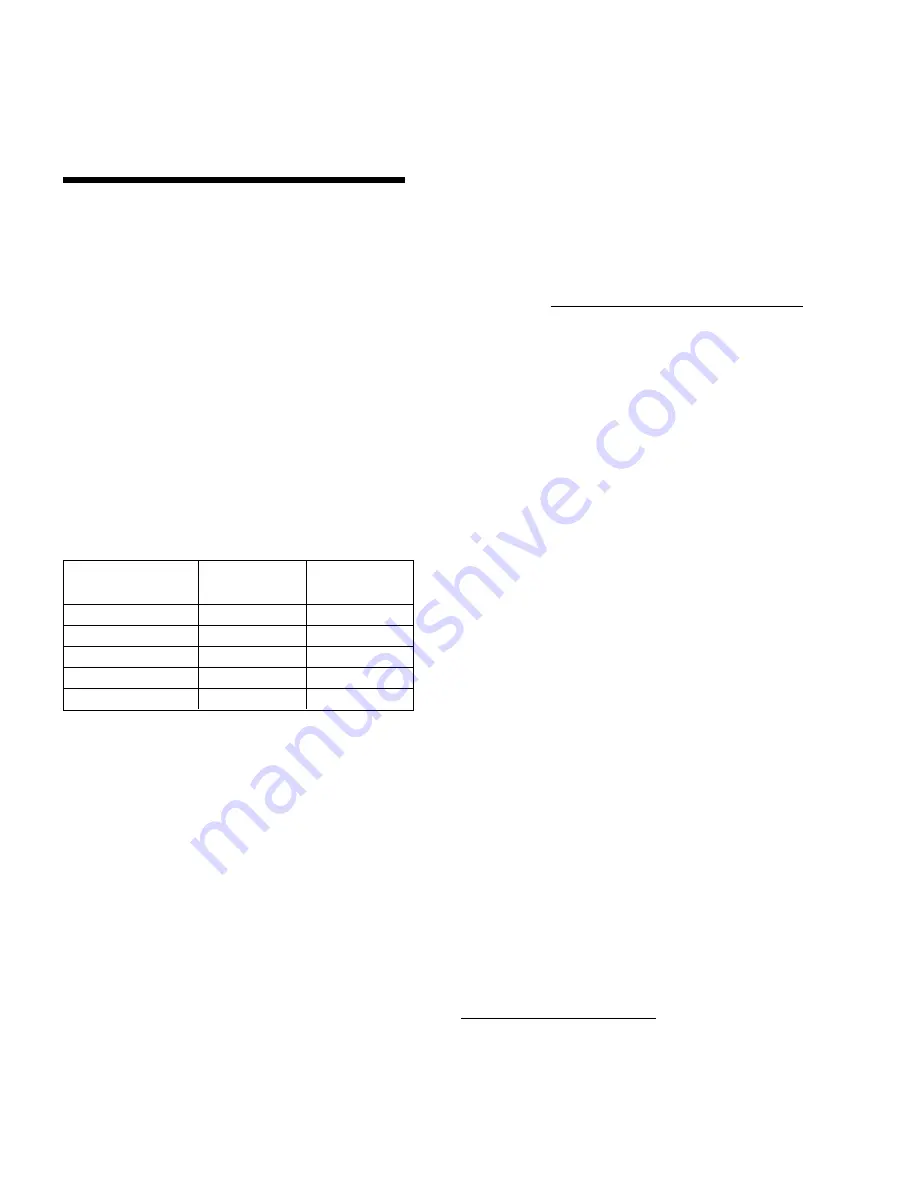
Recirculated Water Quality Guidelines
can be adjusted using the valve in the bleed line and
measured by filling a container of known volume while
noting the time period. The bleed rate and water quality
should be periodically checked to ensure that ade-
quate control of the water quality is being maintained.
The required continuous bleed rate may be calculated by
the formula,
Evaporation Rate
Bleed Rate =
Number of Cycles of Concentration – 1
The evaporation rate can be determined by one of the
following:
1.
The evaporation rate is approximately 2 GPM per 1
million BTU/HR of heat rejection.
2.
The evaporation rate is approximately 3 GPM per 100
tons of refrigeration.
3.
Evaporation Rate = Water Flow Rate x Range x .001
Example: At a flow rate of 900 GPM and a cooling range
of 10°F, the evaporation rate is 9 GPM (900 GPM x 10°F
x .001 = 9 GPM).
Note: For Closed Circuit Cooling Towers, the flow rate to
be used in this calculation is the flow through the coil.
Note: The bleed line must be furnished by others on VTO,
VT1 and VTL cooling tower models.
If the site conditions are such that constant bleed-off
will not control scale or corrosion and maintain the
water quality within the guidelines, chemical treat-
ment may be necessary. If a chemical treatment pro-
gram is used, it must meet the following requirements:
1.
The chemicals must be compatible with the unit con-
struction (zinc-coated) steel as well as all other mate-
rials used in the system (pipe, heat exchanger, etc.)
2.
Chemicals to inhibit scale and corrosion should be
added to the re-circulating water by an automatic
feed system on a continuously metered basis. This
will prevent localized high concentrations of chemicals,
which may cause corrosion. It is recommended the
chemicals be fed into the system at the discharge of
the recirculating pump on open cooling loops. They
must not be batch fed directly into the cold water
basin. For Series V coil products, chemicals should
be metered into the recirculating water over the coil.
3.
Acid water treatment is
not recommended unless
the unit(s) have been furnished with the BALTI-
BOND® Corrosion Protection System or is con-
structed of Type 304 stainless steel - in which cases
acid treatment can be used provided the requirements
of paragraph 1 and 2 above are maintained.
SYSTEM CLEANING
Closed Circuit Cooling Towers
With proper precautions, alkaline solution used to clean
condenser water systems prior to start-up may be circulat-
ed through a Series V or Low Profile Series V Closed
Circuit Cooling Tower.
Water
Treatment
CORROSION AND SCALE CONTROL
In Evaporative Cooling Products, cooling is accomplished
by the evaporation of a portion of the process water as it
flows through the unit. As this water evaporates, the impuri-
ties originally present remain in the recirculating water. The
concentration of the dissolved solids increases rapidly and
can reach unacceptable levels. In addition, airborne impuri-
ties are often introduced into the recirculating water, intensi-
fying the problem. If these impurities and contaminants are
not effectively controlled, they can cause scaling, corrosion,
and sludge accumulations which reduce heat transfer effi-
ciency and increase system operating costs.
The degree to which dissolved solids and other impuri-
ties build up in the re-circulating water may be defined as
the cycles of concentration. Specifically, cycles of concen-
tration is the ratio of dissolved solids (for example – total
dissolved solids (TDS), chlorides, and sulfates) in the re-
circulating water to dissolved solids in the make-up water.
For optimal heat transfer efficiency and maximum
equipment life, the cycles of concentration should be
controlled such that the re-circulating water is main-
tained within the guidelines list below.
14
Galvanized
Steel
BALTIBOND®
Corrosion
Protection System*
pH
Hardness as CaCO
3
Alkalinity as CaCO
3
Total Dissolved Solids
Chlorides
6.5 to 9.0
30 to 500 ppm
500 ppm max.
1200 ppm max.
250 ppm max.
7.0 to 9.0†
30 to 500 ppm
500 ppm max.
1000 ppm max.
125 ppm max.
† Units having galvanized steel construction and a circu-
lating water pH of 8.3 or higher will require periodic pas-
sivization of the galvanized steel to prevent “white rust,”
the accumulation of white, waxy, non-protective zinc cor-
rosion products on galvanized steel surfaces.
* Closed Circuit Cooling Towers and Evaporative
Condensers with BALTIBOND® Corrosion Protection
System and hot-dip galvanized coils must use the water
quality guidelines for galvanized steel units.
In order to control the cycles of concentration such that
the above guidelines are maintained, it will be necessary
to “bleed” or “blowdown” a small amount of recirculating
water from the system. This “bleed” water is replenished
with fresh make-up water, thereby limiting the build-up of
impurities.
Typically the bleed is accomplished automatically
through a solenoid valve controlled by a conductivity
meter. The conductivity meter set point is the water
conductivity at the desired cycles of concentration
and should be determined by a competent water
treatment expert. (Note: The solenoid valve and conduc-
tivity meter must be supplied by others.) Alternatively, a
bleed line with a valve can be used to continuously bleed
from the system. In this arrangement, the rate of bleed