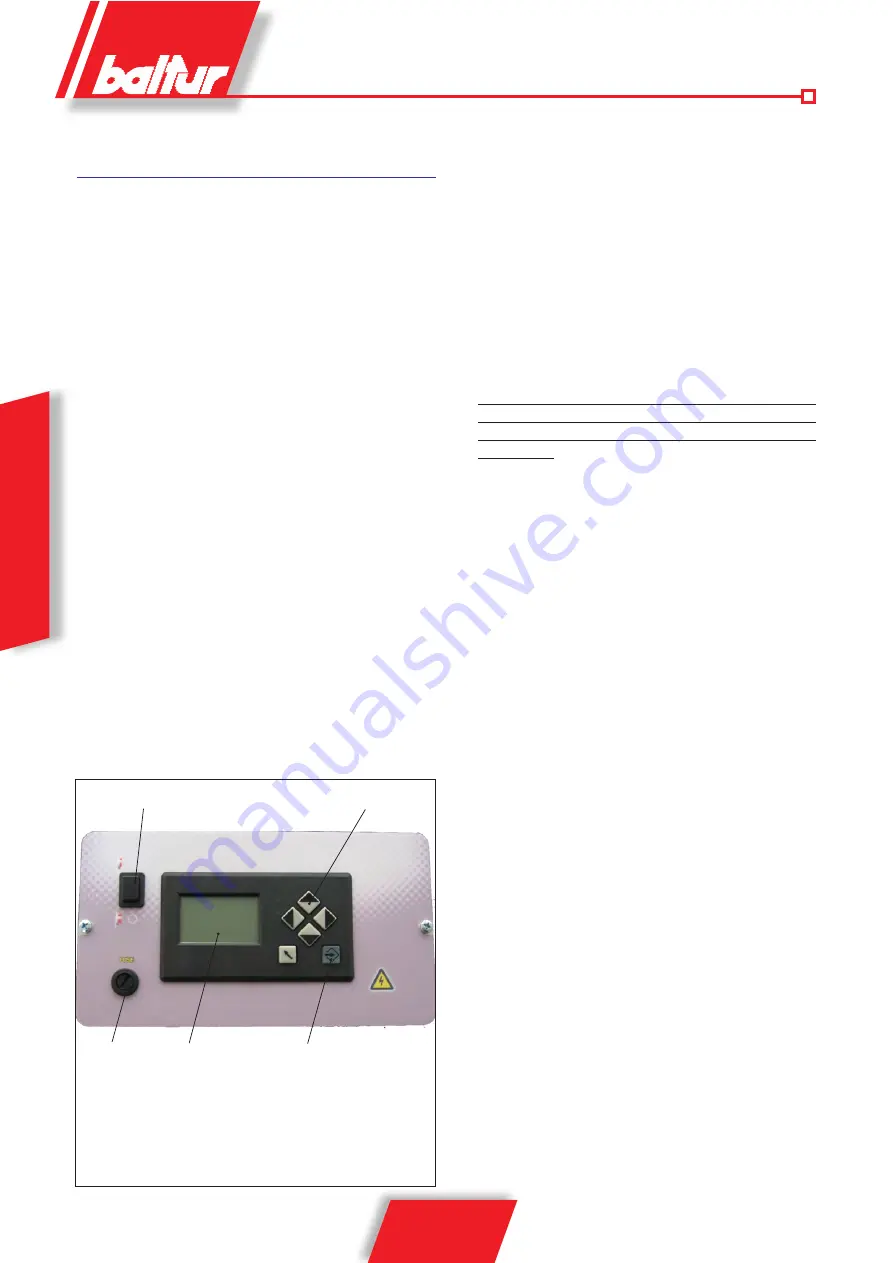
display
lamtec
BT3xx
3
4
1
2
5
14 / 26
0006081538_201308
ENGLISH
NATURAL GAS IGNITION
AND ADJUSTMENT
• The air contained in the piping must be bled out, with due
precautions and with doors and windows open. Open the fitting
on the piping situated near the burner and then open a little the
gas shut-off valve (or valves). When the characteristic odour of
gas can be smelled, close the shut-off valve. Wait long enough
for the gas in the room to disperse, and then connect the burner
to the gas pipe again and open the valve again.
• Check that there is water in the boiler and that the system gates
are open.
• Make absolutely sure that the products of combustion can be
released freely (boiler shutter valve and flue open).
• Make sure that the voltage of the power line to which the burner
is to be connected corresponds to that required by the burner and
that the electrical connections (motor or main line) are designed
for the voltage rating available. Also check that all the electrical
connections carried out on site are in accordance with our wiring
diagram.
• Make sure that the combustion head is long enough to enter
the furnace to the extent specified by the boiler manufacturer.
Check that the air adjustment device on the combustion head
is in the correct position for the fuel supply required (the air
passage between the disk and the head must be reduced for low
supply and relatively wide when supply is higher). See chapter
“Combustion head airflow adjustment”.
• Fit a pressure gauge with suitable full scale (where the pressure
level envisaged allows it, a liquid column manometer is
preferable; do not use pointer gauges for low pressures) to the
pressure outlet port on the gas pressure switch.
• With the switch (1) on the mimic panel switched to “O” and the
master switch turned on, manually close the remote control
switch and check that the motor revolves in the correct direction.
If necessary, exchange the position of the two cables in the line
that feeds the motor in order to reverse the direction of revolution.
• Now switch on the main switch. With the control equipment
receiving electrical power, the programmer will cause the burner
to start up as described in chapter “Operation description”. For
burner adjustment, refer to the supplied instructions for the "BT
3xx" electronic cam.
• After having adjusted the "minimum", (200) bring the burner
towards the maximum, using the controls on the “BT 3xx”
keyboard.
• We recommend that you check combustion using the appropriate
instrument at all intermediate points on the modulation route (from
200 to 999), checking the gas flow rate by reading the meter.
It is essential to check, with a suitable instrument, that the
percentage of carbon monoxide (CO) present in the fumes
does not exceed the limit set by regulations in force at the time
of installation.
• Now check the proper automatic operation of modulation.
This ensures that the equipment receives the signal from the
electronic modulation regulator, if the burner is the modulating
model, or from the second stage thermostat or pressure switch,
if it is a two stage progressive burner.
• The air pressure switch has the purpose of switching the
equipment into the safety (lock-out) status if the air pressure is
not what it should be. The pressure switch must therefore be set
to close the contact (closed during operation) when air pressure
in the burner is sufficient. The pressure switch connection circuit
is self controlling. Therefore, the contact which is meant to be
closed in a non operating status (fan stopped and thus no air
pressure in burner), should in fact be in this status, otherwise
the command/control equipment will not be switched on (burner
remains inoperative). Please note that if the contact meant
to be closed during operation does not close (insufficient air
pressure), the equipment carries out its cycle but the ignition
transformer is not switched on and the fuel valves do not open.
As a result, the burner stops. To verify that the air pressure switch
is operating correctly, while the burner is ignited at its minimum
setting, increase the adjustment value until the switch triggers
instant “lock” stop of the burner. Release the burner by pushing
the appropriate button and readjust the pressure switch to an
adequate value to detect the existent air pressure during the
pre-ventilation phase.
• The pressure switches for checking gas pressure (minimum
and maximum) prevent the burner from operating when gas
pressure is between the expected values. The specific function
of the pressure switches clearly reveals that the pressure switch
for controlling minimum pressure must use the contact which is
closed when the pressure switch detects a pressure value above
the value it is set to, while the pressure switch for controlling
maximum pressure must use the contact that is closed when the
pressure switch detects a pressure lower than the value it is set
to. Minimum and maximum gas pressure switches must be set
when the burner is tested. Setting depends on pressure detected
from time to time. Tripping of any of the gas pressure switches
(in the sense of opening the circuit) will therefore prevent the
equipment and therefore the burner from working. When the
1 - Main switch On/Off
2 - Programming keys
3 - Display
4 - Confirm or RESET key
5 - Fuse
Содержание BGN 250 DSPGN ME
Страница 2: ......
Страница 25: ...23 26 0006081538_201308 ITALIANO SCHEMA ELETTRICO EVENTUALE COLLEGAMENTO A MODULAZIONE ESTERNA...
Страница 26: ...24 26 0006081538_201308 ITALIANO START PER REGISTRATORE CORRENTE MINIMA DI OIONIZZAZIONE 1 4 A...
Страница 51: ...23 26 0006081538_201308 ENGLISH WIRING DIAGRAM POSSIBLE CONNECTION TO EXTERNAL MODULATION...
Страница 52: ...24 26 0006081538_201308 ENGLISH START FOR RECORDER MINIMUM IONISATION CURRENT 1 4 A...
Страница 55: ......