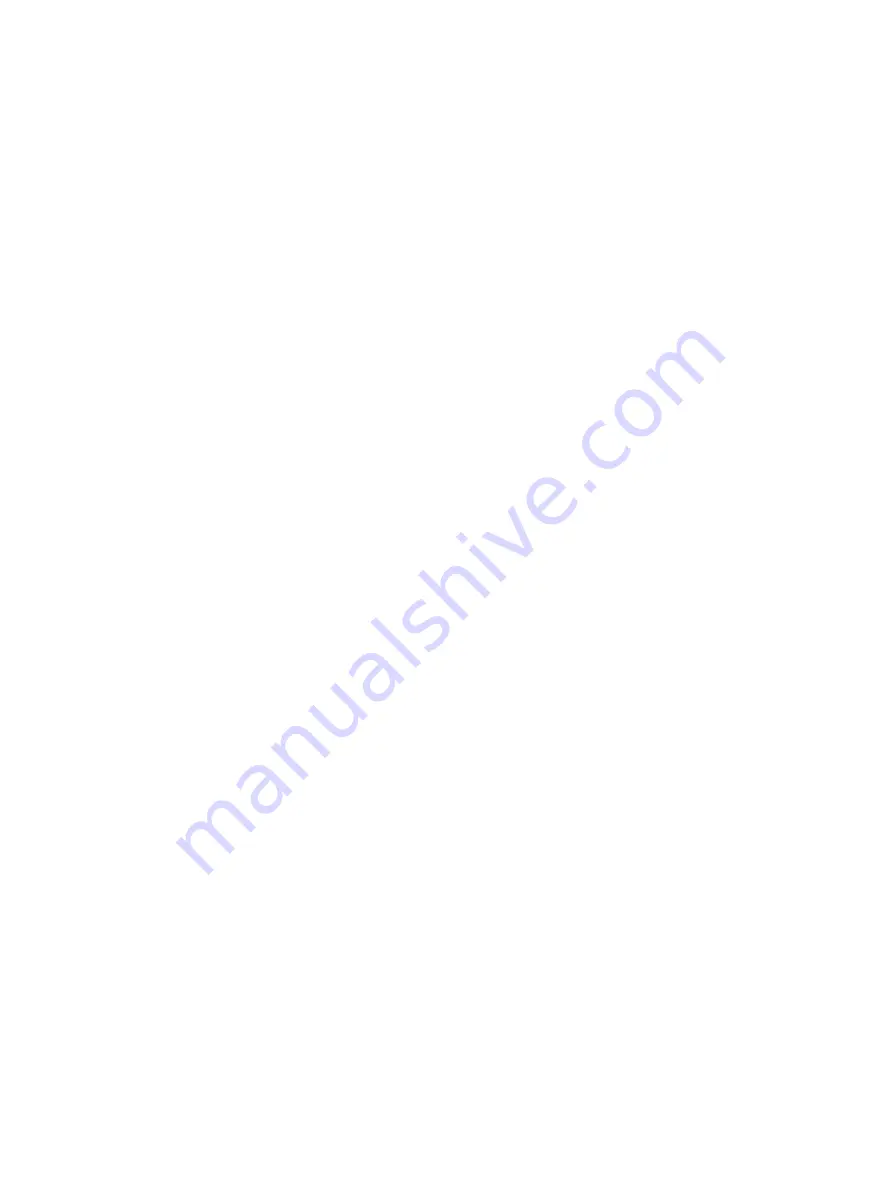
Consolidated 1982 Series Safety Relief Valve Manual
| 8
© 2020 Baker Hughes Company. All rights reserved.
VIII. Terminology for Pressure Relief Valves
A. Accumulation:
The pressure increase over
the maximum allowable working pressure of
the vessel during discharge through the valve,
expressed as a percentage of that pressure or in
actual pressure units.
B. Backpressure:
The static pressure existing on
the discharge side of a pressure relief valve:
1. Built-up Backpressure:
Pressure that
develops at the valve outlet as a result of
flow, after the valve has opened.
2. Superimposed Backpressure:
Pressure
in the discharge header before the valve
opens.
3. Constant Backpressure:
Superimposed
backpressure that is constant with time.
4. Variable Backpressure:
Superimposed
backpressure that will vary with time.
C. Blowdown:
The difference between set
pressure and reseat pressure of a valve,
expressed as a percentage of the set pressure
or in actual pressure units.
D. Cold Differential Set Pressure:
The pressure
at which the valve is adjusted to open on a test
stand. This pressure corrects for backpressure
when a pop action pilot’s vent is piped to the
main valve outlet.
E. Differential Between Operating and Set
Pressures:
Valves in process service will
generally give best results if the operating
pressure does not exceed 90% of the set
pressure. However, on pump and compressor
discharge lines, the differential required between
the operating and set pressures may be greater
because of pressure pulsations coming from a
reciprocating piston. The valve should be set as
far above the operating pressure as possible.
F. Lift:
The actual travel of the disc away from the
closed position when a valve is relieving.
G. Maximum Allowable Working Pressure:
The maximum gauge pressure permissible in
a vessel at a designated temperature. A vessel
may not be operated above this pressure or its
equivalent at any metal temperature other than
that used in its design. Consequently, for that
metal temperature, it is the highest pressure at
which the primary pressure relief valve is set to
open.
H. Operating Pressure:
The gauge pressure to
which the vessel is normally subjected in
service. A suitable margin is provided between
operating pressure and maximum allowable
working pressure. The suitable margin depends
on the type of pressure relief valve in service.
I. Overpressure:
A pressure increase over the
set pressure of the primary relieving device.
Overpressure is similar to accumulation when
the relieving device is set at the maximum
allowable working pressure of the vessel.
Normally, overpressure is expressed as a
percentage of set pressure.
J. Rated Capacity:
The percentage of measured
flow at an authorized percent overpressure
permitted by the applicable code. Rated
capacity is generally expressed in pounds per
hour (lb/hr) or kg/hr for vapors, standard cubic
feet per minute (SCFM) or m³ /min for gases,
and in gallons per minute (GPM) or Liter/min (L/
min) for liquids.
K.
Set Pressure:
The inlet static pressure at which
a pressure relief valve begins to operate under
service conditions. In liquid service, the inlet
pressure at which a valve starts to discharge
determines the set pressure. In gas or vapor
service, the inlet pressure at which the valve
pops or starts to leak, determines the set
pressure.
L. Simmer:
The audible passage of a gas or
vapor across the seating surfaces just before
a “pop”. The difference between this start-to-
open pressure and the set pressure is called
“simmer”. Simmer is generally expressed as a
percentage of set pressure.