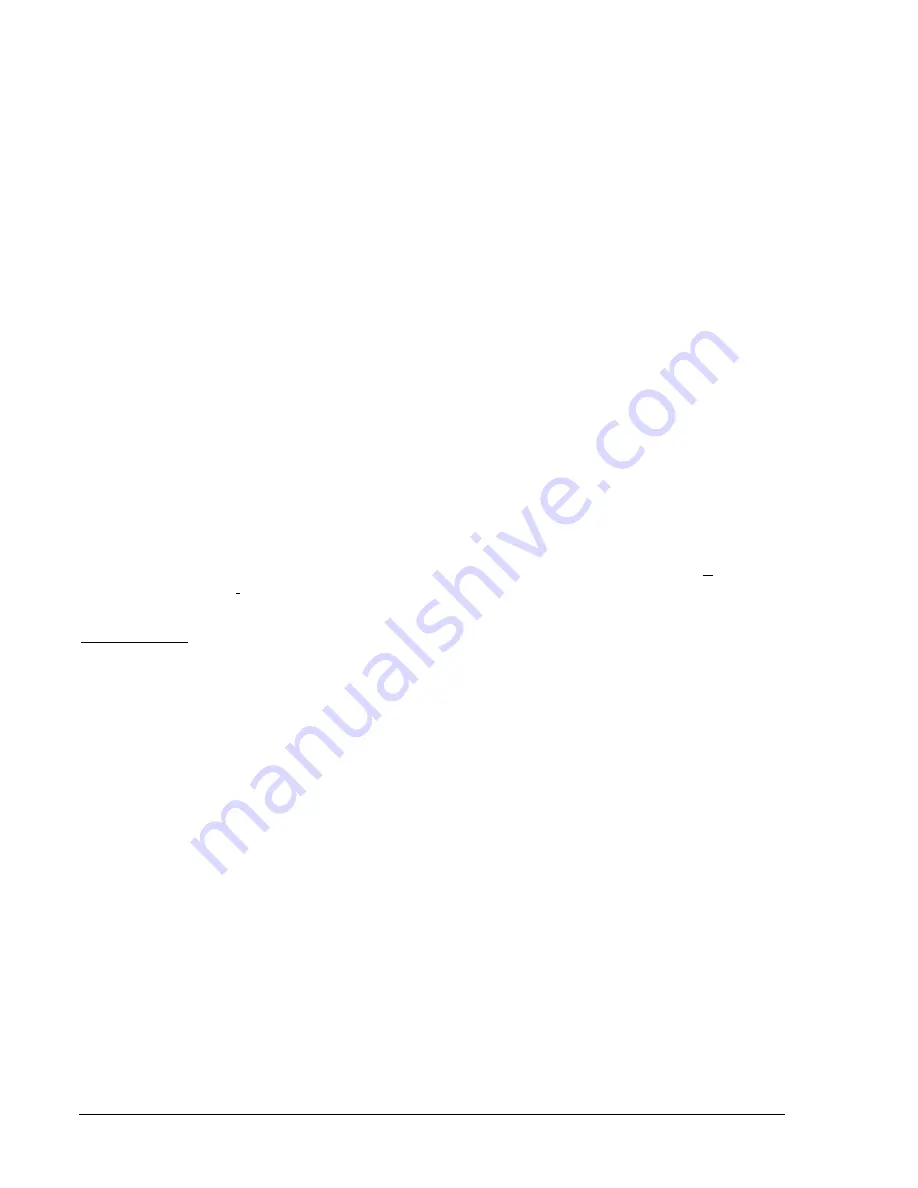
CANBus/J1939 Interface - Enable ECU Support.
This setting enables and disables the DGC-500 CAN
interface. When enabled, the CAN interface allows the DGC-500 to communicate with the engine control
unit (ECU). This setting must be enabled in order to enable DTC support.
CANBus/J1939 Interface - Enable DTC Support.
This setting enables and disables the viewing of
diagnostic trouble codes (DTCs) reported by the ECU. Both the Enable ECU Support and Enable DTC
Support settings must be enabled to view DTCs.
CANBus/J1939 Interface - Unit CANBus Address.
This setting selects the address to be used by the
DGC-500 for J1939 communication. A value of 0 to 253 may be entered.
CANBus/J1939 Interface - Engine Start/Stop Config.
This setting selects one of two engine start/stop
configurations. Selecting Volvo Penta configures the DGC-500 for starting and stopping of the engine
using the J1939 communication interface. (The Enable ECU Support setting must be enabled.) Selecting
Not Configured disables this feature.
CANBus/J1939 Interface - Speed Select.
This setting tells the Volvo Penta EDC III to operate the engine
at the primary or secondary base speed. If the engine is configured by Volvo for 60 hertz applications, the
primary base speed is 1,800 rpm and the secondary base speed is 1,500 rpm. If the engine is configured
by Volvo for 50 hertz applications, the primary base sped is 1,500 rpm and the secondary base speed is
1,800 rpm. This setting is enabled only when Volvo Penta is selected as the Start/Stop Config. Setting.
CANBus/J1939 Interface - Accelerator Position.
This setting, expressed as a percentage, tells the Volvo
Penta EDC III where to set the engine speed (trim) relative to the base speed. The range of the setting is
the base speed ±120 rpm. A setting of 0% will cause the engine to run at 120 rpm below the base speed,
a setting of 50% will cause the engine to run at the base speed, and a setting of 100% will cause the
engine to run at 120 rpm above the base speed. The Accelerator Position setting is linear with a gain of
2.4 rpm/%. This setting in not saved in nonvolatile memory and defaults back to 50% after DGC-500
operation power is cycled. This setting is enabled only when Volvo Penta is selected as the Start/Stop
Config. setting.
Programmable Inputs and Outputs
Click the
PROG I/O
button to access the Programmable Inputs and Outputs screen or click
Screens
on
the menu bar and click
Input/Output Settings
.
The Programmable Inputs and Outputs screen consists of two tabs: Input Setup and Output Setup.
Input Setup Tab
The Input Setup tab settings of the Programmable Inputs and Outputs screen consist of three identical
groups of settings for each of the three programmable inputs. Tab settings are shown in Figure 4-15.
Each tab setting is described in the following paragraphs.
Programmable Input - Function.
This setting selects the function type that is used to trigger the
corresponding programmable input. The functions available for triggering a programmable input are listed
below.
•
Auto Transfer Switch
•
Auxiliary Input
•
Battery Charger Fail
•
Fuel Leak Detect
•
Low Coolant Level
•
No Function
•
Single-Phase Override
Programmable Input - Alarm/Pre-Alarm.
Either of these check boxes can be selected to annunciate an
alarm or pre-alarm when the selected function triggers the programmable input. Alarm or pre-alarm
annunciation is available only when one the following functions are selected: Auxiliary Input, Battery
Charger Fail, Fuel Leak Detect, or Low Coolant Level.
Programmable Input - Auxiliary Input Label.
This setting field is active only when Auxiliary Input is
selected as the programmable input function. An user-assigned label (eight characters, maximum) can be
entered for the corresponding programmable input.
4-12
DGC-500 BESTCOMS Software
9355400990 Rev H
Содержание DGC-500
Страница 1: ...INSTRUCTION MANUAL FOR DIGITAL GENSET CONTROLLER DGC 500 Publication 9355400990 Revision H 02 14...
Страница 2: ......
Страница 8: ...This page intentionally left blank vi DGC 500 Introduction 9355400990 Rev H...
Страница 10: ...This page intentionally left blank viii DGC 500 Introduction 9355400990 Rev H...
Страница 12: ...This page intentionally left blank ii DGC 500 General Information 9355400990 Rev H...
Страница 20: ...This page intentionally left blank 1 8 DGC 500 General Information 9355400990 Rev H...
Страница 22: ...This page intentionally left blank ii DGC 500 Human Machine Interface 9355400990 Rev H...
Страница 25: ...Figure 2 2 Rear Panel HMI 9355400990 Rev H DGC 500 Human Machine Interface 2 3...
Страница 28: ...This page intentionally left blank 2 6 DGC 500 Human Machine Interface 9355400990 Rev H...
Страница 51: ...Figure 3 9 Menu 1 Navigation 9355400990 Rev H DGC 500 Functional Description 3 21...
Страница 52: ...Figure 3 10 Menu 2 Navigation 3 22 DGC 500 Functional Description 9355400990 Rev H...
Страница 53: ...Figure 3 11 Menu 3 Navigation 9355400990 Rev H DGC 500 Functional Description 3 23...
Страница 66: ...Figure 3 28 Alarm State Diagram 3 36 DGC 500 Functional Description 9355400990 Rev H...
Страница 96: ......
Страница 98: ...This page intentionally left blank ii DGC 500 Installation 9355400990 Rev H...
Страница 118: ...This page intentionally left blank ii DGC 500 Maintenance and Troubleshooting 9355400990 Rev H...
Страница 122: ...This page intentionally left blank ii DGC 500 Time Overcurrent Characteristic Curves 9355400990 Rev H...
Страница 152: ...This page intentionally left blank C 6 DGC 500 Settings Record 9355400990 Rev H...
Страница 153: ......