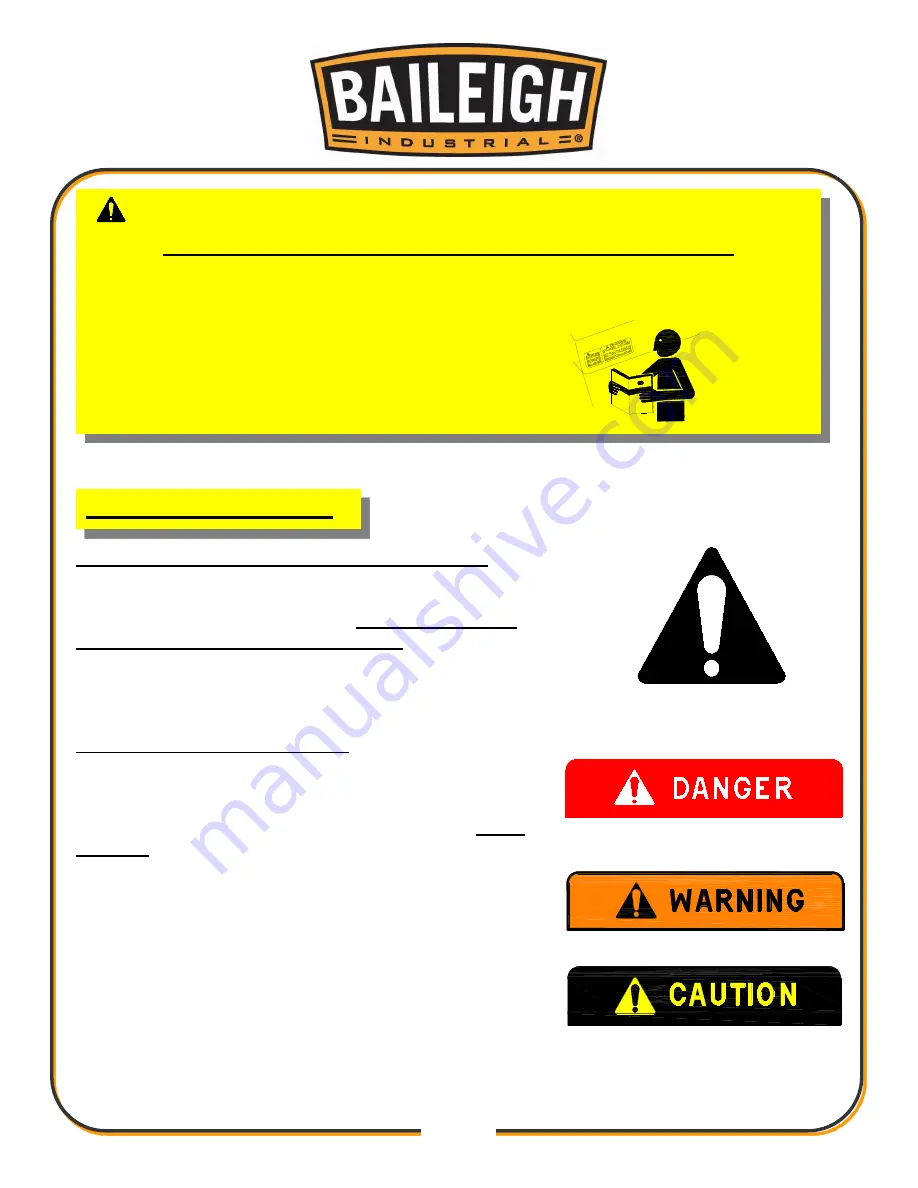
4
4
LEARN TO RECOGNIZE SAFETY INFORMATION
This is the safety alert symbol. When you see this symbol
on your machine or in this manual,
BE ALERT TO THE
POTENTIAL FOR PERSONAL INJURY!
Follow recommended precautions and safe operating
practices.
UNDERSTAND SIGNAL WORDS
A signal word
–
DANGER
,
WARNING
, or
CAUTION
is
used with the safety alert symbol.
DANGER
identifies a
hazard or unsafe practice that will result in severe
Injury
or Death
.
Safety signs with signal word
DANGER
or
WARNING
are
typically near specific hazards.
General precautions are listed on
CAUTION
safety signs.
CAUTION
also calls attention to safety messages in this
manual.
IMPORTANT
PLEASE READ THIS OPERATORS MANUAL CAREFULLY
It contains important safety information, instructions, and necessary operating procedures.
The continual observance of these procedures will help increase your production and
extend the life of the equipment.
SAFETY INSTRUCTIONS
Содержание SS-2822
Страница 29: ...26 26 Electrical Schematic...
Страница 53: ...50 50 BODY PARTS DIAGRAM...
Страница 55: ...52 52 ELEVATION PARTS DIAGRAM...
Страница 57: ...54 54 SPINDLE PARTS DIAGRAM Spindle and arbor is separate...
Страница 60: ...57 57 FENCE PARTS DIAGRAM...
Страница 62: ...59 59 ELECTRICAL PARTS DIAGRAM...