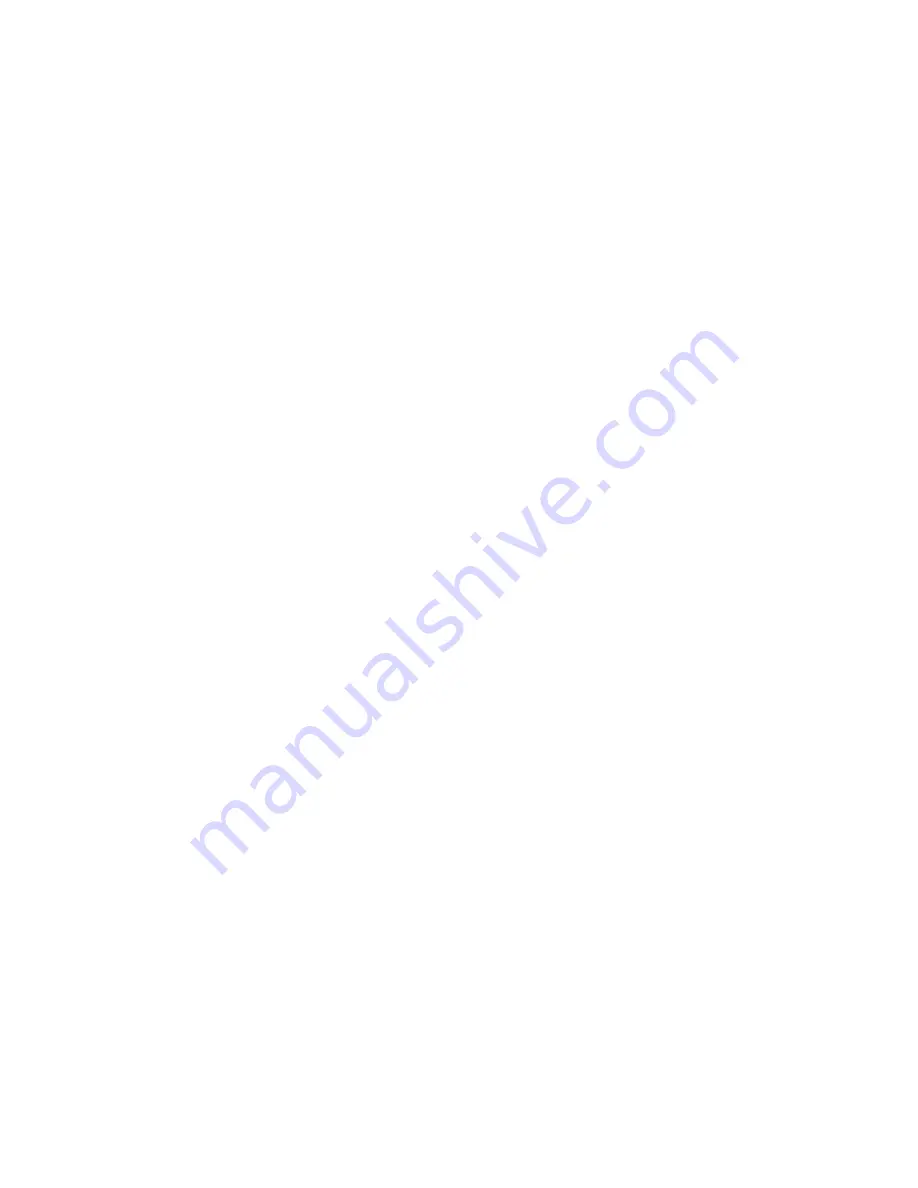
10
LEAKAGE TESTS
See the standard Air Brake System and Accessory Leakage
test on Page A-14 (Test 2).
Note: Leakage in the air supply system (components
before the supply reservoir - such as the governor, air dryer,
reservoir drain cocks, safety valve, and check valves) will
not be registered on the vehicle dash gauges and must
be tested separately.
Refer to the various maintenance
manuals for individual component leakage tests and the
Bendix “Test and Checklist” published in the Air Brake
System Handbook (BW5057) and on the back of the Dual
Circuit Brake System Troubleshooting Card (BW1396).
CYLINDER HEAD
Check for cylinder head gasket air leakage.
1. With the engine running, lower the air system pressure
to 60 psi and apply a soap solution around the cylinder
head. Check the gasket between the cylinder head
and valve plate assembly, the inlet reed valve/gasket
between the valve plate assembly and crankcase and
between the cylinder head and discharge jumper for
air leakage.
2. No leakage is permitted. If leakage is detected, replace
the compressor or repair the cylinder head using a
genuine Bendix
®
maintenance kit available from an
authorized Bendix
®
parts outlet.
INLET, DISCHARGE & UNLOADER
In order to test the inlet and discharge valves and the
unloader piston, it is necessary to have shop air pressure
and an assortment of fittings. A soap solution is also
required.
1. With the engine shut off, drain ALL air pressure from
the vehicle.
2. Disconnect the inlet and discharge lines and remove
the governor or its line or adapter fitting.
3. Apply 120 to 130 psi shop air pressure to the unloader
port and soap the inlet port. Leakage at the inlet port
should not exceed 50 sccm.
4. Apply 120 to 130 psi shop air pressure to the discharge
port and then apply and release air pressure to the inlet
port. Soap the inlet port and note that leakage at the
inlet port does not exceed 20 sccm.
If excessive leakage is noted in Tests 3 or 4, replace or
repair the compressor using genuine Bendix replacements
or maintenance kits available from any authorized Bendix
parts outlet.
While it is possible to test for inlet, discharge, and unloader
piston leakage, it may not be practical to do so. Inlet and
discharge valve leakage can generally be detected by
longer compressor build-up and recovery times. Compare
current compressor build-up times with the last several
recorded times. Make certain to test for air system
leakage — as described in the Service Operating Tests
section of this manual — before making a determination
that performance has been lost.
Unloader leakage is generally exhibited by excessive
compressor cycling between the loaded and unloaded
condition.
1. With service and supply system leakage below the
maximum allowable limits and the vehicle parked,
bring system pressure to governor cut-out and allow
the engine to idle.
2. The compressor should remain unloaded for a minimum
of 5 to 10 minutes. If the compressor cycling occurs
more frequently and service and supply system leakage
is within tolerance, replace the compressor or repair the
compressor unloader system using a genuine Bendix
maintenance kit available from authorized Bendix parts
outlets.
COMPRESSOR REMOVAL & DISASSEMBLY
GENERAL
The following disassembly and assembly procedure is
presented for reference purposes and presupposes that
a rebuild or repair of the compressor is being undertaken.
Several maintenance kits and service parts are available.
The instructions provided with these parts and kits should
be followed in lieu of the instructions presented here.
See
the Maintenance and Service Parts section in this manual.
REMOVAL
In many instances it may not be necessary to remove the
compressor from the vehicle when installing the various
maintenance kits and service parts. The maintenance
technician must assess the installation and determine the
correct course of action.
These instructions are general and are intended to be
a guide. In some cases additional preparations and
precautions are necessary. In all cases follow the
instructions contained in the vehicle maintenance manual
in lieu of the instructions, precautions and procedures
presented in this manual.
1. Block the wheels of the vehicle and drain the air
pressure from all the reservoirs in the system.
2. Drain the engine cooling system and the cylinder head
of the compressor. Identify and disconnect all air, water
and oil lines leading to the compressor.