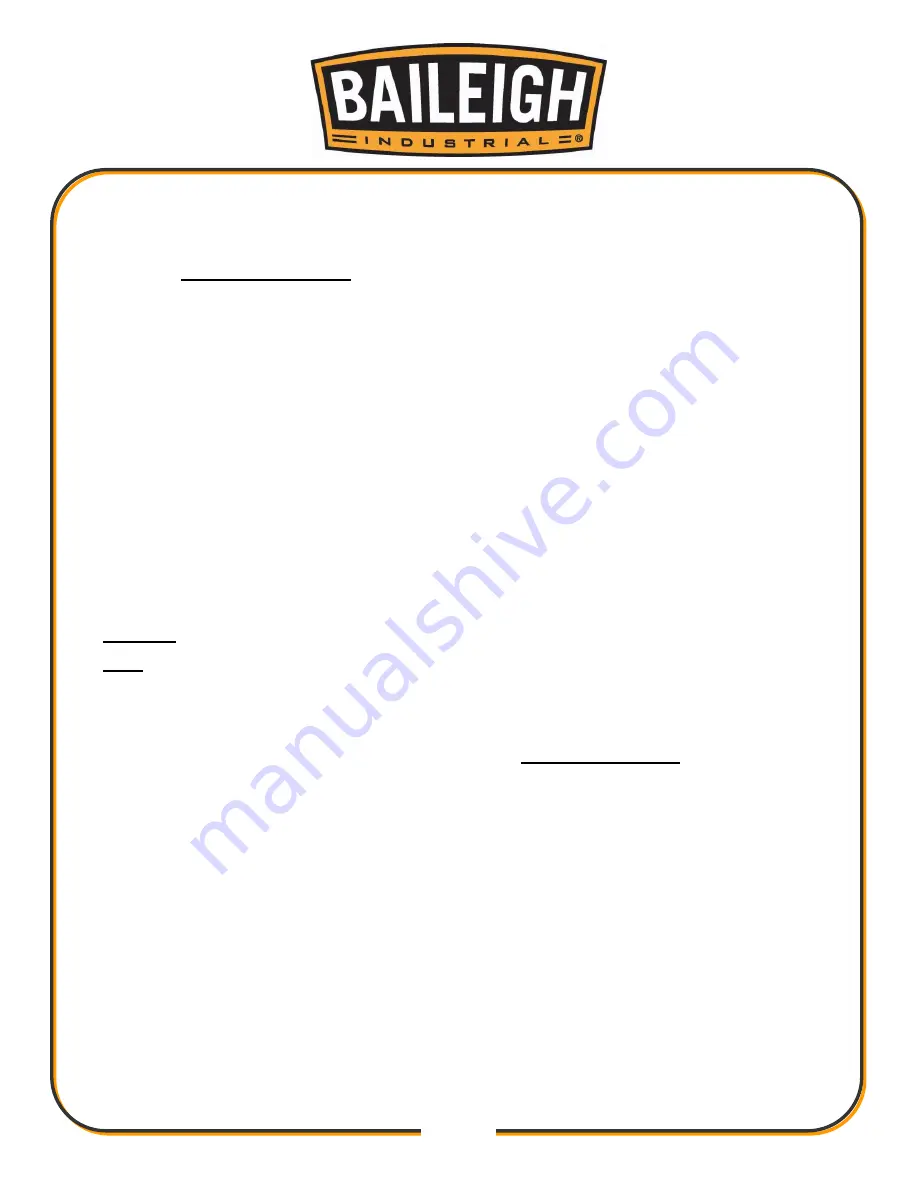
8
8
18. Be sure all equipment is properly installed and grounded according to national, state, and
local codes.
19. Inspect power and control cables periodically. Replace if damaged or bare wires are
exposed.
Bare wiring can kill!
20. Keep visitors a safe distance from the work area.
21.
Keep children away
. Children must never be allowed in the work area.
DO NOT
let them
handle machines, tools, or extension cords.
22.
Store idle equipment
. When not in use, tools must be stored in a dry location to inhibit rust.
Always lock up tools and keep them out of reach of children.
23. Turn off power before checking, cleaning, or replacing drill bits, or making adjustments or
servicing the machine.
24. Turn off main power to the machine and wait for the drill bit to stop turning before removing
debris, removing or securing the piece part, or changing the position of the worktable.
25. Never expose your hands or limbs to the cutting area while the machine is operating.
26. Make sure it is possible to move freely around the machine and associated equipment. The
floor should be kept clean and dry, and the surrounding area well illuminated, so that work
can be performed safely.
27.
Properly
lock the drill bit in the chuck before operating the machine.
28.
Hold
the piece part firmly against the table.
DO NOT
attempt to drill a piece part that does
not have a flat surface against the table, or that is not secured by a vise. Prevent the piece
part from rotating by clamping it to the table or by securing it against the drill press column.
29. Never leave the machine running while unattended. Turn the power OFF. Do not leave the
machine until the spindle comes to a complete stop.
When the machine
is
NOT
in use, the
drill bit should
NOT
be rotating.
30. Remove adjusting keys and wrenches before turning drill press on. Never start the machine
before clearing the table of all objects (tools, scrap pieces, etc.)
31.
DO NOT
bypass or defeat any safety interlock systems. Never use the drill press without the
swing-away safety guard. Use the safety guard. The safety guard prevents chips from flying
out and causing cuts or burns.
Содержание DP-3814B
Страница 17: ...15 15 GETTING TO KNOW YOUR MACHINE K G M E O I D R S P Q B J A C H N F L...
Страница 33: ...31 31 PARTS DIAGRAM...
Страница 38: ...36 36 NOTES...
Страница 39: ...37 37 NOTES...