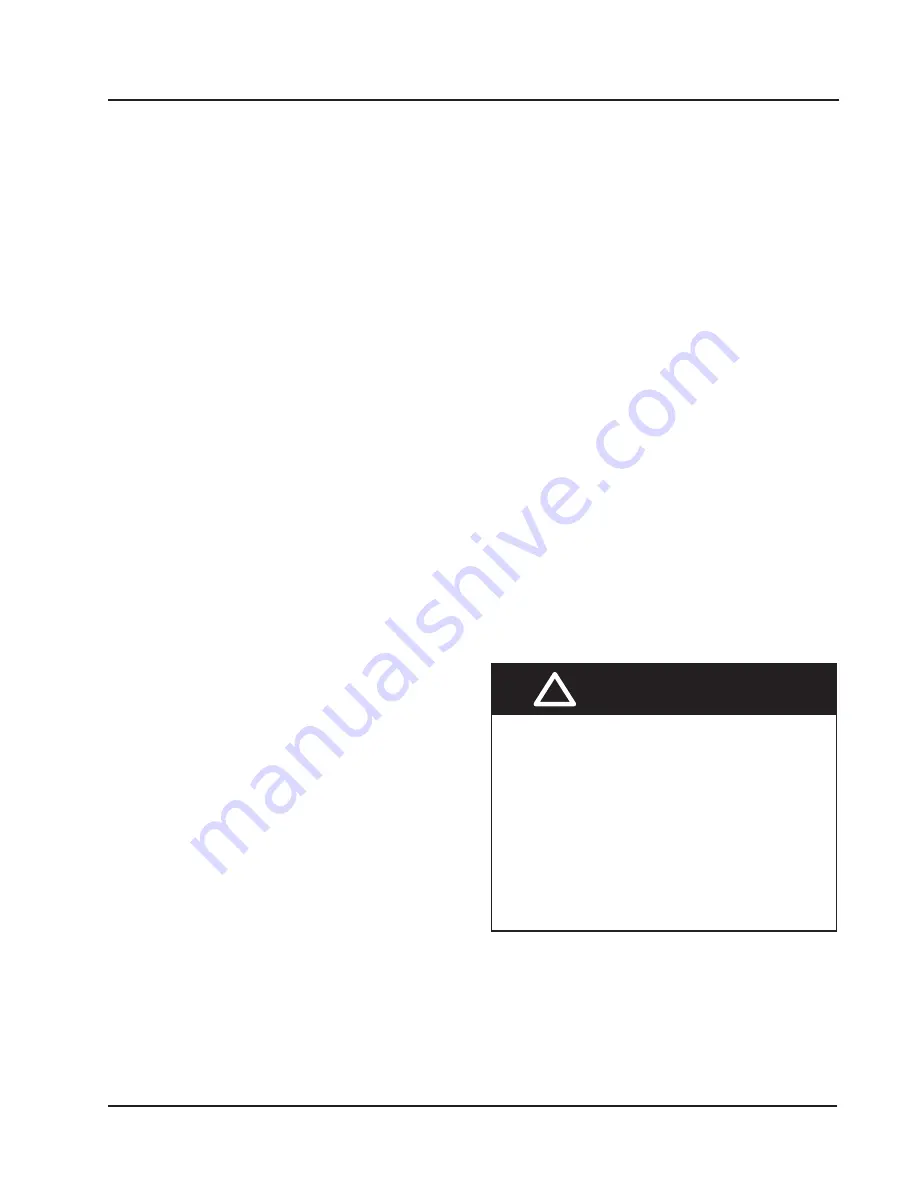
Manual 2100-752B
Page
41 of 49
!
WARNING
Exposure to high pressure refrigerant hazard.
This unit is equipped with an electronic
expansion valve (EEV). In order to fully
recover refrigerant or evacuate system during
repairs, either use service tool P/N 2151-
021 to manually open the EEV or be sure to
recover and evacuate from all service ports:
suction, liquid and discharge.
Failure to do so could result in eye injuries
and/or refrigerant burns.
DO NOT connect to the high pressure service port on
the front of the unit with the RED circular label. This
connection point is under very high pressure and could
cause injury and/or refrigerant burns.
DEHUMIDIFICATION UNIT INSTRUCTIONS
Q**A4D dehumidification models provide a unique
dehumidification circuit for periods of low outdoor
ambient temperature and high indoor humidity
conditions.
Refer to Spec Sheet S3620 for the standard features of
the base units and this manual for electrical data.
Dehumidification Circuit
The dehumidification circuit incorporates an
independent heat exchanger coil in the supply air
stream. This coil uses discharge gas to reheat the
supply air after it passes over the cooling coil without
requiring the electric resistance heater to be used for
reheat purposes. This results in very high mechanical
dehumidification capability from the air conditioner on
demand without using electric resistance reheat.
The dehumidification refrigerant reheat circuit is
controlled by a dehumidification valve directing
the refrigerant gas to the normal condenser during
periods when standard air conditioning is required.
During periods of time of low ambient temperature
(approximately 65° to 75° outdoor) and high indoor
humidity, a humidistat senses the need for mechanical
dehumidification. It then energizes both the compressor
circuit and dehumidification valve, thus directing
the hot refrigerant discharge gas into a separate
desuperheating condenser circuit, which reheats the
conditioned air before it is delivered to the room. The
refrigerant gas is then routed from the desuperheating
condenser to the system condenser for further heat
transfer. When the humidistat is satisfied, the system
automatically switches off. The result is separate
humidity control at minimum operating cost.
Dehumidification Sequence of
Operation
Dehumidification is controlled through the thermostat
(if capable) or through a separate humidistat. On a call
for dehumidification mode of operation, the compressor
and dehumidification valve of the unit are energized
through circuit R - D to provide dehumidification.
Dehumidification will continue until the humidistat is
satisfied.
Any time there is a call for circuit R - Y1, the
dehumidification mode will cancel and the system will
return to cooling operation.
Balanced Climate
TM
Mode
Enable Balanced Climate mode for cooling operation
ONLY and utilize a 2-stage thermostat to enhance the
comfort. To activate this mode, the jumpers between Y1
and Y2 on both low voltage terminal strips (blower section
and control panel) need to be removed. Refer to unit
wiring diagram for clarity.
This mode will allow the indoor blower to run at a
reduced airflow on the first stage of cooling. A 2-stage
thermostat connected to Y2 will then allow the airflow
to return to normal rated speed if the call for cooling is
not satisfied within the allotted time frame specified by
the thermostat.
Electronic Expansion Valve
Operation
This model employs an electronic expansion valve
(EEV) which meters the refrigerant to the evaporator.
The EEV is made of a stepper motor that is controlled
with a step output from the controller. The valve is
capable of 480 steps which drives a needle valve that
in turn regulates the flow of refrigerant. The EEV allows
for tighter control and better capacity management in
varying operating conditions than a standard TXV. The
EEV system consists of the electronic valve and stator,
control board, relay, suction temperature sensor and
suction pressure transducer. The pressure transducer
and temperature sensor monitor the suction line to
provide real time data to the control board so that a real
time superheat can be calculated. This then determines
the EEV position. The controller is set to maintain
around 17° superheat. The relay is used to activate the
EEV system’s controller anytime that the compressor is
energized.
EEV Instructions for Vacuuming, Reclaiming and
Charging Unit
Содержание Q36A4DA
Страница 16: ...Manual 2100 752B Page 16 of 49 MIS 2471 A REMOVE KNOCK OUT FOR INDOOR DRAIN HOSE CONNECTOR FIGURE 18C If used...
Страница 39: ...Manual 2100 752B Page 39 of 49 GRAPH 2 Q42A4D FAD Ventilation Delivery GRAPH 1 Q36A4D FAD Ventilation Delivery...
Страница 40: ...Manual 2100 752B Page 40 of 49 GRAPH 3 Q48A4D FAD Ventilation Delivery...