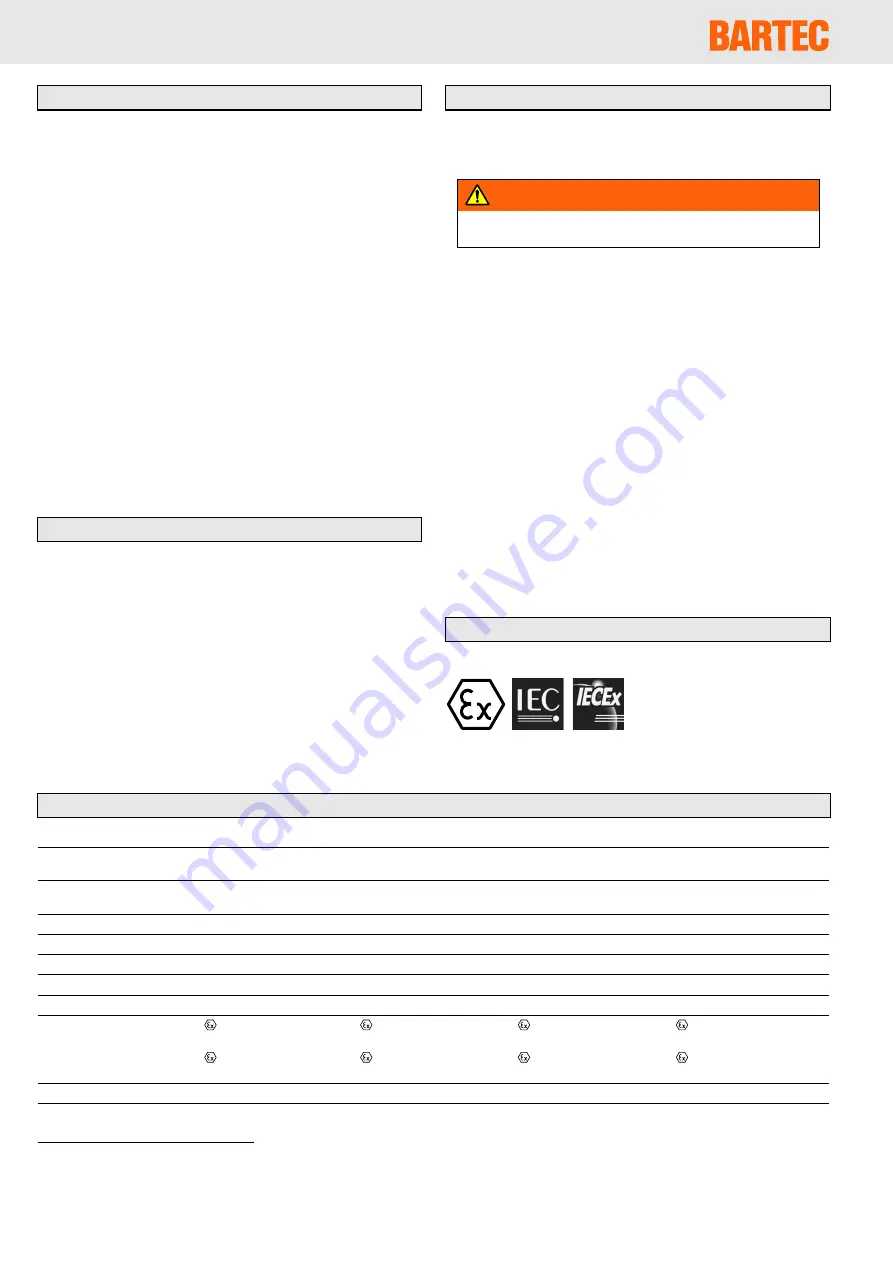
01-5800-7N0012/-
05/2019-EHT-432712
Notice
Technical data subject to change without notice.
No claims for damage arising from alternations, errors or misprints shall be allowed.
Page 5 / 46
Applications
Trace heating compensates for the heat loss through the thermal insula-
tion to maintain the pipe and fluid at temperatures above the freezing or
solidification point in systems that are expected to have stagnant fluids for
prolonged durations.
Freeze protection:
Water, and fluids containing significant water, expand as they freeze.
This expansion can cause the pipe to be blocked or break leading to:
▪
Economic losses: A frozen water pipe leading to a critical process
like a frozen pipe in a waste water treatment plant or cooling tower
can shut down the operation causing high economic losses.
▪
Safety issues: A frozen pipe to safety showers can jeopardize
personnel safety in the event of hazardous chemical exposure.
Temperature maintenance:
A process temperature maintenance system can maintain the tem-
perature of the fluid in a pipe to the desired level over a broad range
of temperatures.
Maintaining liquids within the specified temperature range allows you
to cost-effectively transport the fluids from one location to another,
operate your processes at maximum efficiencies, and safely start/shut
down your operations.
Personnel requirements
The personnel executing installation and maintenance tasks must have
acquired the skills and specialized knowledge relating to the types of
protection and types of devices concerned. At least, the personnel must
have:
▪
a general understanding of the relevant electrical engineering
▪
a practical understanding of the principles and techniques of explo-
sion protection
▪
a working knowledge and understanding of the relevant standards
of explosion protection
a basic knowledge of quality assurance, including the principles of
auditing documentation, traceability of measurements and calibration
of measurement instruments.
Safety
For safe installation and operation of BARTEC Self regulating trace
heating systems the technical requirements and instructions given in
this manual must be followed.
WARNING
Risk of fire or electrical shock. Follow these guidelines to avoid
personal injury or material damage.
▪
All electrical systems and installations must comply with BARTEC
GmbH requirements and be installed in accordance with the relevant
electrical codes and any other applicable national and local codes.
▪
BARTEC GmbH and many international electrical and safety codes
require ground fault protection to be provided for all trace heating
circuits.
▪
Install the trace heater circuit carefully.
▪
Use the trace heater in accordance with the intended purpose and
strictly comply with the operational data specified in section
Tech-
nical Data
.
▪
The bending radius of the trace heater must be at least 25 mm (for
HTSB 35 mm). Do not bend on the narrow axis.
▪
To avoid short circuits, do not connect the trace heater bus wires
together.
▪
Keep all components and the trace heaters dry before and during
installation.
▪
Each heating circuit must be marked with electrical warning labels.
▪
Keep these instructions for future reference. If applicable, leave
them with the end user.
▪
De-energize before installation or servicing.
▪
Use only original BARTEC accessories.
Certifications / Approvals
PSB
KEMA 08 ATEX 0111 X
IECEx KEM 09.0084X
HSB/MSB KEMA 08 ATEX 0110 X
IECEx KEM 09.0083X
HTSB
Sira 10 ATEX 3268
IECEx SIR 16.0035
(see BARTEC website for additional information)
Technical data
PSB
MSB
HSB
HTSB
Max. exposure temperature
power on
65 °C
110 °C
120 °C
250 °C
Max. withstand temperature
power off
85 °C
130 °C
200 °C
250 °C
Min. operation temperature
-40 °C
-40 °C
-60 °C
-65 °C
Min. installation temperature
-55 °C
-50 °C
-60 °C
-40 °C
Operating voltage
max. 254 Vac
max. 254 Vac
max. 254 Vac
max. 277 Vac
Heat output
1
10 to 33 W/m
10 to 40 W/m
10 to 60 W/m
15 to 75 W/m
Braid resistance
< 18.2 Ω/km
< 18.2 Ω/km
< 18.2 Ω/km
< 18.2 Ω/km
Protection classification
II 2G Ex e IIC T5,
T6 Gb
II 2D Ex tb IIIC T95 °C,
T 80 °C Db
II 2G Ex e IIC 150 °C (T3),
T4 Gb
II 2D Ex tb IIIC T150 °C,
T130 °C Db
II 2G Ex e IIC 200 °C (T2),
T3, T4 Gb
II 2D Ex tb IIIC T200 °C,
T195 °C, T130 °C Db
II 2G Ex e IIC T2, T3 Gb
II 2D Ex t IIIC T200 °C,
T300 °C IP 6x Db
Temperature classes
2
T5, T6
T3, T4
T2, T3, T4
T2, T3
Minimum bending radius
25 mm
25 mm
25 mm
35 mm
1
nominal heat output at 10 °C
2
according to IEC/IEEE 60079-30-1:2015, refer to page 7 for further information