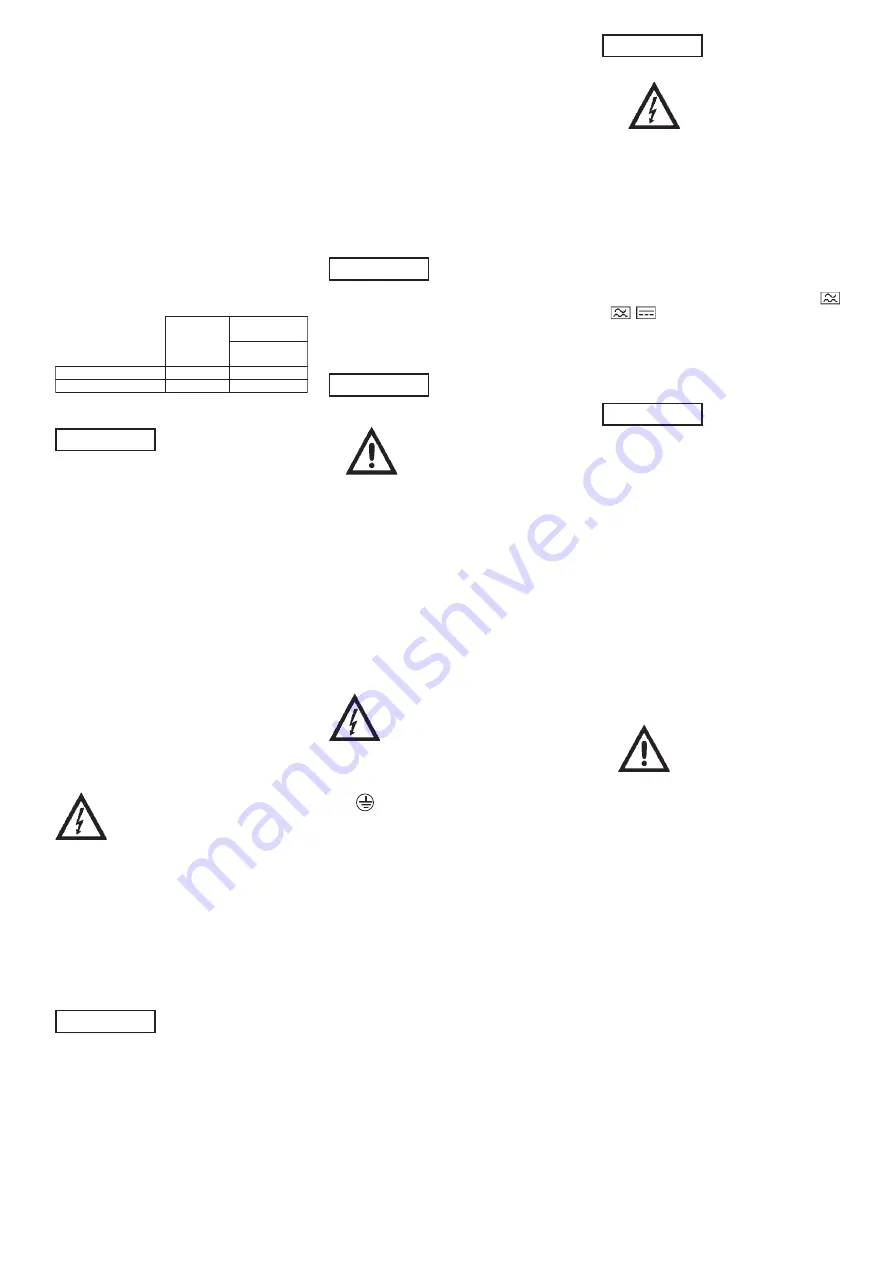
11
• The direction of flow of the media must match
the direction triangle on the pump housing
(fig. 1a, pos. 2).
•
Only
installation positions
as shown in fig.
2 are permitted. The pump shaft must be
horizontal.
When installing in confined spaces, for example
in compact distributors, the control module can
be placed in a vertical position by rotating the
motor, see chapter 5.1.2.
•
Install the pump in an easily accessible place,
so that subsequent servicing work can easily be
carried out.
Installation is to be carried out such that dripping
water cannot drip onto the pump motor or control
module.
Sufficiently long screws are to be used:
When fitting bolting flanges,
make sure the screws are of
sufficient length. The screw
thread must protrude from
the nut by at least one turn
(fig. 3, pos. 2).
5.1.1 Removing/installing the control
module
The control module can be separated from the
motor by loosening 2 screws (fig. 4):
•
Loosen terminal box lid screws (pos. 1),
•
Remove terminal box lid (pos. 2),
•
Remove sealing stopper using a suitable tool,
avoid damaging the stopper (pos.3),
•
Loosen 2 M5 hexagon socket screws (SW4)
(pos. 4),
•
Remove control module from motor (pos. 5),
•
To install, reverse the above sequence.
If the pump is running off a generator
(rotor driven by admission pressure
pump), a dangerous voltage is crea-
ted at the motor terminals after the
control module is removed.
The motor terminals are designed
as VDE-approved bushings, so that
there is no danger if simply touched
with the finger. However, there would
be a danger if a pointed object (nail,
screwdriver, wire) were poked into
one of the bushings.
For easy installation there are 2 or 3 (depending
on pump type) pilot pins on the back of the control
module which snap into corresponding holes in
the motor housing. Only when these pilot pins
have secured the control module to the motor
housing does the central earthing pin and then
the winding pins make contact (fig. 4).
Between the motor housing
and the control module there
is a flat seal (fig. 4, pos. 6)
which is responsible for the
thermal decoupling of the
two components. This seal
must always be placed bet-
ween the module and the
motor when installing the
control module.
5.1.2 Removing/installing the motor
impeller unit
To remove the motor, 4 M6 hexagon socket screws
(SW5) must be loosened. These screws can be
reached with the following tools (fig. 5, pos. 2):
•
90° offset socket-head screwdriver
•
spherical head socket-head screwdriver
• 1/4” reversing ratchet with suitable bit
If only the control module is to be moved into a
different position, the motor does not need to
be completely removed from the pump housing.
The motor can be turned to the desired position
in the pump housing, provided there is sufficient
room available.
Be careful not to damage the
O-ring situated between the
motor head and the pump
housing. The O-ring must lie
untwisted in the bevel of the
end shield pointing to the
impeller.
The shaft is inextricably
linked to the impeller, the end
shield and the rotor. This unit
is secured against unintentional
removal from the motor. If the
rotor with its strong magnets
is not in the motor housing, it
has a considerable potential
for danger e.g. by suddenly
attracting objects made from
iron/steel, influencing electrical
equipment (risk to people with
pace-makers), destroying
magnetic cards, etc..
If the accessibility of the screws on the motor flan-
ge is not guaranteed, the control module can be
separated from the motor by loosening 2 screws,
see chapter 5.1.1.
5.2.
Electrical connection
Electrical connection should be
made by a qualified electrician.
Current national regulations must
be observed.
5.2.1. Electrical pump connection
(Figure 6)
L, N,
Mains voltage: single-phase current
1 ~ 230 VAC, 50 Hz, DIN IEC 60038.
•
According to Part 1 of the VDE 0730, the pump
must be connected to the electrical supply by a
solid wire (3 x 1,5mm
2
minimum cross-section)
equipped with a plug or an all-pole switch. The wi-
dth of the contact gap must be at least 3 mm.
•
No motor protection is required. If this is already
present in the installation, it is be bypassed or
set to the maximum possible current value.
•
To guarantee protection against dripping water
and the grip of the cable gland, cables with an
adequate outer diameter are to be used and
screwed sufficiently tightly. In addition, the ca-
bles in the vicinity of the cable gland are to be
bent into a run-off loop to drain off any dripping
water. Unoccupied cable glands are to be closed
with the available sealing plastic washers and
made sufficiently tight.
•
To adapt the connecting leads to the inner
diameter of the cable entries, the seals consist
of concentric rubber rings, the inner one(s) of
which can be removed if required.
Cables of an appropria-
te outer diameter are to
be used, so that the cable
gland is sealed after being
tightened. Unused cable
glands are sealed with a
plastic washer. This washer
must not be removed. Even
unused cable glands are to
be tightened.
• When using the pump in systems where the
water temperature exceeds 90 °C, a connecting
pipe with corresponding heat resistance must
be used.
•
The connecting lead must be laid in such a way
that it never touches the pipework and/or the
pump and motor casing.
•
This pump may be protected with an FI
safety switch. Identification symbol: FI -
or
• Check that the mains current and voltage com-
ply with the data on the rating plate.
•
Mains fuse: see rating plate
•
Pump/installation must be earthed in compliance
with regulations.
In insulation tests with a
high-voltage generator the
pump is to be disconnected
on all poles from the mains
in the control module. The
free cable ends are to be
insulated in accordance
with the voltage of the high-
voltage generator.
6. Operation
6.1 Filling and venting the unit
The system must be filled and ventilated properly.
The pump rotary box is ventilated automatically
after operating for a brief time. Brief dry running
will not damage the pump.
Depending on the operating condi-
tion of the pump and/or installation
(fluid temperature) the entire pump
can become very hot.
Avoid touching the pump owing
to the risk of burning. The tem-
perature at the heat sink can be
up to 70°C within the permissi-
ble operating conditions.
6.2 Setting the pump power
The unit is set to a specific operating point (point
of maximum load, calculated maximum heating
requirements). When starting up for the first time,
the pump capacity (delivery head) is to be set in
accordance with the system operating point. The
factory presetting does not correspond to the
pumping capacity required for the system. It is
calculated on the basis of the characteristics
diagram of the selected pump (from the catalo-
gue/ data sheet). See also Figs 11 to 12.
g
n
i
d
a
e
r
T
w
e
r
c
s
.
n
i
m
h
t
g
n
e
l
/
0
5
N
D
5
6
N
D
6
N
P
d
n
e
d
e
g
n
a
l
F
2
1
M
m
m
0
6
0
1
N
P
d
n
e
d
e
g
n
a
l
F
6
1
M
m
m
0
5
¡ATTENTION!
¡ATTENTION!
¡ATTENTION!
¡ATTENTION!
¡ATTENTION!
¡ATTENTION!
ATC
ROC