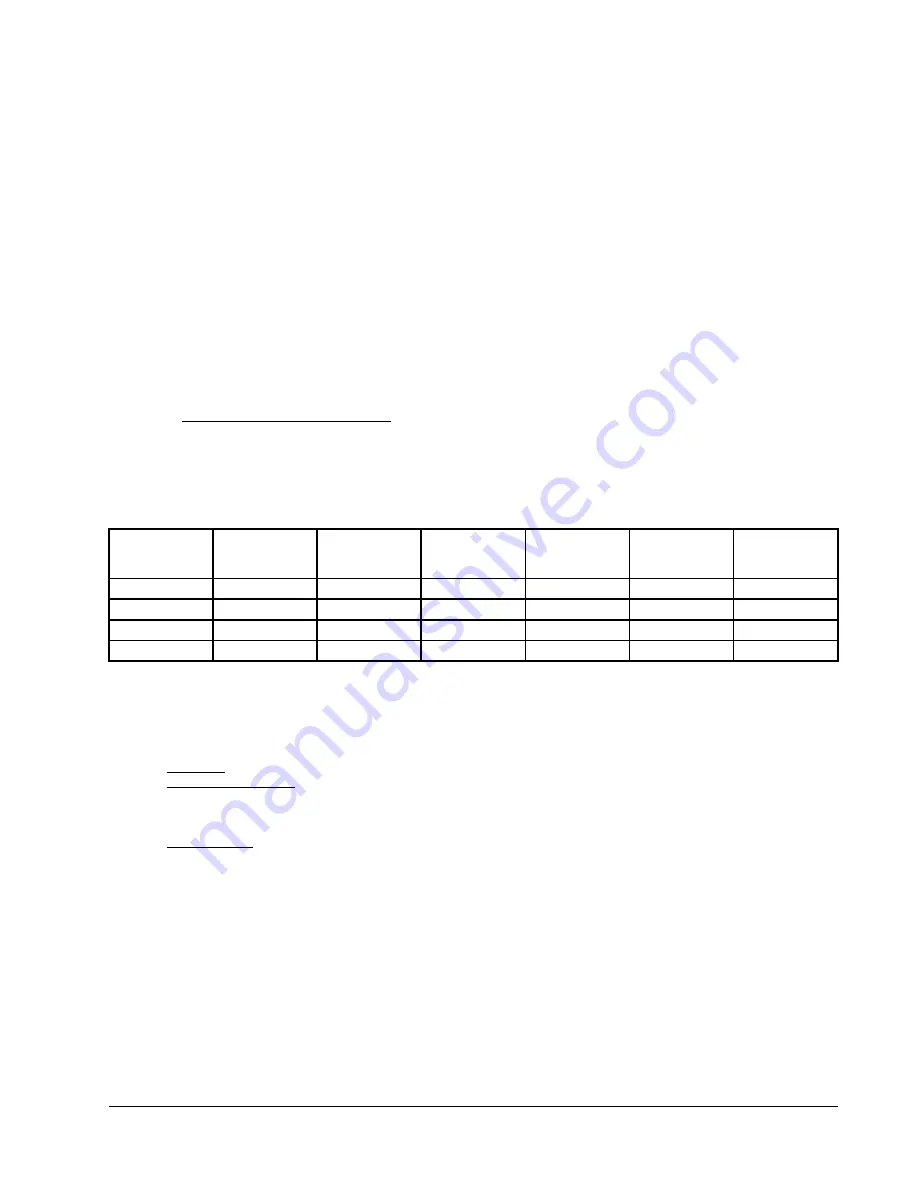
Manual 2100-577C
Page
29 of 50
Maximum ESP (inches WC) shown is with 2" MERV 8 pleated filter.
Rated CFM for ducted applications – required for maximum performance rating.
l
Optional 2nd Stage CFM – the unit is factory shipped to operate on full 2nd stage airflow. If the optional 2nd
stage airflow is desired, it requires removal of gray wire from "Y2" terminal of low voltage terminal strip in unit
main control panel. This reduces system capacity performance by approximately 2% at the same energy
efficiency.
m
Continuous CFM the total airflow being circulated during continuous blower operation.
NOTE: These units are equipped with a variable speed (ECM) indoor motor that automatically adjusts
itself to maintain approximately the same rate of indoor airflow in both heating and cooling, dry
and wet coil conditions, and at both 230/208 or 460 volts.
TABLE 4
Indoor Blower Performance
MODEL
RATED
ESP
MAX. ESP
CONTINUOUS
AIRFLOW
m
RATED
1st STAGE
OPTIONAL
2nd STAGE
l
RATED
2nd STAGE
QW2S2
0.0
0.5
800
800
900
1000
QW3S2
0.0
0.5
800
900
1050
1150
QW4S2
0.0
0.5
900
1200
1300
1450
QW5S2
0.0
0.5
900
1400
1500
1650
PRESSURE SERVICE PORTS
High and low pressure service ports are installed on
all units so that the system operating pressures can be
observed. Pressure charts are located on the backside
of the units lower service door, as well as later in
this Manual (Table 5). It is imperative to match the
correct pressure chart to the unit by model number. All
upper service doors must be attached to obtain proper
reading. The service ports are in the lower compressor
section on the tubing adjacent to the compressor.
This unit employs high-flow Coremax valves instead of
the typical Shrader type valves.
WARNING! Do NOT use a Schrader valve core removal
tool with these valves. Use of such a tool could result
in eye injuries or refrigerant burns!
To change a Coremax valve without first removing the
refrigerant, a special tool is required which can be
obtained at www.fastestinc.com/en/SCCA07H. See the
replacement parts manual for replacement core part
numbers.
PIPING ACCESS TO UNIT
Water piping to and from the coaxial water coil is
intended to enter/exit the unit through the rectangular
hole (See Figures 1, 8A, 21 and 22). The connections
on the water coil are a double O-ring with a retainer nut
that secures it in place.
Various double O-ring fittings are available so you may
then connect to the coaxial coil with various methods
and materials. The methods include 1" barbed fittings
(straight and 90°), 1" MPT (straight and 90°), and 1¼"
hot fusion fitting with P/T fitting). (See Table 6.)
Note:
All double O-ring fittings require “hand
tightening only”. Do not use a wrench or pliers as
retainer nut can be damaged with excessive force.
Avoid cross-threading the nut.
Note:
Apply petroleum jelly to o-rings to prevent
damage and aid in insertion.