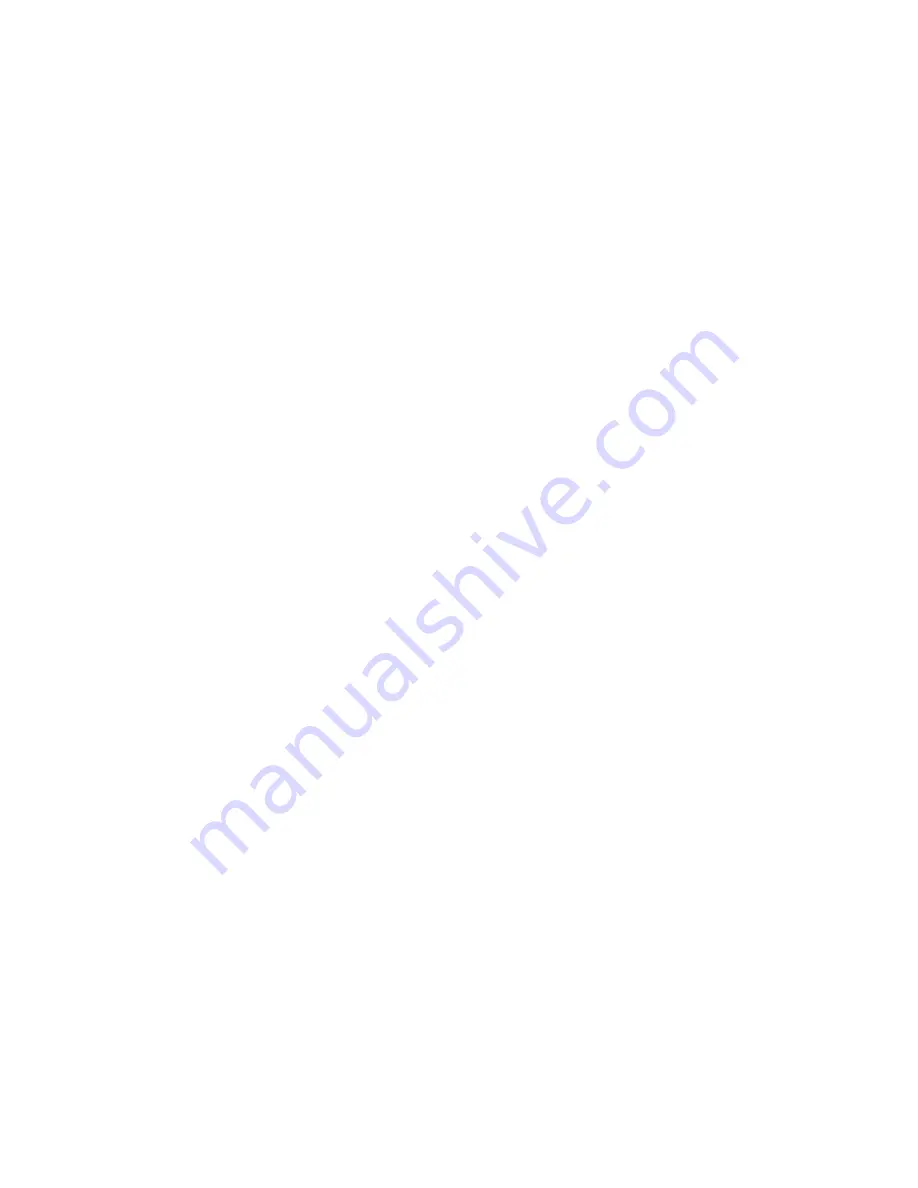
WAM Arm – User’s Manual
www.barrett.com
© 2008 Barrett Technology®, Inc.
Document: D1001, Version: AH.00
76 of 80
Appendix D GLOSSARY
Backdrivability - Backdrivability
is the measure of how accurately a force or motion that is
applied at the output end of a mechanical transition is reproduced at the input end. In a mechanical
robot-like linkage, good backdrivability means that a person can grab the ending of the linkage
and move it around effortlessly. Some robots show acceptable backdrivability for slow
disturbances, but near-zero backdrivability when the disturbances happen suddenly.
Backdrivable Robot -
A
robot
which exhibits greater than 95% backdrivability.
BarrettHand™ -
The 1.2 kilogram dexterous robotic Grasper™ as described in the
BarrettHand™ BH8-Series User’s Manual.
Cables (mechanical tension elements) -
A “wire rope” typically made from very fine strands of
stainless steel.
CANbus Communications -
CANbus
is a robust, deterministic, and addressable 2-wire serial-
communications protocol that operates up to 1 megabit/sec.
Cartesian Space -
Cartesian space
is a rectilinear, orthogonal description of three-dimensional
space. It consists of three infinitely long straight lines that intersect at a mutual point, the origin.
The lines are often associated with right-hand X, Y, and Z axes, and half of each line is designated
positive. For the WAM, the world coordinate frame is right-handed and its origin is in the center
of the shoulder with X pointing toward the front (rounded) part of the WAM, and Z pointing up
(see frame docs in this manual).
Controller -
The word
controller
in the field of motion controls has two meanings:
1.
A motor controller takes sensor feedback of rotor position and performs (brushless-
commutation) calculations to determine a set of winding currents for that position that
will produce either a desired trajectory or a desired torque (in cases with very low
Coulomb friction). Then, in most modern motor controllers, a set of PWM signals is
generated that control a set of (typically 6) FETs (through charge pumps) arranged in a
double-H bridge (in the 6-FET case).
2.
A high-level motion controller coordinates the motions of one or more axes of a robot. A
simple controller may apply a PID filter to a single joint to follow a trapezoidal function
(velocity vs. time) with limits on acceleration/deceleration and velocity. More
sophisticated controllers may control trajectories and forces in true Cartesian space and
may exploit modeled observers, nonlinear functions, and adaptive control techniques.
Degrees of Freedom
-
Degrees of freedom
is shorthand for
independent
degrees of freedom
,
which is almost always equal to the number of motors, as long as the motors drive independent
axes. Generally a six-degree-of-freedom robotic arm can place its tool frame origin at any location
within its reach and orient that frame arbitrarily anywhere within its dexterous workspace.
However, for a fixed position and orientation of the tool frame the arm pose is fixed.
When there are more degrees of freedom than 6-space, the robot arm kinematics are called
redundant. For example, a seven-degree-of-freedom robotic arm such as the WAM arm remains
free to move even while holding a position and orientation.
Denavit-Hartenberg (D-H) -
Denavit-Hartenberg
is a technique for analyzing the type of serial-
link kinematic chains used in robotic manipulators in which each frame is defined relative to its
adjacent frame via two length dimensions and two rotations. The scheme is flexible enough to
work with both revolute and prismatic joints. An important initial step in the analysis is to affix
coordinate frames to each sequential link according to a protocol that is consistent with correct
interpretation of the D-H parameters.