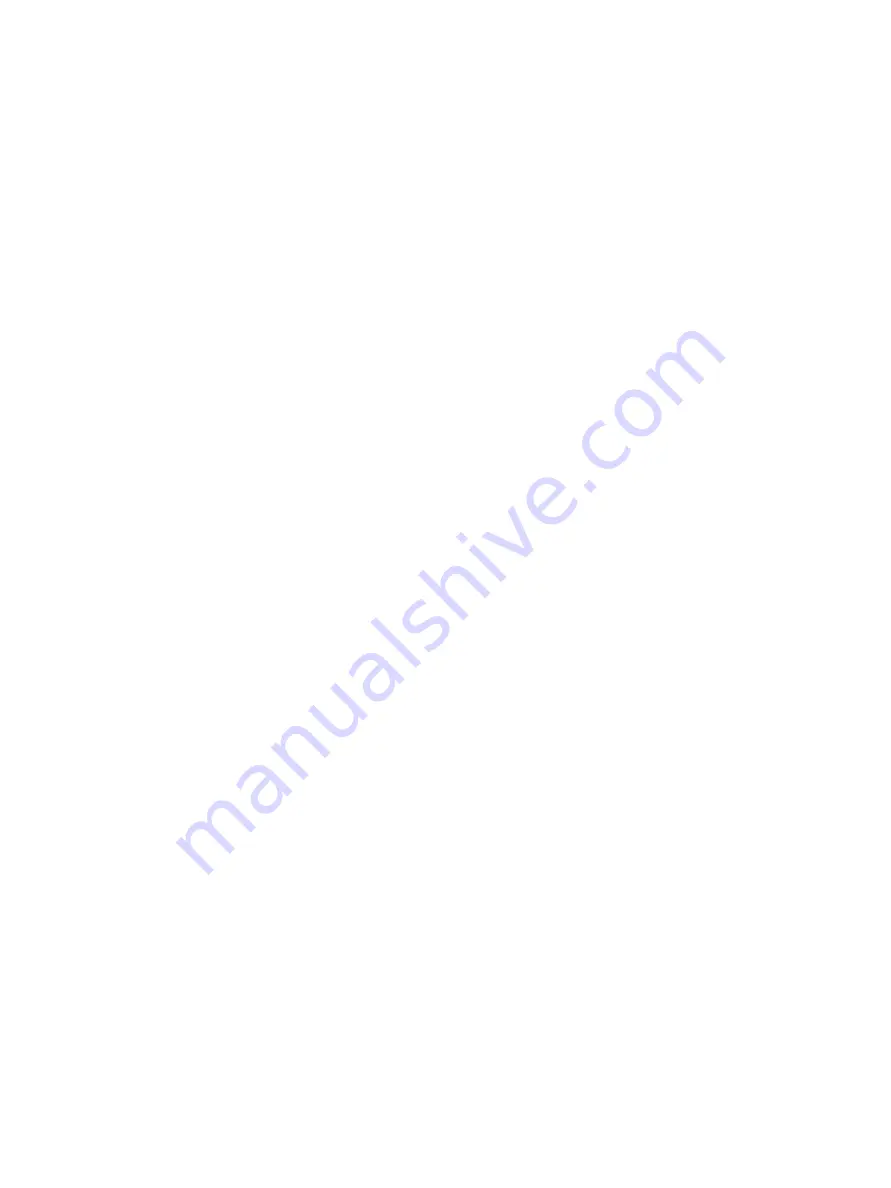
Consolidated 1982 Series Safety Relief Valve Manual
| 12
© 2020 Baker Hughes Company. All rights reserved.
X. Disassembly
(For the parts identification refer to Figures 1 to 4)
1. Remove cap (lifting gear). Remove cap gasket.
2. Remove adjusting ring pin and gasket. If the
existing valve action is to be restored, the
position of the ring should be determined by
turning it counterclockwise until it contacts the
roof of the disc recording the number of notches
that the ring is moved. Return to the original
position below the disc upon reassembly.
3. Loosen adjusting screw locknut. Record the
number of turns necessary to barely remove all
spring compression. Remove adjusting screw
from the bonnet. Return to original position when
reassembling.
4. With valve base held in vise, loosen the bonnet
to base connection (use strap wrench).
CAUTION: Do not distort base.
5. Remove bonnet, disc assembly, spindle, spring
and spring washer assembly from the base,
holding the spindle to be sure that the disc does
not drop.
6. Remove disc assembly, spindle, spring and
spring washers from bonnet.
7. Remove disc from spindle by engaging
the drop-out threads and turning the disc
counterclockwise.
Seat Repairing and Lapping
Reconditioning of the seating surface of the disc
and base is accomplished by lapping with a flat cast
iron ring lap coated with Grade No. 1000 KWIK-AK-
SHUN™ Silicon-Carbide compound, or equivalent.
Lapping tools are listed in Section XVI (Maintenance
Tools and Supplies).
The following method is recommended for lapping
seats.
1. Keep the work clean.
2. Always use a fresh lap. If signs of wearing (out
of flatness) is evident recondition the lap.
3. Apply a very thin layer of compound to the lap.
This will prevent rounding off the edges of the
seat.
4.
Keep the lap squarely on the flat surface and
avoid any tendency to rock the lap which will
cause rounding of the seat.
5.
When lapping, keep a firm grip on the part
to prevent the possibility of dropping it and
damaging the seat.
6. Lap using a reciprocating motion in all directions,
at the same time apply uniform pressure and
rotating the lap slowly.
7. Replace the compound frequently after wiping
off the old compound, and apply more pressure
to speed the cutting action of the compound.
8. To check the seating surfaces, remove all
compound from both the seat and the lap. Then
shine up the seat with the same lap using the
lapping motion described above. Low sections
on the seating surface will show up as a shadow
in contrast to the shiny portion. If shadows are
present, further lapping is necessary and only
laps known to be flat should now be used. Only
a few minutes will be required to remove the
shadows.
9. When the lapping is completed, any lines
appearing as cross scratches can be removed
by rotating the lap, which has been wiped clean
of compound, on the seat about its own axis.
10. The seat should now be thoroughly cleaned.
When the seats cannot be repaired by lapping,
they can be remachined using dimensions given
in Figure 5 and Table 1. The following procedure
can be used when machining the base seat:
a. Using a four-jaw chuck, align the base so
that it is running true.
b. Take light cuts on the seat surface until
all damage is removed. Reestablish the
.028” (0.71 mm) and B dimension per
Figure 6 and Table 2.
c. Lap the seat.
d. When minimum dimension “D” is
exceeded (Table 2), the base should be
discarded.