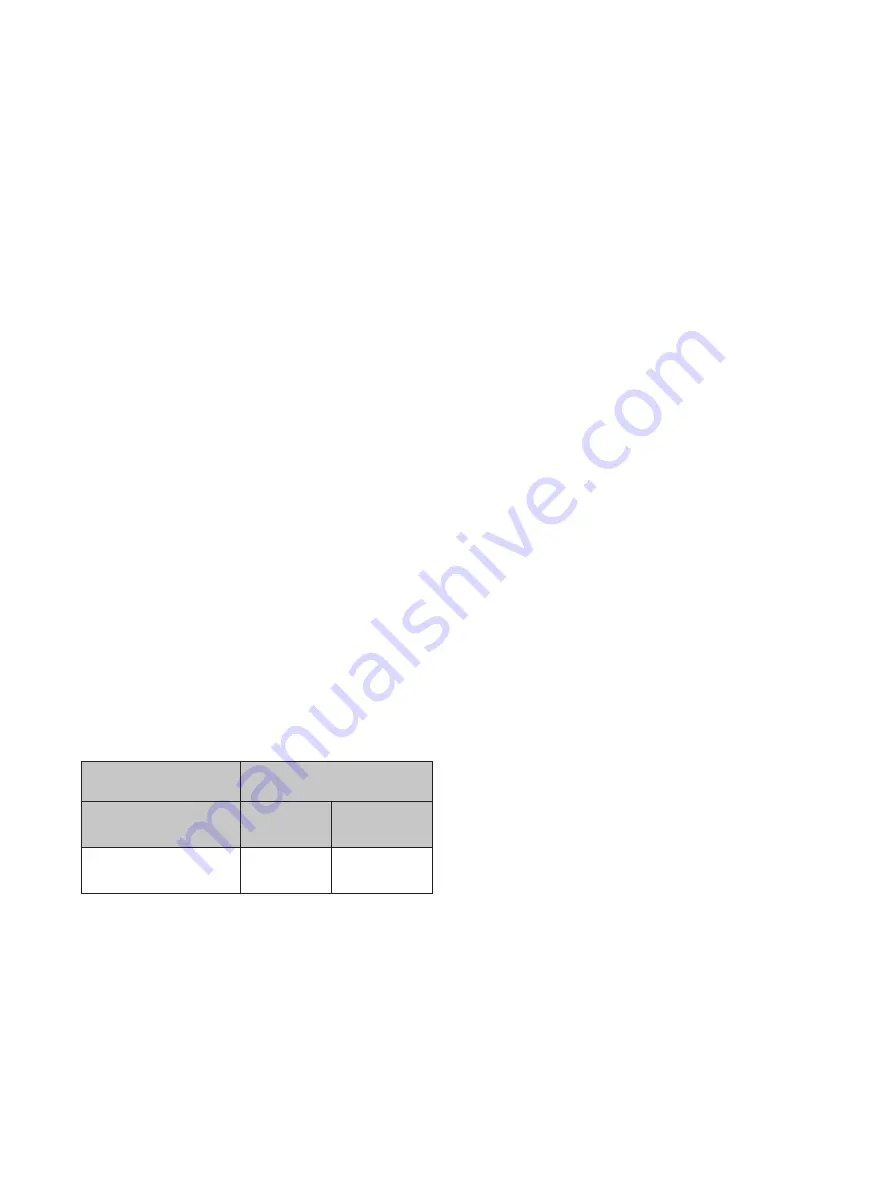
21 |
Baker Hughes
© 2020 Baker Hughes Company. All rights reserved.
XIII. Setting and Testing (Cont.)
Air
The air leakage test shall be performed with all
connections and openings in the body and bonnet
pressure tight. The cap with gasket which covers
the adjusting screw must be installed. Test valve for
leakage using API test fixture. The API leakage test
procedure is described below.
Per API Standard 527, (ANSI B142.1-72), a standard
test fixture consists of a piece of tubing .313”
(7.94mm) x .032” (0.81 mm) wall, one end of which
is joined to an adaptor on the valve outlet and the
other end of which is immersed .500” (12.70 mm)
below the surface of a reservoir of water.
The leakage rate for a valve with metal to metal
seats shall be determined with the valve mounted
vertically and using a standard test fixture as
described above.
“The leakage rate in bubbles per minutes shall
be determined with pressure at the safety relief
valve inlet held at 90 percent of the set pressure
immediately after popping for valves set 51 psig
(3.517 bar) and above. On valves set at 50 psig
(3.448 bar) and below, test for leakage at 5 psig
(0.345 bar) below the set pressure immediately after
popping. The test pressure shall be applied for a
maximum of 1 minute.”
Tightness Standard: The leakage rate in bubbles per
minute shall not exceed the following:
Max. Leakage Rate
Approx. Leakage Rate
(Bubbles / minutes)
ft
3
/ 24 Hr.
Liters/ 24 Hr.
40
0.60
16.99
Water
When a metal-to-metal seat valve is tested using
water as the test medium, there shall be no leakage,
as determined by seeing or feeling, when pressure is
held at 90% of set pressure.
Steam
When a valve is checked for tightness using steam
as the test medium, at 90% of the set pressure,
there shall be no visual or audible leakage after the
interior of the valve is allowed to dry after popping.
Valve is to be held at test pressure for a minimum
of three (3) minutes prior to checking for leakage.
If there is no visual or audible leakage, the valve is
acceptable.
G. Hydrostatic Testing
When hydrostatic tests are required after installation
of the safety relief valve, a test gag must be used.
Very little force (fingertight) on the test gag is
sufficient to hold hydrostatic pressures. Too much
force applied to the gag may bend the spindle
and damage the seat. After hydrostatic test the
gag must be removed and replaced by the sealing
plug furnished for this purpose. Test gags for
Consolidated Safety Relief Valves can be furnished
for all types of caps and lifting gears.
H. Manual Popping
After the valve has been installed and is in use, it
may be necessary to pop it by hand or by pressure
to make sure it has not become fouled by chemical
action, such as corrosion, and that it continues to
function properly. Consolidated Safety Relief Valves
are furnished when so ordered with packed or plain
lifting gears for hand popping.
F. Seat Leakage