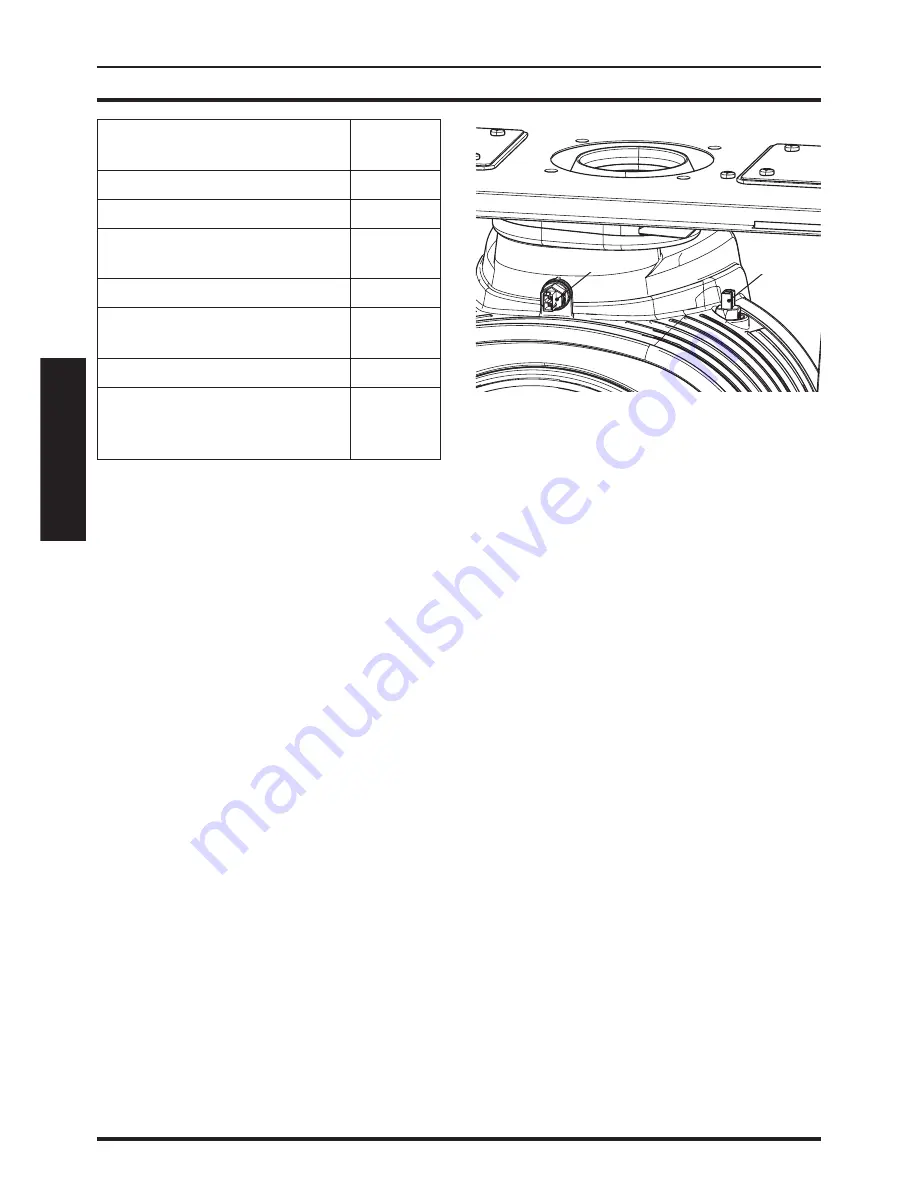
- 18 -
USE
USEFUL ADVICE
Faulty primary circuit
(no water or absence of flow)
04E
Faulty fan control system
05E
Faulty c.h. temp. probe NTC
06E
Faulty external temp. probe
NTC
08E
Faulty flue temp. probe NTC
09E
Flue probe intervention lock
-
out
10E
Flame detection error
11E
No circulation, of faulty pump
or intervention primary tem
-
perature limit.
14E
3.9 Flue probe
The flue probe 15 and safety thermal fuse
20 indicated in Fig. 3.7 are a safety device.
The flue probe 15 intervenes when the flue
temperature exceeds 110°C placing the
boiler in safety block switching it off.
To reset normal boiler functioning, just press
the
11 (Fig. 3.5) key.
If flue probe 15
does not intervene and,
therefore does not send the boiler into se
-
curity lockout, thermofusible 20
enters into
function as a further safety measure.
This component sends the boiler into se
-
curity lockout when the flue temperature
reaches 167°C.
To restore the normal operation of the boil
-
er, contact the Authorized Service Centre.
Fig. 3.7
15
20