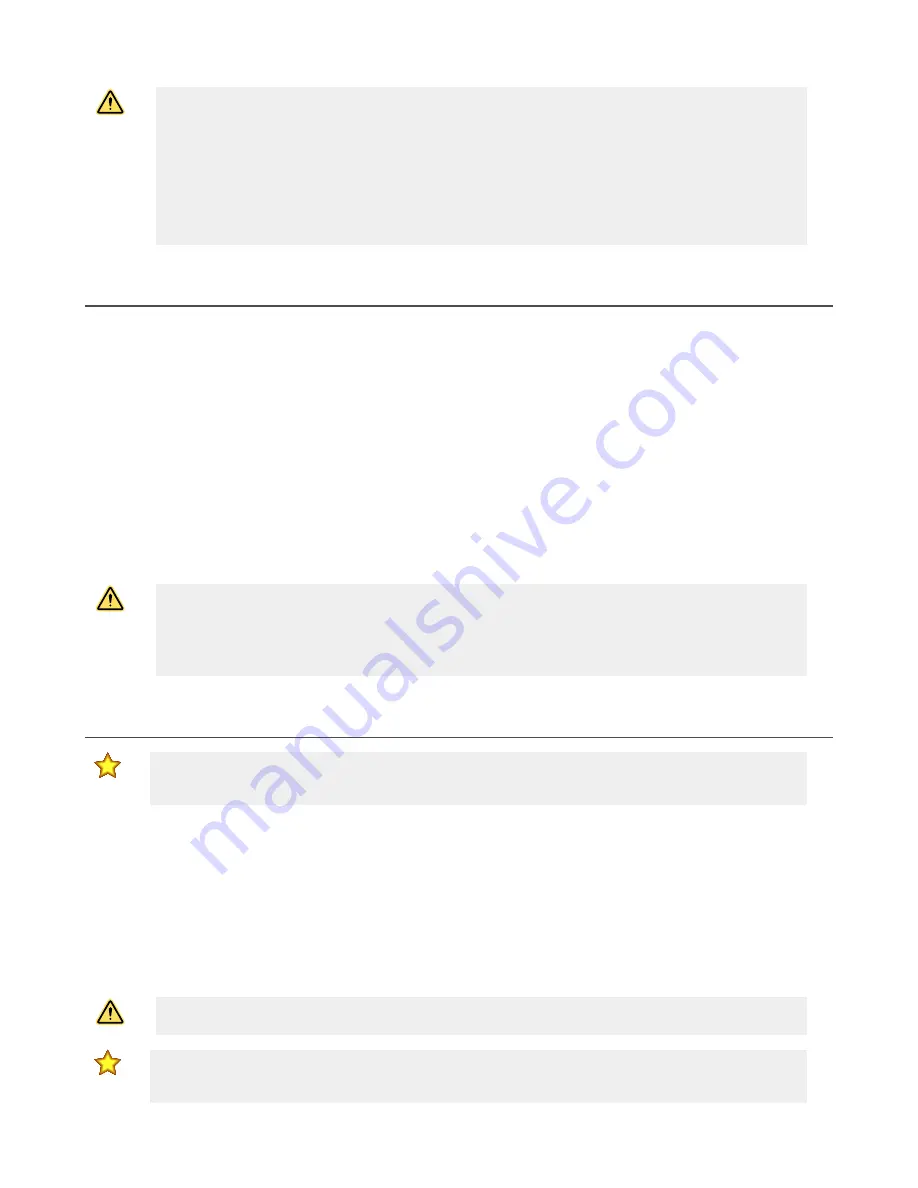
WARNING:
• The hazard must be accessible only through the sensing field
• Incorrect system installation could result in serious injury or death.
• The installation of the SI-RF Safety Switch must prevent any individual from reaching around,
under, over or through the defined area and into the hazard without being detected.
• See OSHA CFR 1910.217, ANSI B11.19, and/or ISO 14119, ISO 14120 and ISO 13857 for
information on determining safety distances and safe opening sizes for your guarding device.
Mechanical barriers (for example, hard (fixed) guarding) or supplemental safeguarding might be
required to comply with these requirements.
3.2 Pass-through hazards and Perimeter Guarding
A pass-through hazard is associated with applications where personnel may pass through a safeguard (which issues a stop
command to remove the hazard), and then continues into the guarded area, such as in perimeter guarding. Subsequently,
their presence is no longer detected, and the related danger becomes the unexpected start or restart of the machine while
personnel are within the guarded area.
Eliminate or reduce pass-through hazards whenever possible—see ANSI B11.19 and ANSI B11.20 or ISO 11161. One
method to mitigate the risk is to ensure that once tripped, either the safeguarding device, the safety related part of the
control system, or the guarded machine's MSCs/MPCEs will latch in an OFF condition. The latch must require a deliberate
manual action to reset that is separate from the normal means of machine cycle initiation.
This method relies upon the location of the reset switch as well as safe work practices and procedures to prevent an
unexpected start or restart of the guarded machine. All reset switches must be:
• Outside the guarded area
• Located to allow the switch operator a full, unobstructed view of the entire guarded area while the reset is
performed
• Out of reach from within the guarded area
• Protected against unauthorized or inadvertent operation (such as through the use of rings or guards)
If any areas within the guarded area are not visible from the reset switch, additional safeguarding must be provided.
WARNING: Pass-Through Hazards and Perimeter Guarding
Lockout/Tagout procedures per ANSI Z244.1 may be required, or additional safeguarding, as described
by ANSI B11.19 safety requirements or other appropriate standards, must be used if a passthrough
hazard cannot be eliminated or reduced to an acceptable level of risk. Failure to follow these instructions
could result in serious injury or death.
3.3 Mechanical Installation
Important: Install a safety switch in a manner which discourages tampering or defeat. Mount switches to
prevent bypassing of the switching function at the terminal chamber or Quick Disconnect (QD). A switch
and its actuator must never be used as a mechanical stop. Overtravel may cause damage to switch.
All mounting hardware is supplied by the user. Fasteners must be of sufficient strength to guard against breakage. Use of
permanent fasteners or locking hardware is recommended to prevent the loosening or displacement of the actuator and the
switch body. The mounting holes (4.5 mm) in the switch and actuator body accept M4 (#6) hardware.
Mount the sensor and actuator such that the position cannot be changed after installation/adjustment. Mount the switch
securely on a solid, stationary surface. Prevent the loosening of mounting hardware by using lock washers, thread-locking
compound, etc. Only use slots for initial positioning. Pins, dowels, and splines can be used to prevent movement of the
switch and the actuator.
Install the SI-RF Safety Switch to prevent false or unintended actuation and intentional defeat.
Locate the sensor and actuator to allow access for functional checks, maintenance, and service or replacement. The
installation should provide suitable clearances, be readily accessible, and allow access to the actuator and sensor.
CAUTION: Do not overtighten the units during installation. Overtightening can twist the housing and
affect the sensors performance.
Important: It is the responsibility of the machine builder (user) to make sure the series wiring/cabling is not
easily manipulated by an operator to defeat the safety function(s); for example, cannot remove a switch
from the chain.
SI-RF Non-Contact RF Safety Switch
www.bannerengineering.com - Tel: + 1 888 373 6767
7