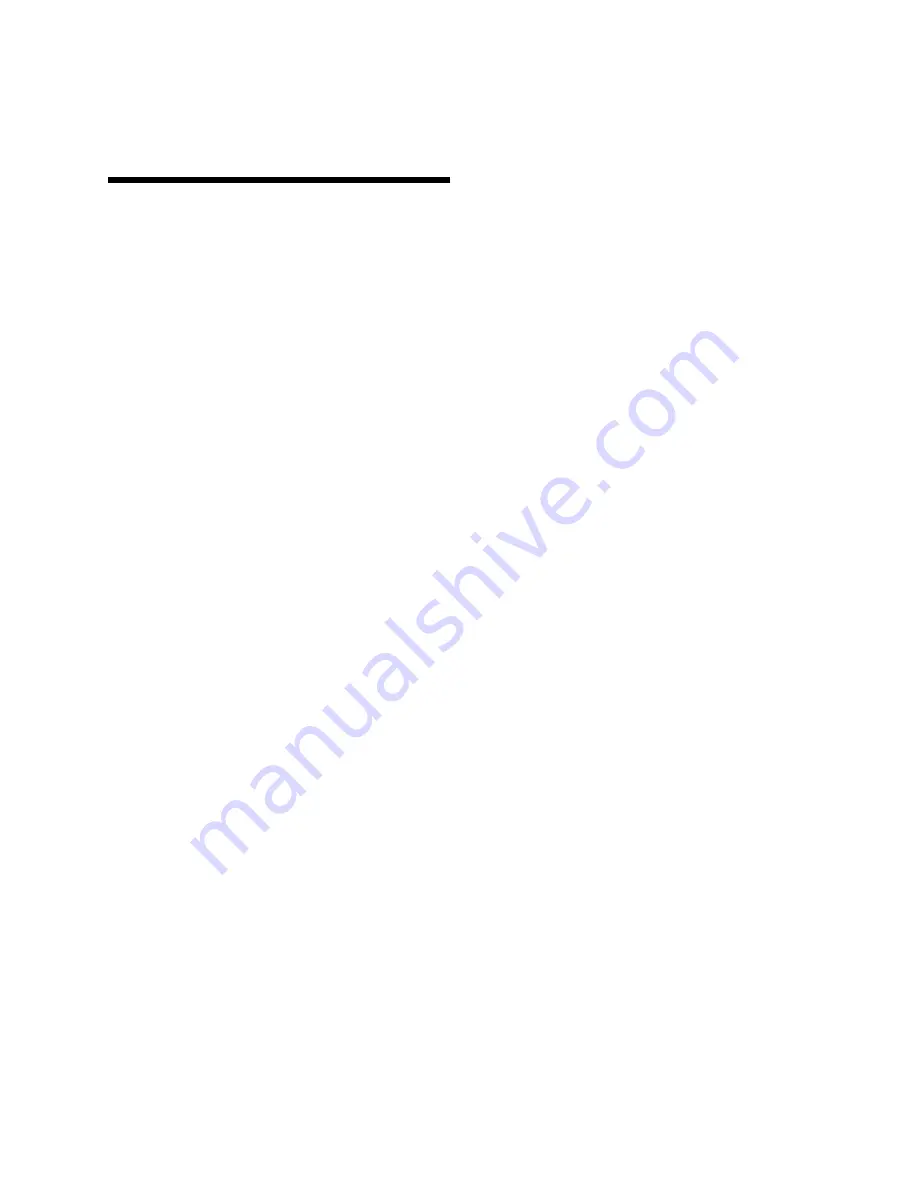
Operation
and Maintenance
7
INITIAL AND SEASONAL START-UP:
Prior to initial start-up or after a shut down period, the unit
should be thoroughly inspected and cleaned:
1.
Clean all debris from inlet air screens, fans, eliminators,
heat transfer sections, and the cold water basin.
2.
Drain the cold water basin (with basin strainers in
place) and flush to remove accumulated dirt.
3.
Remove, clean, and replace basin strainers.
4.
Turn the fan(s) by hand to ensure rotation without
obstruction.
5.
Check the locking collar on each fan bearing assem-
bly and tighten as required.
6.
Check and, if necessary, adjust the fan belt tension.
7.
Prior to seasonal start-up, lubricate the fan shaft and
motor bearings. The ball bearings are factory lubricat-
ed, but should be relubricated if the unit has been sit-
ting on site for more than a year before start-up.
8.
Check float operated make-up valve to be sure it is
operating freely.
9.
Fill the cold water basin with fresh water to the over-
flow level.
a. The initial biocide treatment should be applied at
initial start-up or before restart-up, where the basin
was completely drained. (see Water Treatment sec-
tion)
b. Following a shutdown period, where the basin was
not completely drained: it is recommended that
an initial shock treatment of appropriate bio-
cides be administered at restart-up to eliminate
accumulated biological contaminants.
10. Set the float on the make-up valve to shut off the valve
when the float is approximately 1/2” below the overflow
level.
11. On Closed Circuit Cooling Towers and Evaporative
Condensers, start the pump and check for the proper
rotation as indicated by the arrow on the pump cover.
On installations where the unit pump was not furnished
by the factory, a globe valve should be installed in the
pump discharge line and the pump flow rate adjusted
to the correct water flow and pressure (2 psig at spray
header connection). Pressure greater than 10.0 psig
may cause damage to the distribution system.
12. Inspect the spray nozzles and heat transfer section.
13. Start the fan and check for the proper rotation as indi-
cated by the arrow on the fan housing.
14. Check the voltage and current of all three legs of the
fan and pump motors. The current should not
exceed the nameplate rating. After prolonged shut-
downs, the motor insulation should be checked with a
megger insulation tester prior to restarting the motor.
To prevent motor overload, do not operate fan
motor without design water flow over unit.
15. Check the bleed system to be sure it is fully function-
al and the bleed rate has been properly adjusted prior
to putting the unit into operation (see “Water
Treatment”).
AFTER 24 HOURS:
After 24 hours of operating under load, the following services
should be performed:
1. Check the unit for any unusual noise or vibration.
2. Check the operating water level in the cold-water basin.
Adjust make-up float valve if necessary.
3. Readjust the fan belt tension.
4. Inspect the spray nozzles and heat transfer section.
OPERATION:
During operation, the unit should be inspected, cleaned,
and lubricated on a regular basis. The required services and
recommended frequency for each are summarized in Table
1 on page 6 of this bulletin.
SEASONAL SHUT-DOWN:
The following services should be performed whenever the
unit is to be shut-down for more than three days:
1. Drain the cold water basin and all piping that will be
exposed to freezing temperatures.
2. Clean and flush the cold water basin with the basin
strainers in place. Leave the cold water basin drain open
so rain and melting snow will drain from the unit.
3. Clean the basin strainers and reinstall.
4. Lubricate the fan shaft and motor bearings, motor base,
and motor base adjusting screw.
5. Close the shut-off valve in make-up water line and drain
all exposed make-up water piping.
6. Inspect the protective finish on the unit. Clean and refin-
ish as required.
7. For VF1 and VFL closed circuit cooling towers,
follow the coil freeze protection guidelines explained on
page 13.