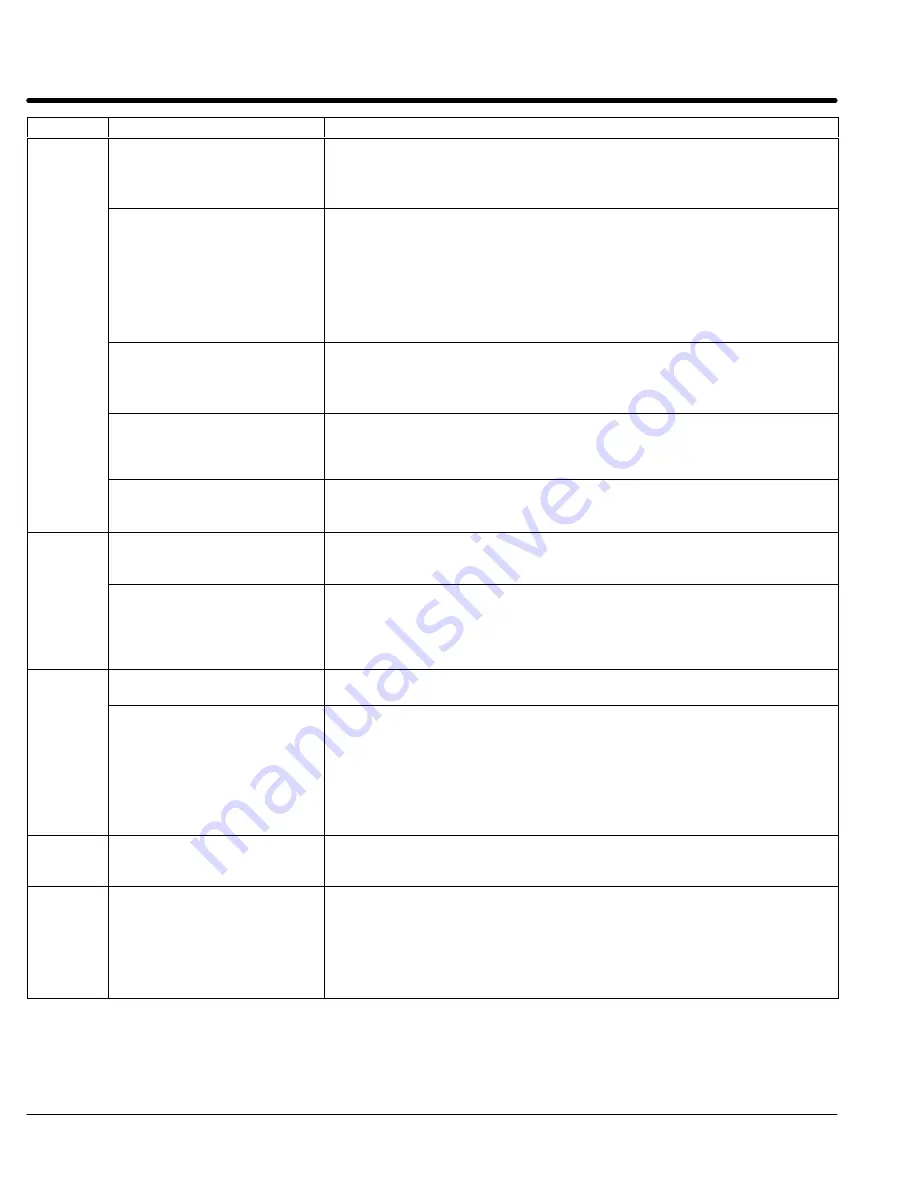
4-2 Troubleshooting and Maintenance
MN1269
Fault
Symptom
Corrective Action
No torque in one direction.
Check left or right limit switch wires to ensure that they are not tied to
common.
Verify that the proper limit switches are used.
Verify P1 position
N/A
No output in either direction.
Check interlock and reset wires to ensure that they are not tied to common.
Perform set–up procedure and verify all connections. Observe if all 4
green LED’s are lit on logic supply.
If all 4 LED’s are not lit, perform start–up procedure in Section 3 and
recheck all steps.
If only (bus) LED is lit, check AC logic fuse on top of unit to verify it is good
and set in the holder.
Verify P1 jumper is not missing.
N/A
Motor runs at uncontrolled
speeds
Verify that the servo control is not set for current mode.
Verify P6 position.
Verify that (T) pot is not set full CCW. Reverse tach leads and verify that
tach voltage is present at signal input connector when motor is running.
Oscillation in motor seen as
instability or rocking of motor
shaft. Motor may have
growling sound.
Refer to Start-up and Adjustment
Procedures for proper setting of (R) and (T) pots.
Motor exhibits a “dead zone“
when responding to a signal
input.
Verify that the bus voltage is sufficient for the motor.
Verify that inductance is not overly high (see specifications in Section 1
). Refer to Start-up procedures for proper setting of (R) pot.
Low output voltage from logic
power supply.
Check incoming power to logic power supply and verify that it is in specified
range. If in range, disconnect any external load on logic power and
reset servo control.
VE
Bus Voltage too high.
Check fuse on shunt regulator.
Recheck voltage and if problem still exists, disconnect power to each servo
control individually and isolate which servo control is drawing excess
current.
Check to ensure (T) pot is turned too far CCW.
RMS current output is
exceeded.
Check axis for instability (oscillation). Correct by turning (R) pot CCW.
EC
Overtemperature on servo
control.
If not instability, look for high tach noise (over 5% p–p) by using an
oscilloscope. If noise is present, check tach shielding.
If overloading is suspected, a larger servo control may be required.
Contact your supplier for alternatives.
Verify that air circulation is present. Check for overload using oscilloscope
on the DCS line to determine current to motor. 1V is approximately 1/10
of the peak rated output current. If not overloaded, unit should be
returned for repair.
GF
Current flow is detected at
ground potential
Can be caused by a short to ground. Remove armature connections and
check for short to ground. If none exists, remove servo control and reset
unit. If problem is resolved, servo control should be returned for repair.
SC
Rated peak current has been
exceeded.
Verify that motor has sufficient inductance (see Section 1.5.2). Reset servo
control and see if problem immediately reappears. If so, check for short
in motor. If motor is not shorted, unit has an internal short and should be
returned for repair.
If upon resetting servo control, the unit does not fault, cycle equipment
while watching for a fault during acceleration. If fault occurs, increase the
acceleration time, reset and cycle until problem is eliminated.
Servo Systems Co. • 115 Main Road • P.O. Box 97 • Montville, NJ, 07045-0097
(973) 335-1007 • Toll Free: (800) 922-1103 • Fax: (973) 335-1661
www.servosystems.com