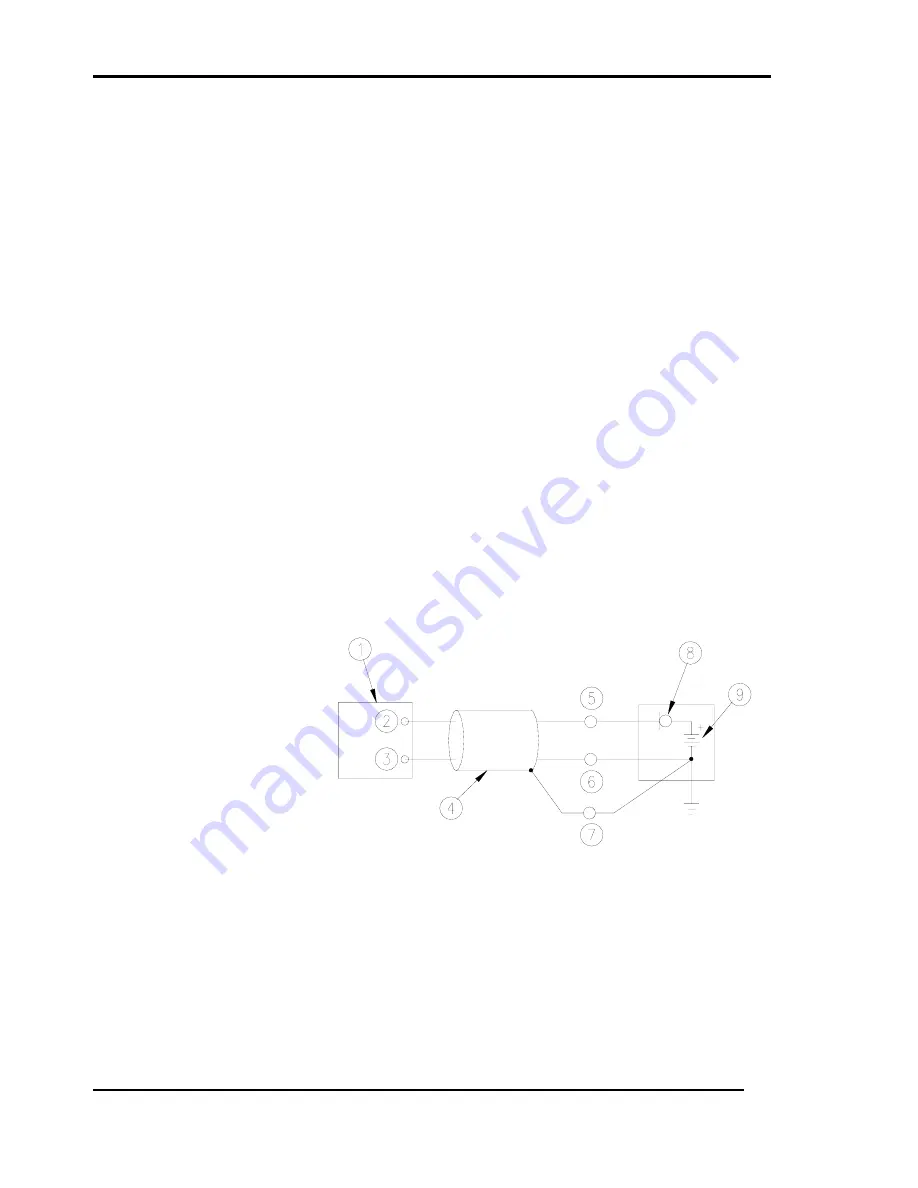
330500 Velomitor Sensor, 330525 Velomitor XA Sensor, 330530 Radiation Resistant Velomitor Sensor Operation Manual
2
The Velomitor® Sensor is designed to monitor vibration in frequencies ranging
from:
•
330500: 4.5 Hz to 5 kHz
•
330525: 4.5 Hz to 2 kHz
•
330530: 4.5 Hz to 5 kHz
The sensor has a calibrated sensitivity of 100 mV/in/s (4 mV/mm/s) and some of
the sensors can measure velocities up to 50 in/sec pk (1270 mm/s pk) – see the
specification section for details. The stainless steel casing protects the Velomitor®
Sensor in highly corrosive environments. The operating temperature range is from
-67°F to 250°F (-55°C to 121°C).
Traditional velocity sensors consist of either a moving wire coil surrounding a
fixed magnet or a fixed wire coil surrounding a moving magnet. The Velomitor®
Sensor is more accurate than traditional velocity sensors. Because the
Velomitor® Sensor contains no moving parts, it is also more durable and less
sensitive to transverse motion than traditional seismic transducers. Its
piezoelectric sensing element and solid-state circuitry let the Velomitor® Sensor
withstand years of continuous use.
The Velomitor® Sensor is a two-wire device that requires an external power
supply. The power supply must provide a DC voltage of 22 to 30 Volts and a
current of 10 mA. A constant current diode must be used to limit the current to
the sensor to 2.5 to 6 mA. Figure 1-1 shows a simple block diagram of the
Velomitor® Sensor system.
(1) Velomitor®
Sensor
(2) Pin A
(3) Pin B
(4) Shielded cable
(5) “A” white
(6) “B” black
(7) “SHLD”
(8) Constant current
source
(9) DC voltage supply
Figure 1-1.
The Velomitor® Sensor internal circuitry automatically sets the DC output bias
when a constant current is supplied. The DC bias and AC signal appears between
pins "A" and "B".
Artisan Technology Group - Quality Instrumentation ... Guaranteed | (888) 88-SOURCE | www.artisantg.com