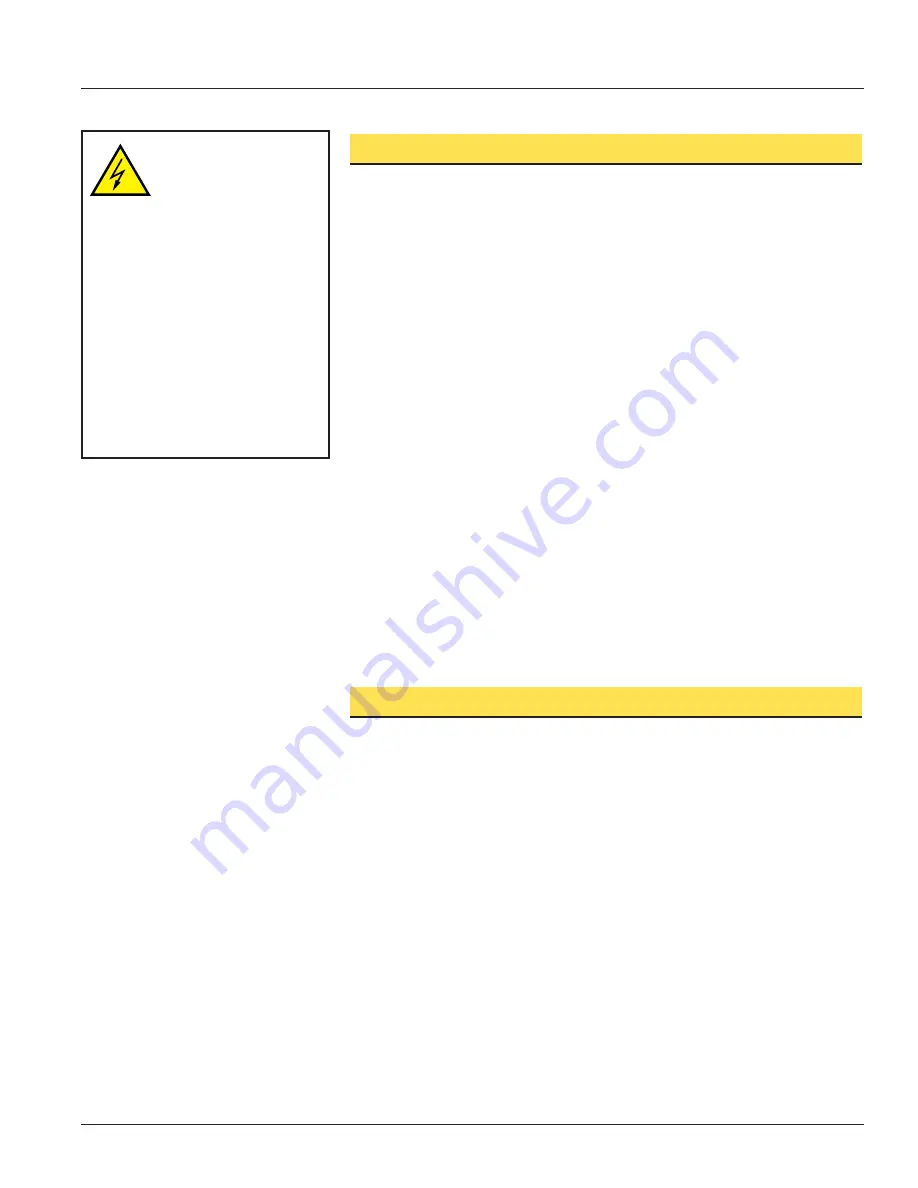
E-Stop Safety Module
– Models ES-GA-5A and ES-HA-5A
Initial Checkout Procedure
Checkout procedure:
1) Remove power from the machine control elements.
2) Activate the E-stop switch (open its contacts).
3) Apply power to the E-Stop Safety Module at terminals A1 and A2 or B1 and B2
(see Figure 2). Verify that only the
Input Power
indicator (Figure 1) is ON. If either
of the other two indicators is ON at this point, disconnect the input power and
check all wiring. Return to step 2 after the cause of the problem has been
corrected.
4) Arm the E-stop switch (close its contacts).
5)
Automatic reset:
K1 and K2 indicators should come ON, and the safety output
contacts should close.
Manual reset:
Close the Reset switch. The K1 and K2 indicators should remain
off. Open the Reset switch. The K1 and K2 indicators should both come ON at
this time. If either indicator comes ON before the Reset switch is opened,
disconnect the input power and check all wiring. Return to step 2 after correcting
the problem.
6) Activate the E-stop switch (open its contacts). The K1 and K2 indicators should turn
OFF simultaneously. If either indicator remains ON, disconnect the input power and
check all wiring. Return to step 2 after the cause of the problem has been corrected.
7) Close the enclosure. Apply power to the Machine Control Elements and perform
the Periodic Checkout Procedure.
NOTE: If more than one E-stop switch is series-connected to one E-Stop Safety
Module, the above checkout procedure must be run individually for
EACH switch.
Periodic Checkout Procedure
The functioning of the E-stop system must be verified on a regular periodic basis to
ensure proper operation (see also the machine manufacturer’s recommendations).
Procedure:
1) With the machine running, engage the E-stop switch (open its contacts). Verify that
the machine stops.
2) Return the E-stop switch to its closed-contact position. Verify that the machine
does not restart.
3) Close and then open the Reset switch (if using manual reset mode). Verify that the
machine restarts.
NOTE: If two or more E-stop switches are series-connected to one E-Stop Safety
Module, this test must be run individually for EACH switch.
CAUTION . . .
Disconnect Power Prior
to Checkout
Before performing the
initial checkout procedure, make
certain all power is disconnected
from the machine to be controlled.
Dangerous voltages may be present
along the E-Stop Safety Module
wiring barriers whenever power to the
machine control elements is ON.
Exercise extreme caution whenever
machine control power is or may be
present. Always disconnect power to
the machine control elements before
opening the enclosure housing of
the E-Stop Safety Module.
Buy: www.ValinOnline.com | Phone 844-385-3099 | Email: [email protected]