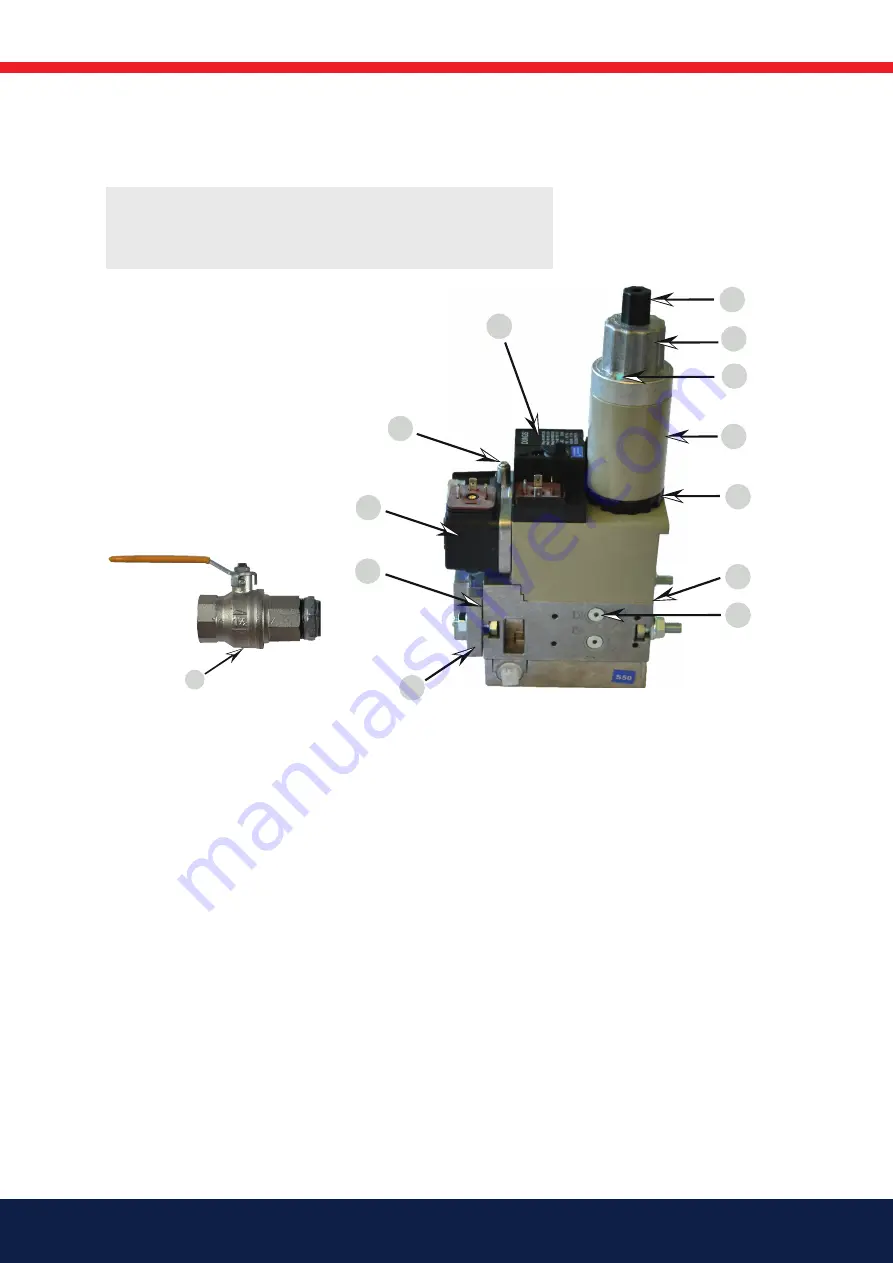
24
Bentone
!
All gasline components shall be assembled and mounted
without bending, torque and outher mechanical or thermal
stress.
1.
Gas pressure switch
2.
Inlet pressure
3.
Governor with pressure adjustment
4.
Hydraulic device, adjustment of stage 2
5.
Protective cover, start gas adjustment
6.
Lock screw for fl ow adjustment
7.
Main valve
8.
Knob for adjustment of stage 1
9.
Test nipple, pressure after governor
10. Test nipple for nozzle pressure
11.
Filter
12. Fixing fl ange
13.
Ball valve
7. Gas valve, MultiBloc ZRDLE 405-420
1
2
3
4
5
6
7
9
11
12
10
8
13
Max. inlet pressure: 360 mbar.
Adjustable governor pressure:
405 - 412 S50 = 4 - 50 mbar
415 - 420 S20 = 4 - 20 mbar
415 - 420 S50 = 20 - 50 mbar
Solenoid valve: Slow opening valves
with adjustable start load, stage 1 and
stage 2.
Turn to the left = the start gas fl ow is
increased.
172 515 11 2018-01-03
Содержание BG 300-2
Страница 26: ...26 Bentone 7 7 1 Pressure taps 1 2 3 4 5 1 8 screwed sealing plug 7 7 2 Electrical connection S 20 S 50...
Страница 42: ......
Страница 43: ......
Страница 44: ...Enertech AB P O Box 309 SE 341 26 Ljungby www bentone com...