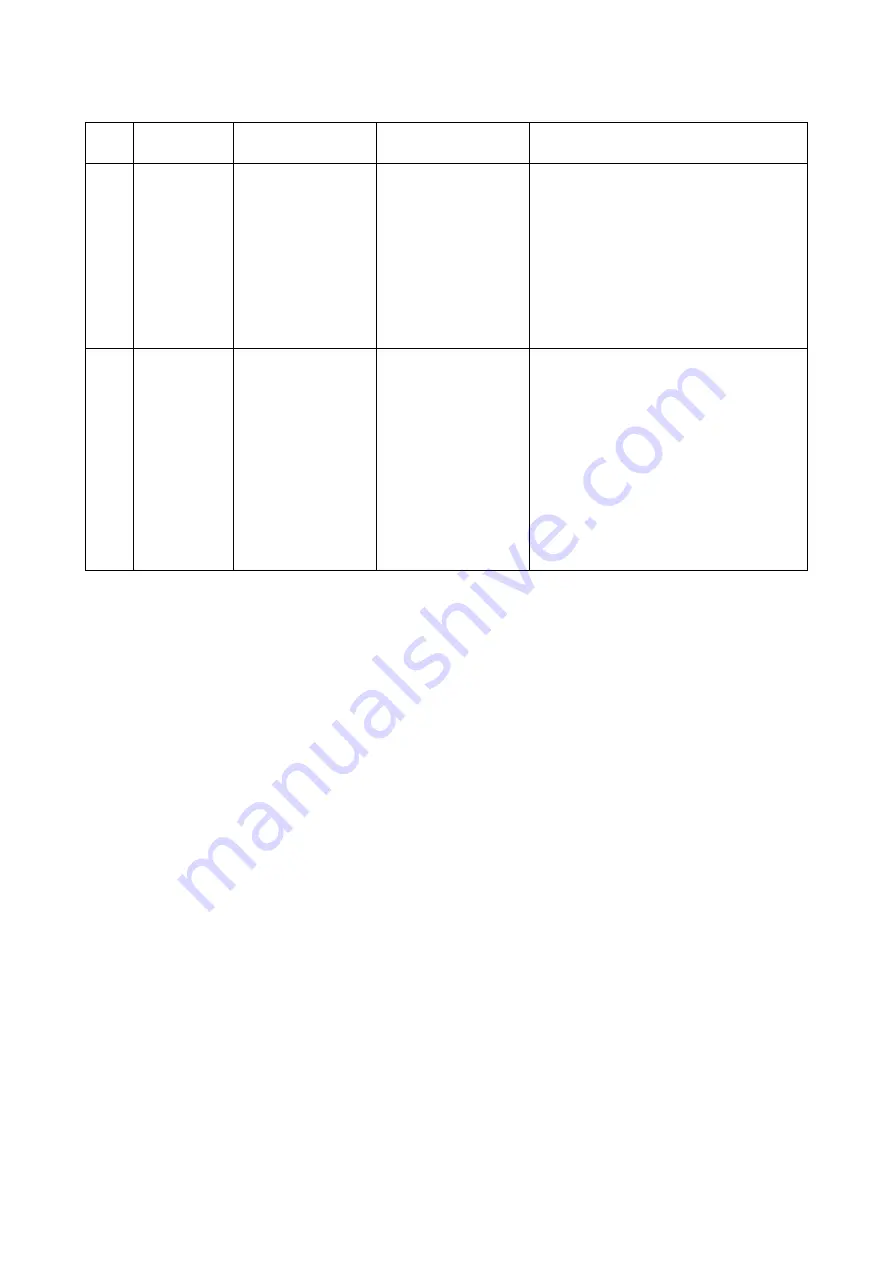
8
For Category 2 and Category 3 see table below.
Cat
Design of
Safety
Design
Requirements
Application
Zone of Use
2
High level of
safety
Safe with frequently
occu. Disturbances
or with an
operating fault
Where explosive
atmospheres are
likely to occur
Zone 1 - An atmosphere where
a mixture of air and flammable
substances in the form of gas, vapor
or mist is likely to occur in normal
operation occasionally.
Zone 21 - An atmosphere where a
cloud of combus- tible dust in the air
is likely to occur in normal operation
occasionally.
3
Normal level
of safety
Safe in normal
operation
Where explosive
atmospheres are
likely to occur
infrequently and be
of short duration
Zone 2 - An atmosphere where
a mixture of air and flammable
substances in the form of gas, vapor
or mist is not likely to occur in nor-
mal operation but, if it does occur, will
persist for only a short period.
Zone 22 - An atmosphere where a cloud
of combus- tible dust in the air is not
li- kely to occur in normal operation but,
if it does oc- cur, will persist for only a
short period.