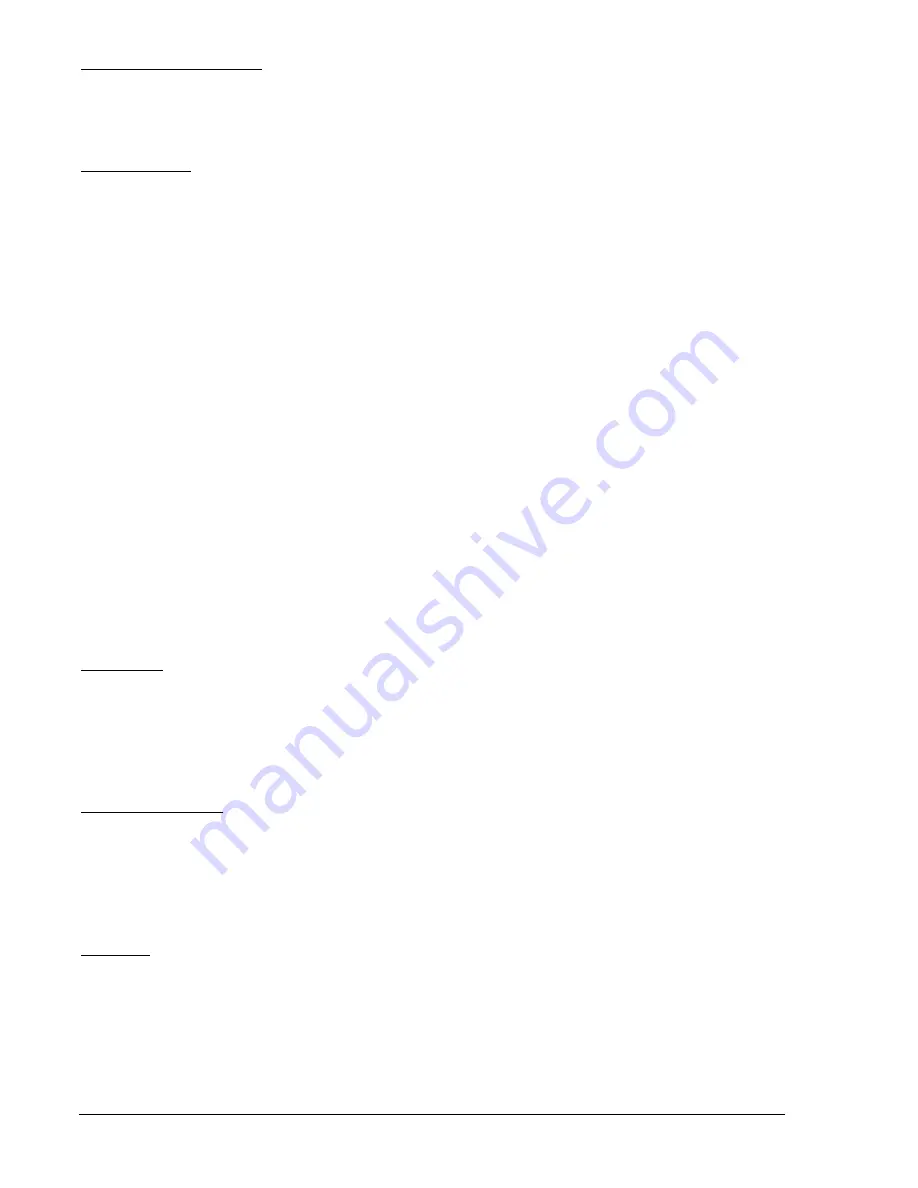
Analog-to-Digital Converter
Scaled and conditioned signals representing the sensing voltage, sensing current, coolant temperature,
fuel level, oil pressure, and battery voltage are digitized by the microprocessor’s 10-bit analog-to-digital
converter. The digitized information is stored in random access memory (RAM) and used by the
microprocessor for all metering and protection functions.
Watchdog Timer
The watchdog timer monitors the firmware executed by the microprocessor. If the firmware ceases normal
operation, the watchdog timer will reset the microprocessor. After reset, the microprocessor will resume
normal operation if the condition that caused the watchdog reset is no longer present. If the condition is
still present, the unit will reset repeatedly until normal operation is resumed or until the watchdog count
reaches five. If the count reaches five, the unit will go to watchdog lockout mode. If a half-hour elapses
after the most recent reset and the watchdog count has not reached five, the watchdog count is cleared.
Once the unit enters the watchdog lockout mode, a power cycle is required to clear the lockout.
Voltage Sensing Inputs
Generator voltages applied to the voltage sensing inputs are scaled to levels suitable for use by the
internal circuitry. Voltage sensing configuration is menu-selectable.
The voltage sensing inputs accept a maximum voltage of 576 Vrms, line-to-line. Sensing voltage is
applied to terminals P23 (A-phase), P26 (B-phase), P29 (C-phase), and P30 (Neutral).
Current Sensing Inputs
Generator currents are sensed and scaled to values suitable for use by the internal circuitry. Isolation is
provided by internal current transformers (CTs).
DGC-500–X1 units accept a maximum current value of 1 Aac. DGC-500–X5 units accept a maximum
current value of 5 Aac. Sensing current is applied to terminals P10 and P11 (A-phase), P12 and P14 (B-
phase), and P15 and P17 (C-phase).
Transducer Inputs
Programmable transducer inputs give the DGC-500 user the flexibility to select the transducer to be used
in an application. Information about programming the transducer inputs is provided in Section 4,
BESTCOMS Software.
Oil Pressure
A current of less than 30 milliamperes is provided to the oil pressure transducer. The developed voltage is
measured and scaled for use by the internal circuitry. Oil pressure transducers that are compatible with
the DGC-500 include Isspro model R8919, Stewart-Warner models 279BF, 279C, 411K, and 411M, and
VDO models 360025 and 360811. Other senders may be used. BESTCOMS software allows for the
programming of sender characteristics. See Section 4,
BESTCOMS Software
for more information.
Oil pressure transducer connections are provided at terminals P13 and P19 (sender common).
Coolant Temperature
A current of less than 1.2 milliamperes is provided to the coolant temperature transducer. The developed
voltage is measured and scaled for use by the internal circuitry. Coolant temperature transducers that are
compatible with the DGC-500 include Isspro model R8959 and Stewart-Warner 334-P. Other senders
may be used. BESTCOMS software allows for the programming of sender characteristics. See Section 4,
BESTCOMS Software
for more information.
Coolant temperature transducer connections are provided at terminals P18 and P19 (sender common).
Fuel Level
A current of less than 5 milliamperes is provided to the fuel level transducer. The developed voltage is
measured and scaled for use by the internal circuitry. An open circuit or short circuit across the fuel level
transducer terminals will cause the DGC-500 to indicate a failed fuel level transducer. Fuel level
transducers that are compatible with the DGC-500 include Isspro model R8925. Other senders may be
used. BESTCOMS software allows for the programming of sender characteristics. See Section 4,
BESTCOMS Software
for more information.
Fuel level transducer connections are provided at terminals P16 and P19 (sender common).
3-2
DGC-500 Functional Description
9355400990 Rev H
Содержание DGC-500
Страница 1: ...INSTRUCTION MANUAL FOR DIGITAL GENSET CONTROLLER DGC 500 Publication 9355400990 Revision H 02 14...
Страница 2: ......
Страница 8: ...This page intentionally left blank vi DGC 500 Introduction 9355400990 Rev H...
Страница 10: ...This page intentionally left blank viii DGC 500 Introduction 9355400990 Rev H...
Страница 12: ...This page intentionally left blank ii DGC 500 General Information 9355400990 Rev H...
Страница 20: ...This page intentionally left blank 1 8 DGC 500 General Information 9355400990 Rev H...
Страница 22: ...This page intentionally left blank ii DGC 500 Human Machine Interface 9355400990 Rev H...
Страница 25: ...Figure 2 2 Rear Panel HMI 9355400990 Rev H DGC 500 Human Machine Interface 2 3...
Страница 28: ...This page intentionally left blank 2 6 DGC 500 Human Machine Interface 9355400990 Rev H...
Страница 51: ...Figure 3 9 Menu 1 Navigation 9355400990 Rev H DGC 500 Functional Description 3 21...
Страница 52: ...Figure 3 10 Menu 2 Navigation 3 22 DGC 500 Functional Description 9355400990 Rev H...
Страница 53: ...Figure 3 11 Menu 3 Navigation 9355400990 Rev H DGC 500 Functional Description 3 23...
Страница 66: ...Figure 3 28 Alarm State Diagram 3 36 DGC 500 Functional Description 9355400990 Rev H...
Страница 96: ......
Страница 98: ...This page intentionally left blank ii DGC 500 Installation 9355400990 Rev H...
Страница 118: ...This page intentionally left blank ii DGC 500 Maintenance and Troubleshooting 9355400990 Rev H...
Страница 122: ...This page intentionally left blank ii DGC 500 Time Overcurrent Characteristic Curves 9355400990 Rev H...
Страница 152: ...This page intentionally left blank C 6 DGC 500 Settings Record 9355400990 Rev H...
Страница 153: ......