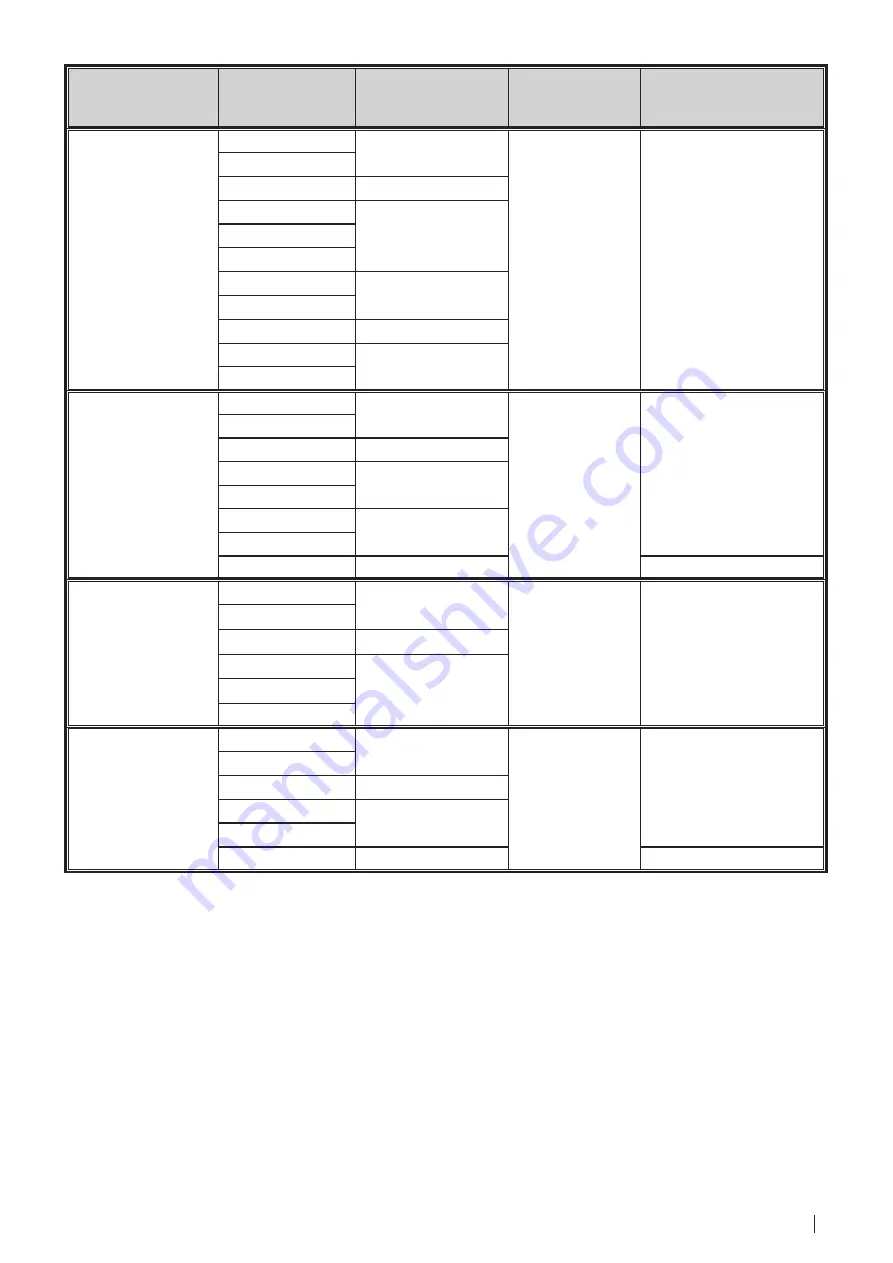
5-4
Chapter 5 Reference Table for Selection of Tools and Materials
Material
Cutting Tool
Maximum
Stepdown Value
Spindle Speed
Feed Rate
Epoxy Tooling
Board
4025C150
5mm (0.2 in.)
100%
1500 mm/min
59 inch/min
4050C150
4100C150
4mm (0.16 in.)
4635V030
1mm (0.04 in.)
4635V060
4635V090
4400H150
3mm (0.12 in.)
6600H300
4100G040
1mm (0.04 in.)
4250B120
3mm (0.12 in.)
4400B150
EVA Foam
4025C150
5mm (0.2 in.)
100%
2500 mm/min
98 inch/min
4050C150
4100C150
4mm (0.16 in.)
4400H150
5mm (0.2 in.)
6600H300
4250B120
3mm (0.12 in.)
4400B150
4100G040
1mm (0.04 in.)
1500 mm/min (59 inch/min)
Modeling Wax
4025C150
1.5mm (0.06 in.)
100%
1500 mm/min
59 inch/min
4050C150
4100C150
2 mm (0.08 in.)
4100G040
1mm (0.04 in.)
4250B120
4400B150
Styrofoam
4025C150
5mm (0.2 in.)
100%
2500 mm/min
98 inch/min
4050C150
4100C150
4mm (0.16 in.)
4250B120
3mm (0.12 in.)
4400B150
4100G040
1mm (0.04 in.)
1500 mm/min (59 inch/min)
Note:
1. This chart is just for your information, the actual settings and selections depend on the real
material characteristics of the workpiece and the performance of the cutting tool.
2. Properly adjust the spindle rate and feed rate based on the melting point and hardness of the
material.
3. The total effective cut depth must not be greater than the thickness of the workpiece unless it’s
meant to be cut through.
4. The total effective cut depth must be less than or equal to the “max. carving depth” plus the
offset value.
5. All these parameters only apply to the Bravoprodigy EDIT and CNC software.