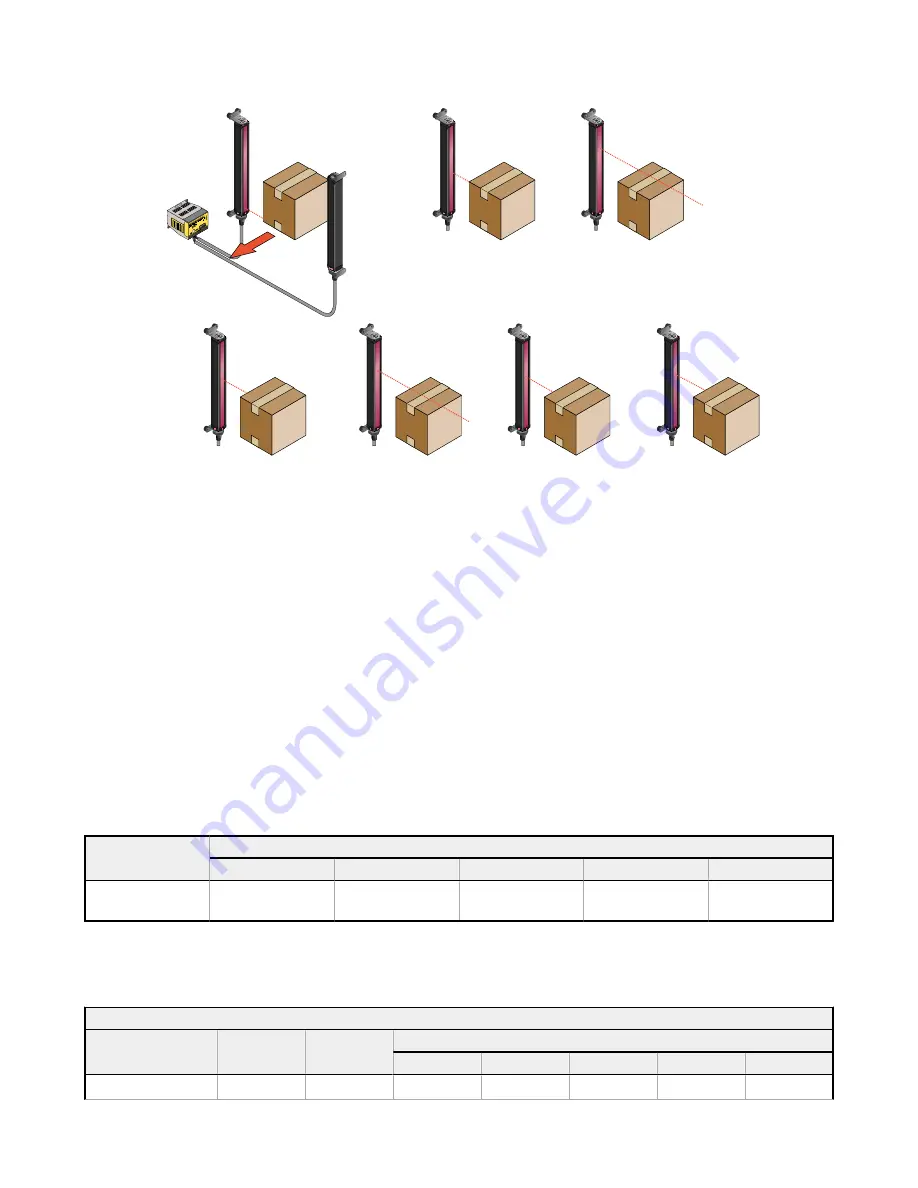
DIAGNOSTICS
Error No.
Error T
ype
Error No.
Error T
ype
—
System
OK
4
Emitter Error
1
Align
/ blank
5
Serial
Comm
2
Output
Short
6
EEPROM
3
E / R Mismatch
7
CPU Error
4
Receiver
Error
8
Null / Span
1
POWER
2 - TX
3 - RX
5 - COM
ALIGNMENT
SWITCH
DIAGNOSTICS
INDICA
TOR
RS-232
MAHCN-1
HIGH RESOLUTION MINI-AR
RAY CONTROLLER
2
3
4
5
6
7
8
9
10
11
12
13
14
15
16
17
18
19
20
1
+
NC
NC
10-30Vdc
GATE
NC
TX
TX
+12V
BR
EMTR
RCVR
BU
BK
5 Wires
WH
30V
150mA MAX
OUTPUT#1
COM
DRN
T/R
T/R
16-30V dc
1A MAX
POWER 2
3
4
5
6
7
8
9
10
11
12
13
14
15
16
17
18
19
20
OUTPUT
ALARM
GA
TE
ALIGN
–
+
–
F1
30V(MAX)
150mA MAX
ALARM
10-30Vdc
ALIGN
RS-485
+
–
High-Resolution
Emitter
MAHCN-1
Control Module
High-Resolution
Receiver
Beam #1 of 64
Blocked
Beam #48
Clear
Beam #32
Blocked
Beam #44
Clear
Beam #40
Blocked
Beam #42
Blocked
Beam #43
Blocked
Step #2
Step #1
Step #3
Step #4
Step #5
Step #6
Step #7
Figure 20. Finding an Edge Using a Binary Search
Note that the receiver always checks the bottom beam first, and only if that beam is blocked does the binary search
continue. Therefore, Single-Edge scan will not work in instances where an item that does not block the first beam is to be
measured. Single-Edge scan is also ineffective if the object does not present a continuous blocked pattern. In other words,
Single-Edge scan is used for single, solid objects that block the first beam.
Double-Edge scan is used to detect two edges of a single object, for example, box width measurements. Double-Edge
Scan requires the selection of a step size: 2, 4, 8, 16 or 32 beams. The sensor uses the steps to skip over beams. Double-
Edge scan works as follows:
1. The sensor activates beam #1 (the beam closest to the sensor cable end).
2. The sensor activates the next beam, determined by the step size. For example, if the step size is 2, beam #3 is next;
if the step size is 8, beam #9 is next.
3. As long as the activated beam is unblocked (or made), the sensor continues the stepping routine until a blocked
beam is found.
4. When a blocked beam is found, a binary search is conducted to find the object’s bottom edge.
5. When the bottom edge is found, the sensor begins stepping again through the array until the sensor finds the next
unblocked beam.
6. A binary search is again performed to find the second edge.
Note that this scanning method sacrifices object detection size for speed. Similar to Single-Edge scan, Double-Edge scan
has some restrictions: the object should provide a solid obstruction; the size of the object will determine the maximum step
size.
Table 1: The Effect of Step Size on Minimum Object Detection Size
Step Size
Number of Beams
2
4
8
16
32
Minimum Object
Detection Size
5 mm (0.2 in)
10 mm (0.4 in)
20 mm (0.8 in)
40 mm (1.6 in)
80 mm (3.2 in)
Sensor response time is a function of sensor length and scanning method. Typical scan times are shown in the following
table.
Table 2: The Effect of Sensor Length and Scanning Method on Scan Time (Typical)
Maximum Scan Time (in milliseconds)
Array Length
Straight Scan
Single-Edge
Scan
Double-Edge Scan
Step 2 Beams
Step 4 Beams
Step 8 Beams
Step 16 Beams
Step 32 Beams
163 mm (6.4 in)
5.8
1.8
4.8
3.4
2.7
2.5
2.6
A-GAGE
®
High-Resolution MINI-ARRAY
®
20
www.bannerengineering.com - Tel: + 1 888 373 6767