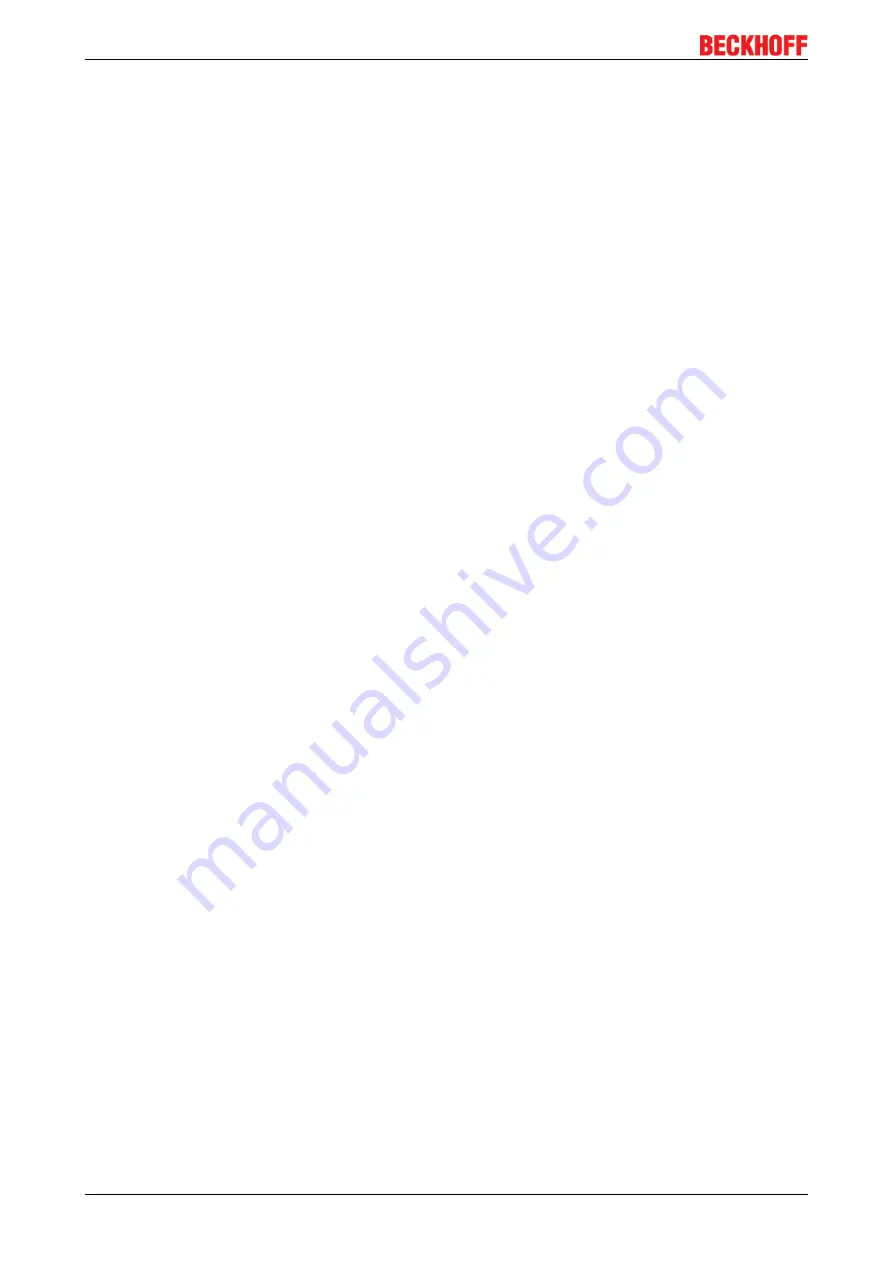
PROFIBUS
BC3150
82
Version: 2.1.0
that it is ready for data exchange. Depending on the extent of the calculations that the slave must carry out
after receiving the parameter and configuration data, it can take up to a few seconds before it is ready for
data exchange. For this reason the slave possesses the following states:
Parameter data
The parameter data is sent from the master to the slave in the SetPrmLock request telegram. The
SetPrmLock response telegram does not contain any data, and therefore consists of a single byte, the short
acknowledgement. The parameter data consists of DP parameters (e.g. the setting of the DP watchdog or
checking the IdentNumber (unique to each DP device)), of DPV1-/DPV2 parameters and of application-
specific parameters that only have to be transmitted once during the StartUp. If an error is found in the
parameter data, this is indicated in the diagnostic data, and the slave either remains in or enters the WAIT-
PRM state.
Configuration data
The configuration data is sent from the master to the slave in the ChkCfg request telegram. The ChkCfg
response telegram does not contain any data, and therefore consists of a single byte, the short
acknowledgement. The configuration data describes the assignment of the DP modules to the cyclic I/O data
that is to be exchanged between the master and slave via the Data_Exchange telegram in the cyclic data
exchange phase. The sequence of the DP modules added to a slave in the DP configuration tool determines
the sequence of the associated I/O data in the Data_Exchange telegram.
Diagnostic data
The diagnostic data is requested by the master using a SlaveDiag request telegram without any data. The
slave replies with the diagnostic data in a SlaveDiag response telegram. The diagnostic data consists of the
standard DP diagnostics (e.g. the state of the slave, the IdentNumber) and of application-specific diagnostic
data.
Cyclic data exchange
At the core of the PROFIBUS DP protocol is the cyclic data exchange, during which the master exchanges I/
O data with each slave within a PROFIBUS DP cycle. This involves the master sending the outputs to each
slave with a DataExchange request telegram, while the slave replies with the inputs in a DataExchange
response telegram. This means that all the output and/or input data is transmitted in one telegram, in which
the DP configuration (the sequence of DP modules) specifies the assignment of the output and/or input data
to the slave's actual process data.
Diagnosis during cyclic data exchange
A slave can send a diagnostics signal to the master during cyclic data exchange. In this case, the slave sets
a flag in the DataExchange response telegram, whereby the master recognizes that there is new diagnostic
data in the slave. It then fetches that data in the SlaveDiag telegram. The diagnostic data is therefore not
available in real-time as the cyclic I/O data in the controller, but always delayed by at least one DP cycle.
Synchronization with Sync and Freeze
The Sync and Freeze commands in the GlobalControl request telegram (broadcast telegram) allow the
master to synchronize the activation of the outputs (Sync) or the reading of the inputs (Freeze) in a number
of slaves. When the Sync command is used, the slaves are first switched into Sync mode (a process that is
acknowledged in the diagnostic data). The I/O data is then exchanged sequentially with the slaves in the
DataExchange telegram. Transmitting the Sync command in the GlobalControl telegram then has the effect
of causing the slaves to generate the most recently received outputs. In Freeze operation a Freeze
command is first sent in the GlobalControl telegram, in response to which all the slaves latch their
inputs. These are then fetched sequentially by the master in the DataExchange telegram.
States in the master
The master distinguishes between the CLEAR state (all outputs are set to the Fail_Safe value) and the
OPERATE state (all outputs have the process value). The Master is usually switched into the CLEAR mode
when, for instance, the PLC enters STOP.
Содержание BC3150
Страница 1: ...Documentation BC3150 Bus Terminal Controller for PROFIBUS DP 2 1 0 2017 07 11 Version Date...
Страница 2: ......
Страница 45: ...Parameterization and Commissioning BC3150 45 Version 2 1 0 Fig 41 Sample for entering associated bytes...
Страница 57: ...Programming BC3150 57 Version 2 1 0 Fig 55 Build...
Страница 87: ...PROFIBUS BC3150 87 Version 2 1 0 Fig 78 RS485 topology with 3 segments and 2 repeaters...