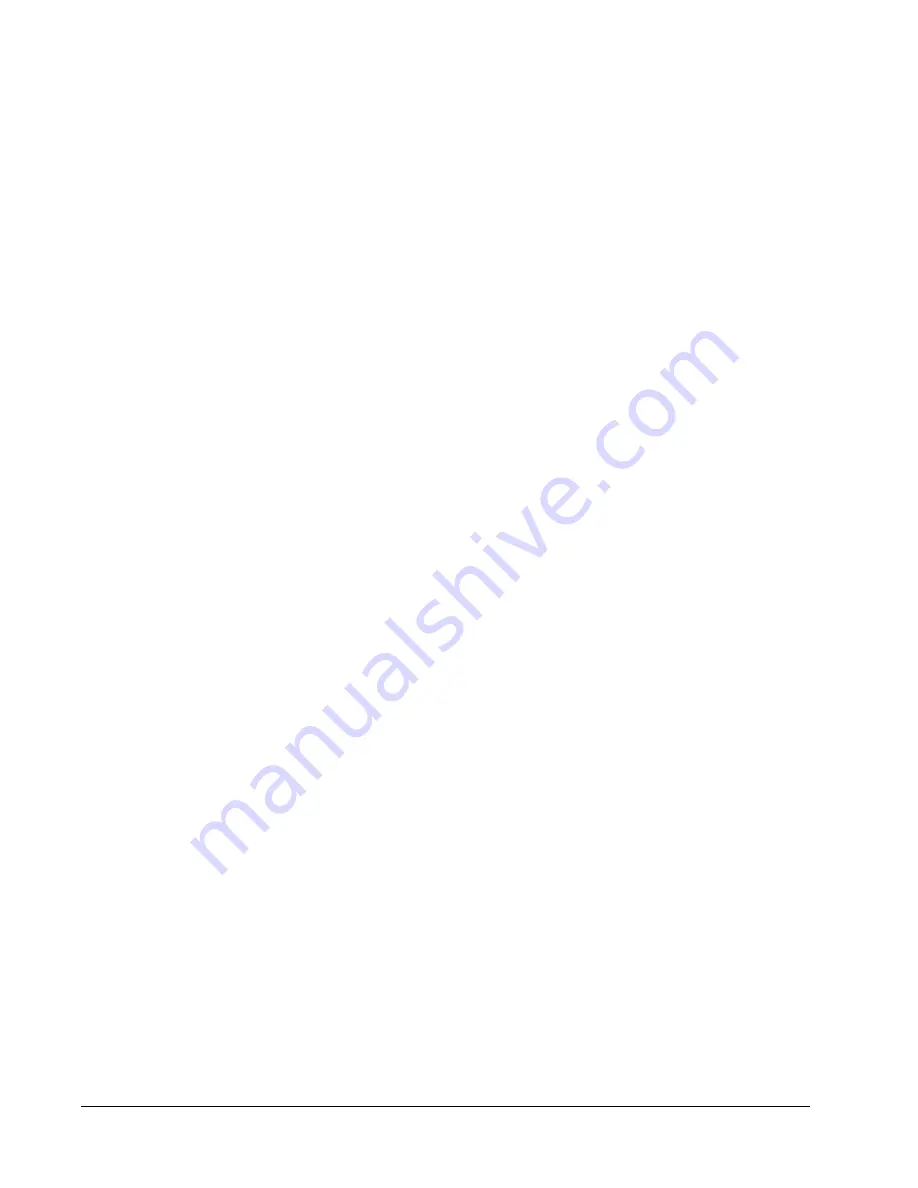
Manual 2100-600C
Page
30 of 38
SERVICE HINTS
1. Caution user to maintain clean air filters at all
times. Also, not to needlessly close off supply
air registers. This may reduce airflow through
the system, which shortens equipment service
life as well as increasing operating costs and
noise levels.
2. Check all power fuses or circuit breakers to be
sure they are the correct rating.
3. Periodic cleaning of the outdoor coil to permit
full and unrestricted airflow circulation is
essential.
4. Some service requires the need to remove the
unit from the wall including replacement of
the indoor coil and/or the outdoor coil. Also
servicing the outdoor fan motor or fan blade
will require removing the unit from the wall if
the unit is installed at a height that is not easily
accessible from the outside of the building.
In order to remove the unit from the wall the
following procedure must be used:
a. Turn off power to the unit at the remote
location. Some units may have more than one
power supply.
b. Disconnect field wiring at unit terminal block
and remove from unit.
c. Disconnect condensate drain.
d. Remove the lower skirting around the unit.
e. Remove wall mounting brackets from wall on
each side of the unit.
f. If unit is attached to duct work, remove upper
cabinet extension by removing the top center
screw only from the cabinet side panel.
g. Remove screws that attach the duct work to
the unit flanges.
This unit is equipped with four rollers mounted
to the base. For ease of pulling unit out from
the wall, you may want to remove the bottom
service door which requires removal of the
return air panel, and grip the front flange of the
base pan then pull straight out.
5. Annual maintenance is required to make sure
that all of the systems are functioning properly.
a. Check to make sure that the drains are not
obstructed in any way.
b. Remove any debris in the condenser section
of the unit.
c. Inspect and clean mist eliminator as described
below.
d. Inspect and wash outdoor coil as necessary.
The conditions needed for the unit to enter test mode
are as follows: POT must start at a time less than or
equal to the 40 second mark. The POT must then be
rapidly rotated to a position greater than or equal to
the 280 second mark in less than ¼ second. Normal
operation will resume after power is reset or after the
unit has been in test mode for at least 5 minutes.
Brownout Protection with Adjustment
Brownout protection may be necessary if the utility
power or generator power has inadequate power to
prevent the voltage from dropping when the compressor
starts. This is rare but can happen if the generator
is undersized at the site or if the site is in a remote
location far from the main power grid. Under normal
circumstances, allowing the brownout to be ignored for
a time period should not be needed. The 8201-164 is
shipped in “0” do not ignore position, with all the DIP
switches off (see Figure 21).
If ignoring the brownout is needed because of the
above conditions, three preset timers can be set by DIP
switches in order to delay signaling a power brownout
for a specific length of time after compressor contactor
is energized. This allows the compressor a time period
to start even if the voltage has dropped and allows
the voltage to recover. This delay only happens when
the CC terminal energizes. The delay can be set to 500
milliseconds (A DIP switch), 1000 milliseconds (B DIP
switch) or 1500 milliseconds (C DIP switch); time is not
cumulative—only the longest setting will apply. If the
voltage recovers during the brownout time period, the
compressor will start. If the voltage doesn’t recover
during the time period, the blue LED will flash. A
flashing blue LED indicates that a brownout condition
was sensed; the control will continue to flash the blue
LED until the Y call has been satisfied. The compressor
will not start if the blue LED is flashing.
If user chooses the “0” do not ignore position when the
site has inadequate utility or generator power, this could
lead to the compressor never starting. The control will
see the brownout immediately and not start.
A common scenario and one that has been seen in the
field is when a unit or units switches from utility power
to generator power. With slower transfer switches, the
time delay between the utility power and generator
power didn’t cause a problem. The units lost power,
shut off and came back on line normally. With the
introduction of almost instantaneous transfer switches,
the millisecond long power glitch can be enough that
the compressor will start to run backwards. In this
scenario, the CCM will catch this and restart the units
normally.
Содержание Q24A2-A
Страница 7: ...Manual 2100 600C Page 7 of 38 FIGURE 1 UNIT DIMENSIONS...
Страница 10: ...Manual 2100 600C Page 10 of 38 FIGURE 6 DUCTED APPLICATION FIGURE 5 INSTALLATION WITH FREE BLOW PLENUM...
Страница 14: ...Manual 2100 600C Page 14 of 38 MIS 2469 DRAIN BOX WALL SLEEVE OVERFLOW TUBE CAULK AROUND TUBE FIGURE 12A...
Страница 16: ...Manual 2100 600C Page 16 of 38 MIS 2471 A REMOVE KNOCK OUT FOR INDOOR DRAIN HOSE CONNECTOR FIGURE 12C If Used...
Страница 32: ...Manual 2100 600C Page 32 of 38 FIGURE 22 FRESH AIR DAMPER REMOVAL MOUNTING SCREW...