 8-cylinder compressors
between full load and 50%.
If a start unloading is mounted, there is one cylinder
bank less available for the capacity control. The range
of control for the capacity control is reduced accord-
ingly.
Start unloading SU
The start unloading can be installed for 4 and 6-cylinder
compressors. The module controls the solenoid valve
and ensures an unloaded compressor start.
Compressor cooling
The compressor control module activates the additional
fan when the discharge gas temperature of 120°C is
exceeded and deactivates it as soon as a temperature
of 100°C is reached. If the discharge gas temperature
reaches 135°C, the CIC is activated intermittently, from
a temperature of 140°C, it works permanently. While
the CIC is active, the compressor can only be operated
in the upper part-load range. The limit is 50% for 4-cyl-
inder compressors and 66% for 6-cylinder com-
pressors.
The module activates the additional fan in the lower
part-load range to cool down the motor, if necessary.
This is done for 4-cylinder compressors in a part-load
range below 50% and for 6-cylinder compressors below
33%.
Oil heater
When the compressor is at standstill, the module
switches the oil heater on and if the compressor is in
operation, the oil heater is switched off.
Control of the motor contactors at compressor start
The compressor control module controls the activation
and deactivation times of the motor contactors. In the
state of delivery, the time relay control is configured for
the installed motor:
Part winding motor: The contact at CN2:2 (K1 Control)
closes 1 second after the release signal. The contact at
CN2:1 (K2 Control) closes 0.5 seconds afterwards.
Both contacts remain closed until the compressor is
shut off.
Star-delta motor: The contact at terminal CN2:2 (K1
Control) closes 1 second after the release signal and
reopens after further 1.5 seconds. The contact at ter-
minal CN2:1 (K2 Control) closes 1.5 seconds after the
release signal and remains closed until the compressor
is shut off.
Motor for direct-on-line start: The contact at terminal
CN2:2 (K1 Control) closes 1 second after the release
signal and reopens when the compressor is shut off.
The contact at terminal CN2:1 (K2 Control) is not used.
For a soft start and operation with frequency inverter,
only one motor contactor is required.
4.2
Monitoring and protective functions
The compressor control module monitors the signals
from several sensors that may be located on the com-
pressor or on the suction gas and discharge gas line:
Monitored function
Measuring sensor
Motor temperature
(standard)
Motor temperature sensor
(R1 .. R6)
Discharge gas temper-
ature (standard)
Discharge gas temperature
sensor (R7)
Application limits (op-
tion):
Condensing and evap-
oration temperature
Low pressure and high
pressure transmitters (B7
and B6)
Low pressure (option)
Low pressure transmitter
(B7)