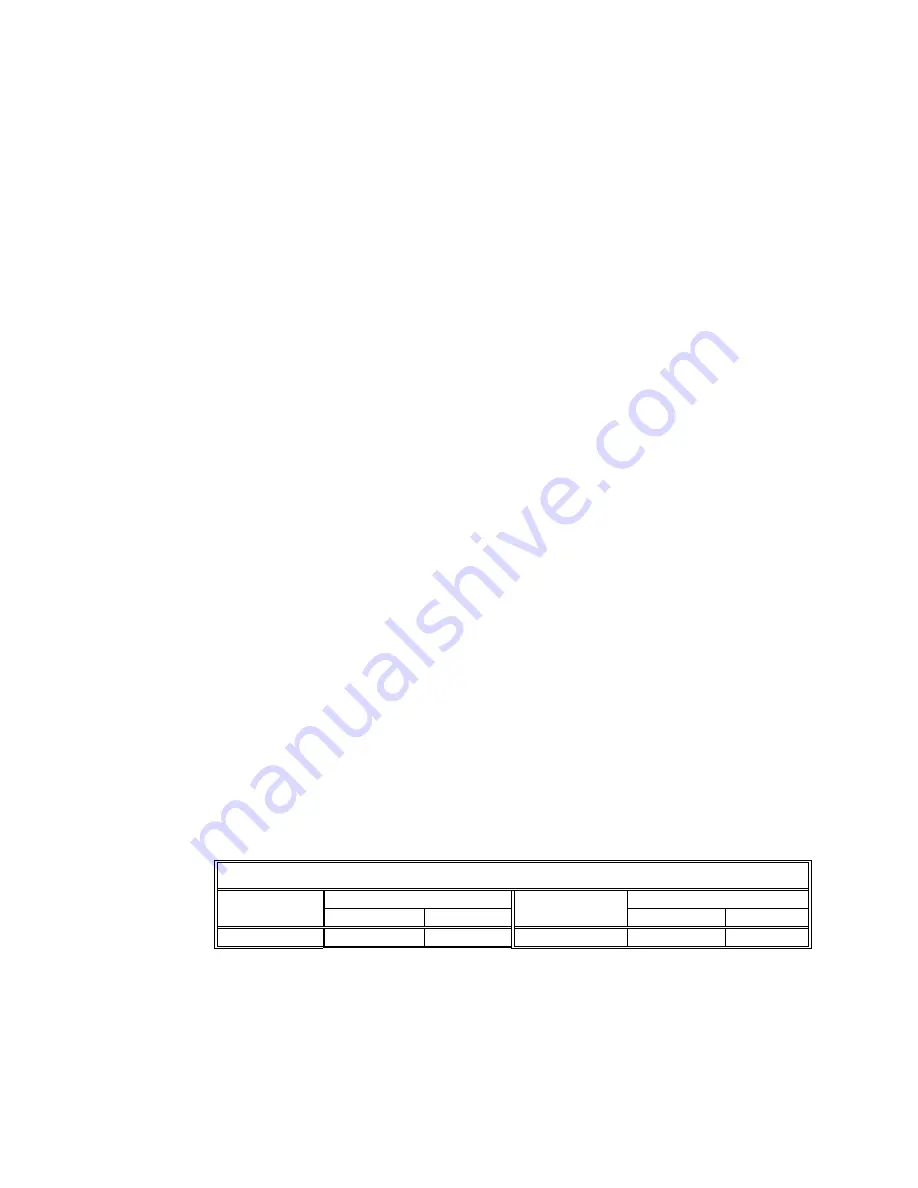
Bettis P/N 127073E
Revision “A”
Page 19 of 37
3.4.8
Refer to assembly drawing page 2 of 2 Detail "D". Install o-ring seal (4-70) into the seal
groove in the outboard end of piston rod (3-40).
3.4.9
Install two split ring halves (3-50) into the outer most groove in piston rod (3-40) and
retain by installing the recessed area of piston (3-30) over the two split halves (3-50).
3.4.10 Install two split ring halves (3-50) into the piston rod, in back of the piston and retain with
retainer ring (3-60).
3.4.11 Coat two tie bars (3-20) with lubricant and install by carefully pushing tie bars through
piston (3-30) and rod T-seal (4-50).
3.4.12 Install two tie bar o-ring seals (4-80) onto the inboard end of tie bars (3-20) and into the
o-ring grooves provided.
3.4.13 Insert the tie bars through inner end cap (3-10) and screw hex nuts (3-90) onto inboard end
of the tie bars. NOTE: Screw the tie bars through the hex nuts (3-90) until one complete
thread is exposed.
3.4.14 Refer to assembly drawing page 2 of 2 Detail "E". Install two tie bar o-ring seals (4-80) onto
the outboard end of tie bars (3-20) and into the o-ring grooves provided.
3.4.15 Apply lubricant to one o-ring seal (4-40) and install into the outer diameter o-ring groove of
outer end cap (3-80).
3.4.16 Apply lubricant to the bore of cylinder (3-70).
3.4.17 Install lubricated cylinder (3-70) over piston (3-30) and onto inner end cap (3-10). When
installing the cylinder over the piston seal tilt cylinder 15
°
to 30
°
degrees to piston rod.
CAUTION:
If needed, when installing the cylinder, hammer on the end of the cylinder
only with a non metallic object.
3.4.18 Install outer end cap (3-80) over tie bars (3-20) and into cylinder (3-70). NOTE: The
pressure inlet port should be positioned in the same position as recorded in section 2.2
step 2.2.1.
3.4.19 Install tie bar nuts (3-90) onto tie bars (3-20). Torque tighten tie bar nuts, alternately in 100
foot pound increments, until a final lubricated torque, as listed in the following table, has
been achieved.
TIE BAR NUTS
TORQUE (±5 %)
TORQUE (±5 %)
HOUSING
MODEL
FT-lb
N-m
HOUSING
MODEL
FT-lb
N-m
G2
120
163
G3
150
203
3.4.20 Install lockwashers (3-140) onto socket cap screws (3-130) ).