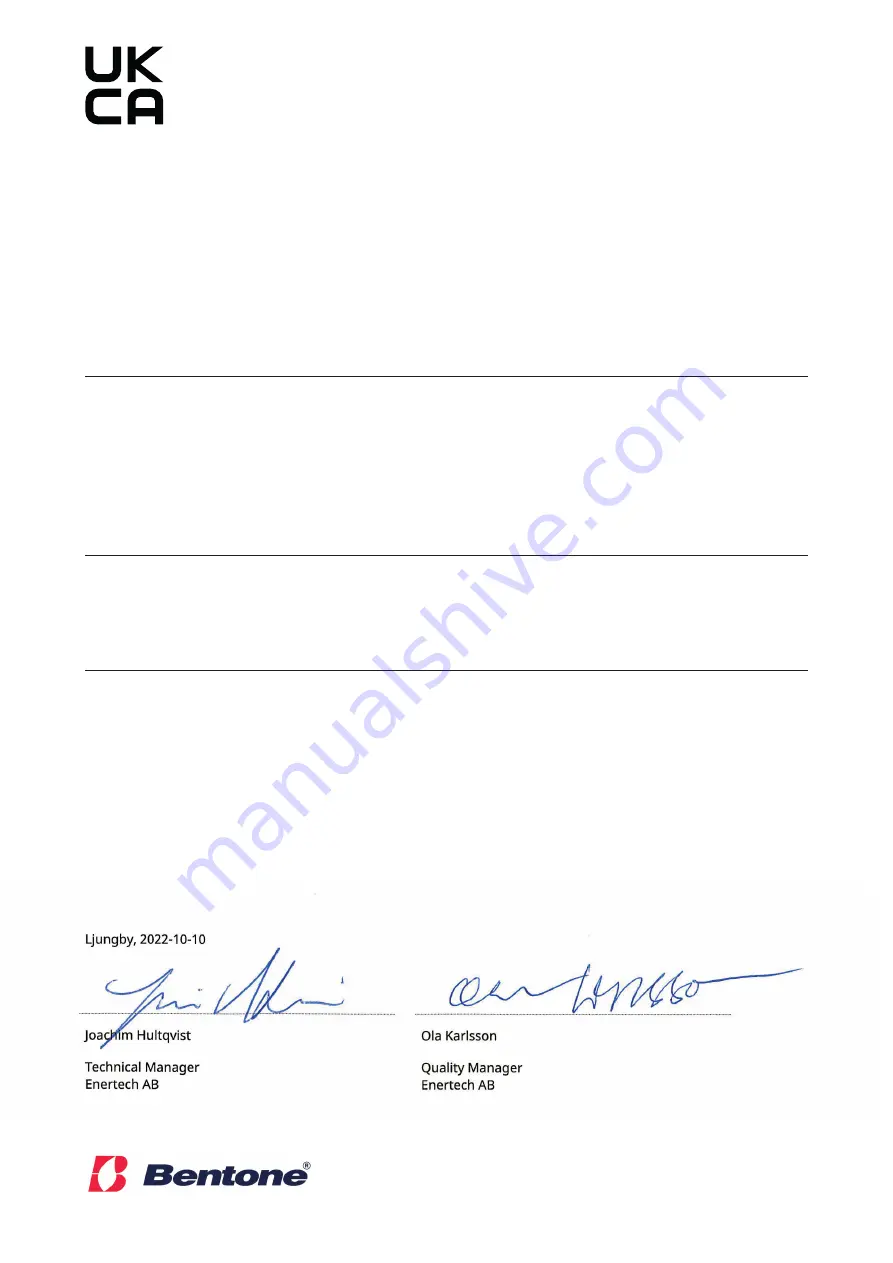
UK Declaration of conformity
Bentone Oil Burners
Type:
BF 1
ST 133
B 40
B 65
ST 108
ST 146
B 45
B 70
ST 120
B 30
B 55
B 80
This declaration of conformity is issued under the sole responsibility of the manufacturer.
The object of the declaration described above is in conformity with:
•
Supply of Machinery (Safety) Regulations 2008
•
Electromagnetic Compatibility Regulations 2016
•
The Restriction of the Use of Certain Hazardous Substances in Electrical and Electronic
Equipment Regulations 2012
References to the relevant harmonised standards used or references to the
other technical specifi cations in relation to which conformity is declared:
BS EN 267:2020
Excluding the requirements of Annex J/K.
Automatic forced draught burners for liquid fuels.
Manufacturer:
171 905 28-5 2022-10-10
Additional information can be downloaded at:
www.bentone.com
Enertech AB
Näsvägen 8
SE-341 34 LJUNGBY
Sweden
TUV SÜD BABT Unlimited
Octagon House,
Concorde Way, Segensworth North,
Fareham, Hampshire,
PO 15 5RL, United Kingdom
Approved Body Number: 0168
Approved Body:
Ljungby, 2022-10-10
Joachim Hultqvist
Ola Karlsson
Technical Manager
Enertech AB
Quality Manager
Enertech AB
Содержание B 40 A
Страница 18: ...18 Bentone 165 105 03 2 4 8 Handling and lifting instruction The lifting aid are available as spare parts...
Страница 41: ......
Страница 42: ......
Страница 43: ......
Страница 44: ...Enertech AB P O Box 309 SE 341 26 Ljungby www bentone com...