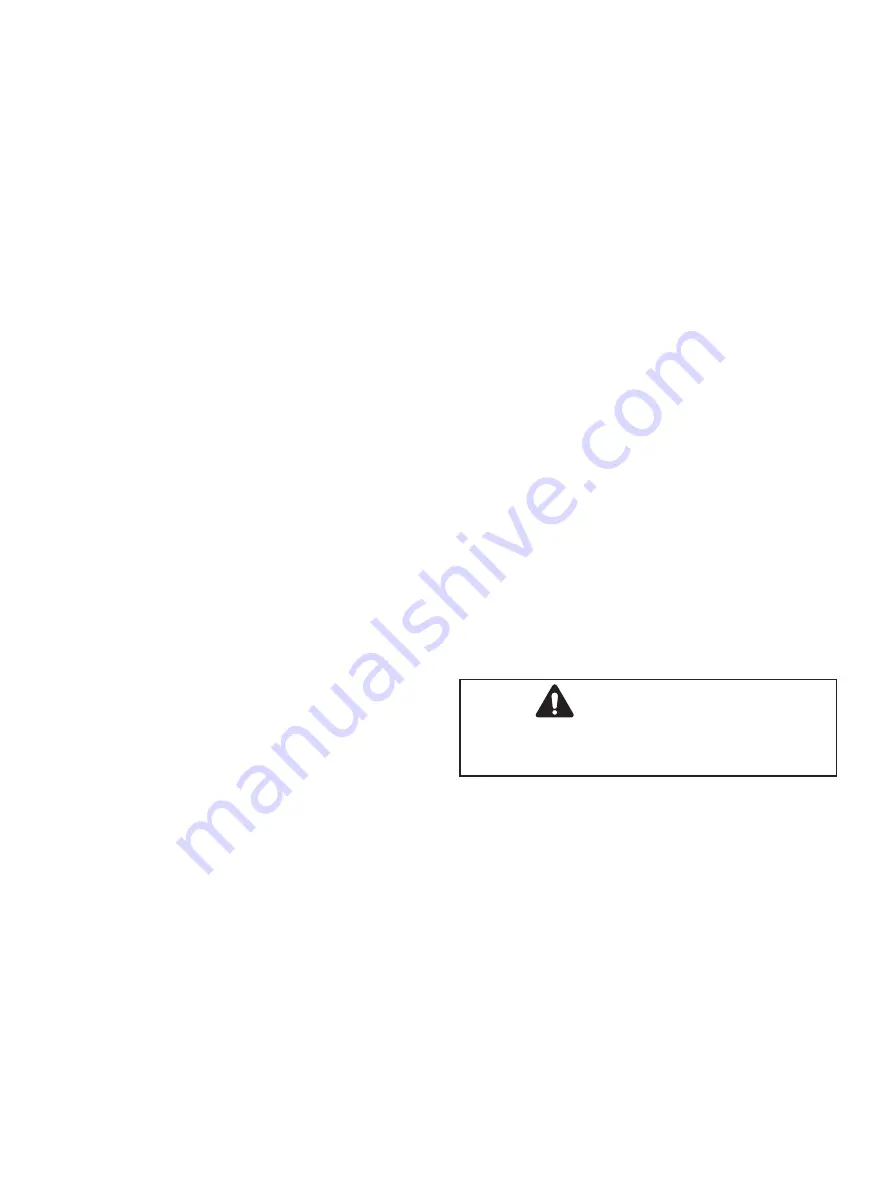
Masoneilan 33000 Series Butterfly Valves Instruction Manual | 9
Copyright 2020 Baker Hughes Company. All rights reserved.
7. Unpacking
Care must be exercised when unpacking the valve to prevent
damage to the accessories and component parts. Should any
problems arise, contact the local Baker Hughes Representative
or After Sales Department.
8. Installation
Before installing the valve in the line, clean piping and valve of all
foreign material such as welding chips, scale, oil, grease or dirt.
Gasket surfaces should be thoroughly cleaned to insure leak-
proof joints.
To allow for in-line inspection, maintenance or removal of the
valve without service interruption, provide a manually operated
stop valve on each side of the 33000 Series valve with a manually
operated throttling valve mounted in the by-pass line (See Figure
X).
The valve must be installed so that the controlled substance will
flow through the valve in the direction indicated by the flow arrow
located on the body (See Figure 11).
1. Always read the installation instructions carefully and work
to them.
2. The preferred orientation of a Butterfly valve is horizontal.
Butterfly valves may be installed in other orientations, but
deviations from this position, if not specified at the time of
order, could compromise performance.
3. Always remove all external and internal packaging together
with any temporary protective material.
4. Always carefully inspect the valve to ensure that no damage
has occurred in transit or during subsequent handling.
5. Care should be taken to prevent any foreign matter finding
its way through the valve during installation, which may
cause damage to the valve internals and inhibit good valve
performance.
6. Always ensure that the valve is installed so that it can be
safely operated and maintained without putting persons at
risk.
7. Always ensure adjoining pipework and connections are
square, true and adequately supported to prevent the
valve being subjected to stresses, which could affect its
performance.
8. Always ensure that the bolted connections are tightened
evenly to avoid placing a strain on the body/flanges.
9. Always ensure that the system into which the valve is to be
installed is clean and free from any foreign matter.
10. Never remove fitted components when valve(s) are being
installed - to do so will invalidate any warranty.
11. Always ensure that fast moving parts, which have a velocity
greater than 12mm per second, are guarded.
12. Always ensure that valves, which operate at high or low
temperatures, are positioned or lagged to prevent personnel
contacting surfaces, which could cause injury.
13. Before chemical cleaning, flush the valve with water under
a moderate pressure and operate the valve to allow the
gland packing to be saturated with water, this will prevent
the absorption of chemicals. During chemical cleaning, have
the valve in the half open position to create turbulence; this
will create the best cleaning effect. Passivate, and then flush
with water. With water in the valve, operate it several times
to flush away any chemicals that may have penetrated the
gland packing. If the valves are not to be used immediately,
use corrosion inhibitor in the water.
14. Always check with Baker Hughes prior to chemical cleaning
to ensure that no degradation of any sealing elements will
take place because of chemical attack.
15. Care should be taken not to over pressurize the system
during hydraulic testing. Use corrosion inhibited water
where necessary.
16. Function test the valve and system to ensure they are
working as intended. Manually rotate the spindle of the valve
to make sure that the vane clears the flanges and pipe when
it moves to the open position. (Note for power actuated
valves, disconnect the linkage before attempting to rotate
the shaft). Ensure power or air supplies are safe and correct
e.g. that electric actuators run in the correct direction, any
limit switches trip at the correct position and that devices are
available to isolate the electricity supply.
9. Air Piping
The actuators are designed to accept 1/4” NPT air supply piping.
Use 1/4” OD tubing (4 x 6 mm) or equivalent for all air lines. If the
supply airline exceeds 25 feet in length (7 meters) or if the valve
is equipped with volume boosters, then 3/8” tubing (6 x 8 mm) is
preferred. All connections must be free of leaks.
CAUTION
Do not exceed supply pressure indicated on serial
plate located on the yoke of the actuator.