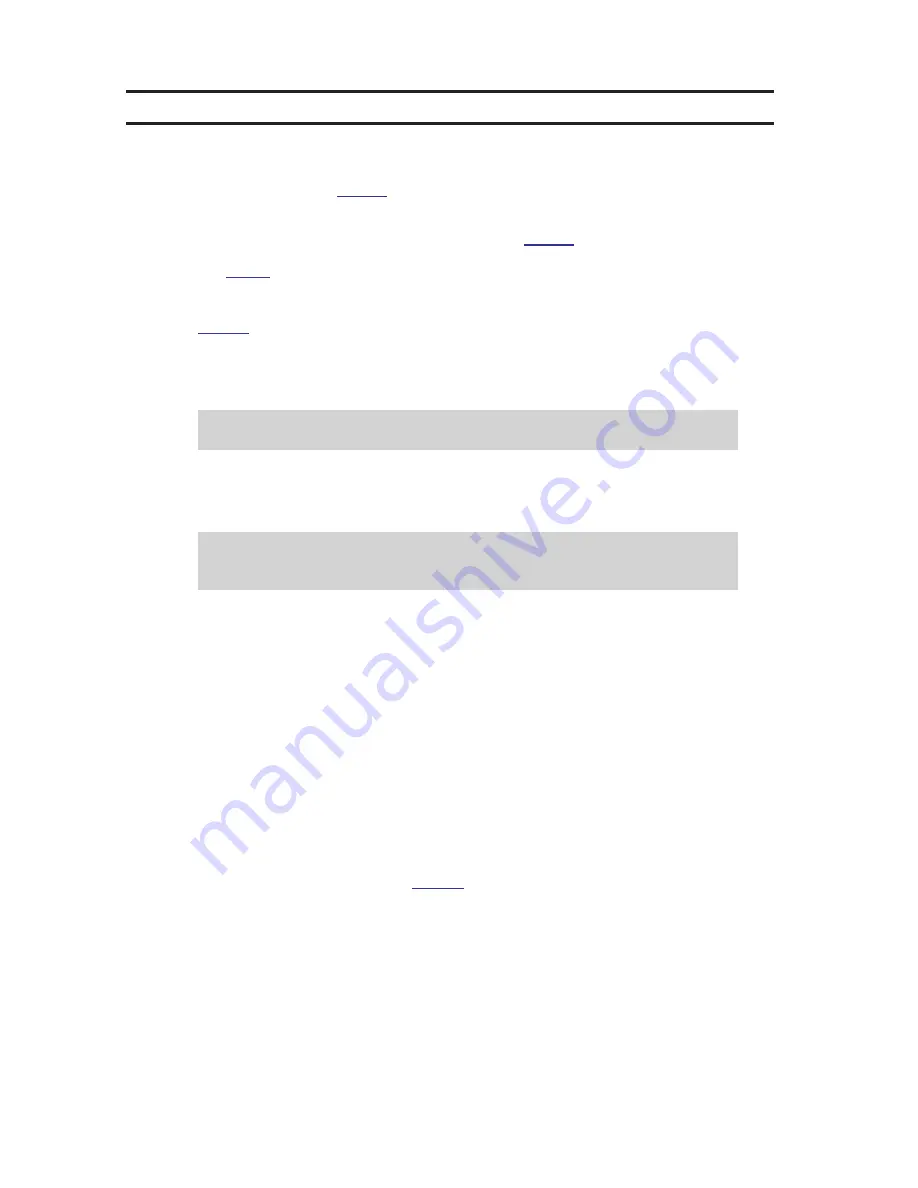
M-6200A Application Guide
–4–
3.0
External Connections
Terminal Block Assignments
The external connections to the control are made to the two terminal blocks located on the
rear of the control, see
Figure 3
. See "Terminal Block Assignments" later in this section for
a description of each terminal assignment. For example, if external dry contacts are being
used to control the Voltage Reduction Step #1 function, connections for these contacts
may be made between TB1-4 and TB1-7 as shown in
Figure 3
. The dry contact inputs for
non-sequential input, voltage reduction must be "wetted" by connecting to terminal TB1-4.
See
Table 1
.
Typical Connections
Figure 3
illustrates typical connections for a regulator control. Motor Power and sensing
voltage can be obtained from a common source or from an independent source having a
nominal 120 Vac output. Normally, this is line-to-neutral voltage, although line-to-line voltage
can be used if recognition is made of any phase shift between the voltage and current signals
when using line drop compensation.
CAUTIIO:
▲
The current input to the M-6200A is rated at 0.48 A continuous, and
4.0 A for 1 second.
Load current must be reduced by an appropriate auxiliary transformer to 0.2 A "full scale"
before connecting to the regulator current inputs.
Grounding
WAROIOG:
8
The protective earth grounding terminal must be connected to
the installation earth ground anytime external connections have
been made to the unit.
Ground the control by connecting a 14 AWG, 300 V min., 105° C green insulated wire inserted
in an Amp 51864-8 or equivalent ring connector wire to the marked protective earth terminal
located adjacent to either side of TB1. Connect to the installation ground.
Unit Isolation
Sensing inputs should be equipped with test switches and shorting devices where necessary
to isolate the unit from external potential or current sources.
A switch or circuit breaker for the M-6200A's power shall be included in the building
installation, and shall be in close proximity to the control and within easy reach of the
operator, and shall be plainly marked as being the power disconnect device for the control.
Torque Requirements
Terminals TB1-1-16 & TB2-1-12: 7.5 in-lbs, minimum and 8.0 in-lbs, maximum.
Control Power Backup Input Connection
The Control Power Backup Input (
Figure 4
) is designed to sustain communication port
operation in the event of the loss of AC control power. In the event of a loss of AC input
power to the control, this feature permits uninterrupted operation of the control by supplying
+12 Vdc to the control. In addition, the control retains functionality with the exception of the
actual operation of the tapchanger mechanism.
When the AC input voltage drops below approximately 85 Vrms, the Control Power Backup
Input will activate and all automatic tapchange operations will then be suspended. If Motor
Power is available, manual tapchanges may be initiated.
When the control is being powered only by the backup DC input the Auto/Manual switch
status and the Local/Remote switch status are functional. When a control is being supplied
by both AC and DC via the backup power input and the backup DC input is lost the unit will
report it via DNP.