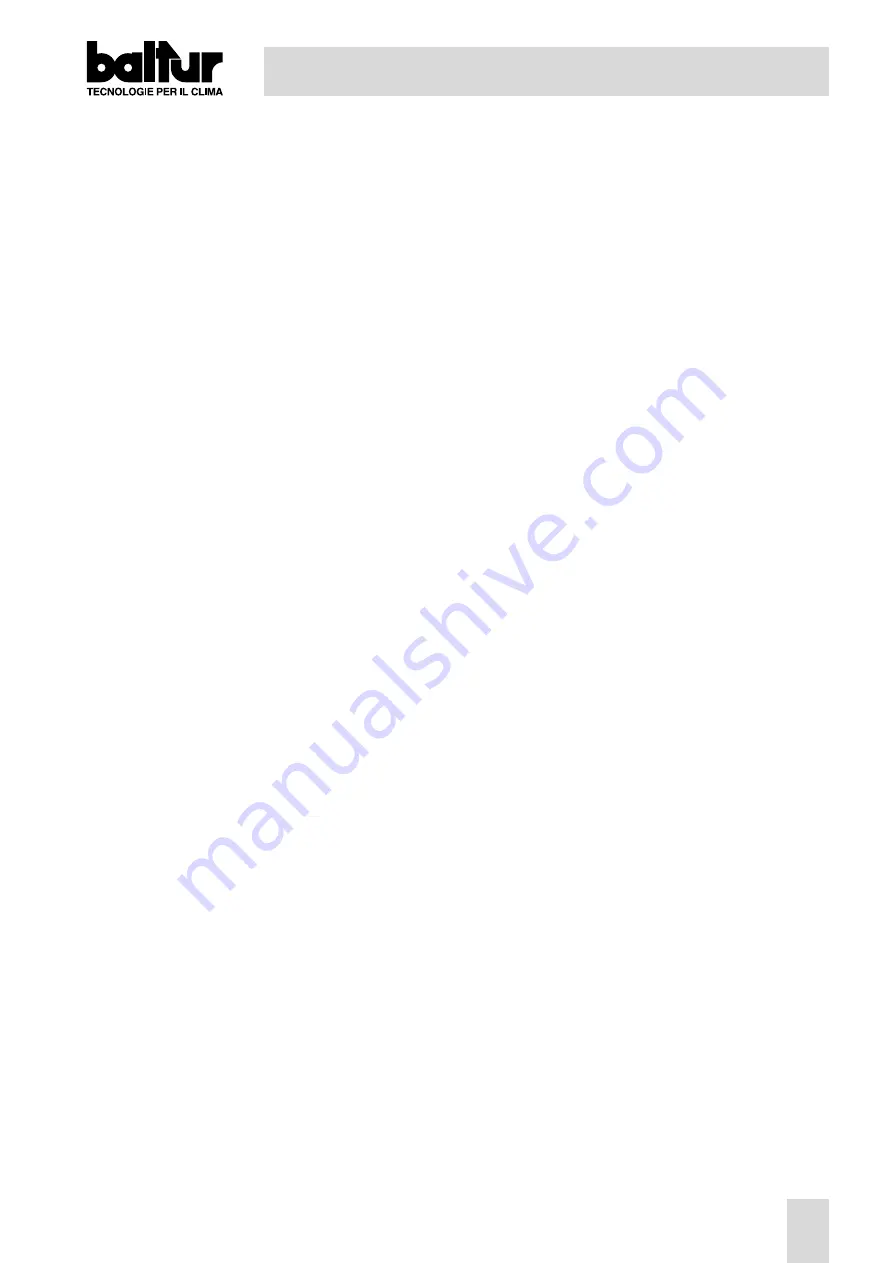
29
TWO STAGE PROGRESSIVE NATURAL GAS BURNERS
7) Regulate the air for the ignition flame, for minimum flame and high flame, following the instructions for regu-
lating air damper control electrical motor shown in the following pages. In practice, set the low flame and high
flame air regulation cams to the suitable positions according to the desired thermal power for low and high
flame.
8) By acting on the special screw for adjusting the gas and air pressure ratio, on the gas valve mod. MB-VEF....,
set the desired value (see the specific instructions for the gas valve MB-VEF.... in the following pages). In
practice, you must act on the adjusting screw of the ratio between the gas pressure (at the combustion head)
and the air pressure (at the combustion head) to set the reference index between the values of 0.4 and 0.8 so
as to have a greater air supply than gas.
10) Now enable the control panel switch and set the modulation switches to
MIN
(minimum) and
MAN
(manual).
The control box thus receives voltage, and the programmer determines the enable of the burner as described
in chapter “description of the operation”.
Note
: Pre-ventilation is carried out with open air and thus, during the same, the regulation servomotor is
enabled, and it runs a complete opening stroke up to the “maximum” set. Only when the regulation
servomotor returns to the “ignition” position, the control box continues its ignition program by enabling
the transformer and the ignition gas valves.
During the pre-ventilation step, make sure that the air pressure control switch changes position (from off
position without pressure detection it must switch to the off position with air pressure detection). If the air
pressure switch does not detect the sufficient pressure (it does not switch position), the ignition transformer
and the flame gas valves are not enabled, and thus the control box “locks”. Note that some “locks” at the first
stage are normal since in the valve ramp pipes there is still air that must be discharged before having a stable
flame.
To “unlock”, press the “unlock” push button. At the first stage there may occur further “locks” due to:
a) The gas pipes have not been sufficiently air-bled, and thus the gas quantity is not sufficient to allow a stable
flame.
b) The “lock” with presence of flame may be caused by instability of the same in the ionisation zone for an
incorrect air/gas ratio. Remedy is by varying the quantity of supplied air and/or gas so as to find the correct
ratio. The same problem may be caused by a wrong air/gas distribution in the combustion head. Remedy is
by operating on the combustion head regulation device, by adjusting the closing or opening of the air
passage between head and gas diffuser.
11) Set the burner to minimum flame (modulation servomotor set to minimum), check the quantity and appearance
of the flame making the necessary adjustments: see instructions elating to the gas valve model MB-VEF...
Afterwards, check the supplied gas quantity by reading the meter. If necessary, adjust the gas output and the
relevant combustion air by operating as described above. Then, check the combustion with the special instru-
ments (see chapter “Combustion control”).
12) After adjusting the “minimum”, set the modulation switches to
MAN
(manual) and
MAX
(maximum) position.
The air regulation servomotor sets to “maximum” and as a consequence, also the gas supply reaches the
“maximum”. The quantity of supplied gas is then checked by reading the meter.
With burner ignited at the maximum existing output, measure the gas flow rate by calculating the difference
between two reads performed after one minute from one another. By multiplying the measured value by sixty,
a sixty-minute flow rate – that is, one hour – is obtained. By multiplying the hourly output (m
3
/h) by the gas heat
value, you obtain the delivered power in kcal/h, which must correspond or be very close to that required by the
burner (lower heat value for methane = 8550 kcal/h).
Avoid operating the burner if the flow rate is more
than the admissible for the boiler so as to prevent possible damages to the same. Shut down the
burner after the two meter reads.
13) To change the maximum gas output, operate on the air flow rate regulator since the gas flow rate automatically
adjust to the air supply. Then, operate on the cam regulating the air damper maximum aperture position (see
dr. n° 0002934320). Reduce the aperture angle of the air damper to reduce the gas flow rate, and vice versa.
To change the gas/air ratio, see instruction of gas valve MB-VEF...
14) Afterwards, check the combustion with the special instruments and if necessary, check the existing regulation
(air and optionally gas).
Check with the special instruments that the carbon oxide (CO) percentage in
the flue gas does not exceed the maximum admissible value of 0.1% and that CO2 does not exceed
10% for methane. (See chapter “Combustion control”)
Содержание BTG 20 LX
Страница 35: ...35 TWO STAGE PROGRESSIVE NATURAL GAS BURNERS LMG 2 CONTROL BOX SPECIFICATIONS...
Страница 36: ...36 TWO STAGE PROGRESSIVE NATURAL GAS BURNERS LMG 2 CONTROL BOX SPECIFICATIONS...
Страница 37: ...37 TWO STAGE PROGRESSIVE NATURAL GAS BURNERS LMG 2 CONTROL BOX SPECIFICATIONS...
Страница 49: ...QUEMADORES DE GAS NATURAL DE DOS ETAPAS PROGRESIVO 49...
Страница 50: ...QUEMADORES DE GAS NATURAL DE DOS ETAPAS PROGRESIVO 50...
Страница 51: ...QUEMADORES DE GAS NATURAL DE DOS ETAPAS PROGRESIVO 51...
Страница 52: ...QUEMADORES DE GAS NATURAL DE DOS ETAPAS PROGRESIVO 52...
Страница 65: ...65 BR LEUR GAZ NATUREL DEUX ALLURES PROGRESSIVES...
Страница 66: ...66 BR LEUR GAZ NATUREL DEUX ALLURES PROGRESSIVES...
Страница 67: ...67 BR LEUR GAZ NATUREL DEUX ALLURES PROGRESSIVES...
Страница 80: ...ZWEISTUFIG GLEITEND BEI ERDGAS BRENNER 80...
Страница 81: ...ZWEISTUFIG GLEITEND BEI ERDGAS BRENNER 81...
Страница 82: ...ZWEISTUFIG GLEITEND BEI ERDGAS BRENNER 82...
Страница 95: ......