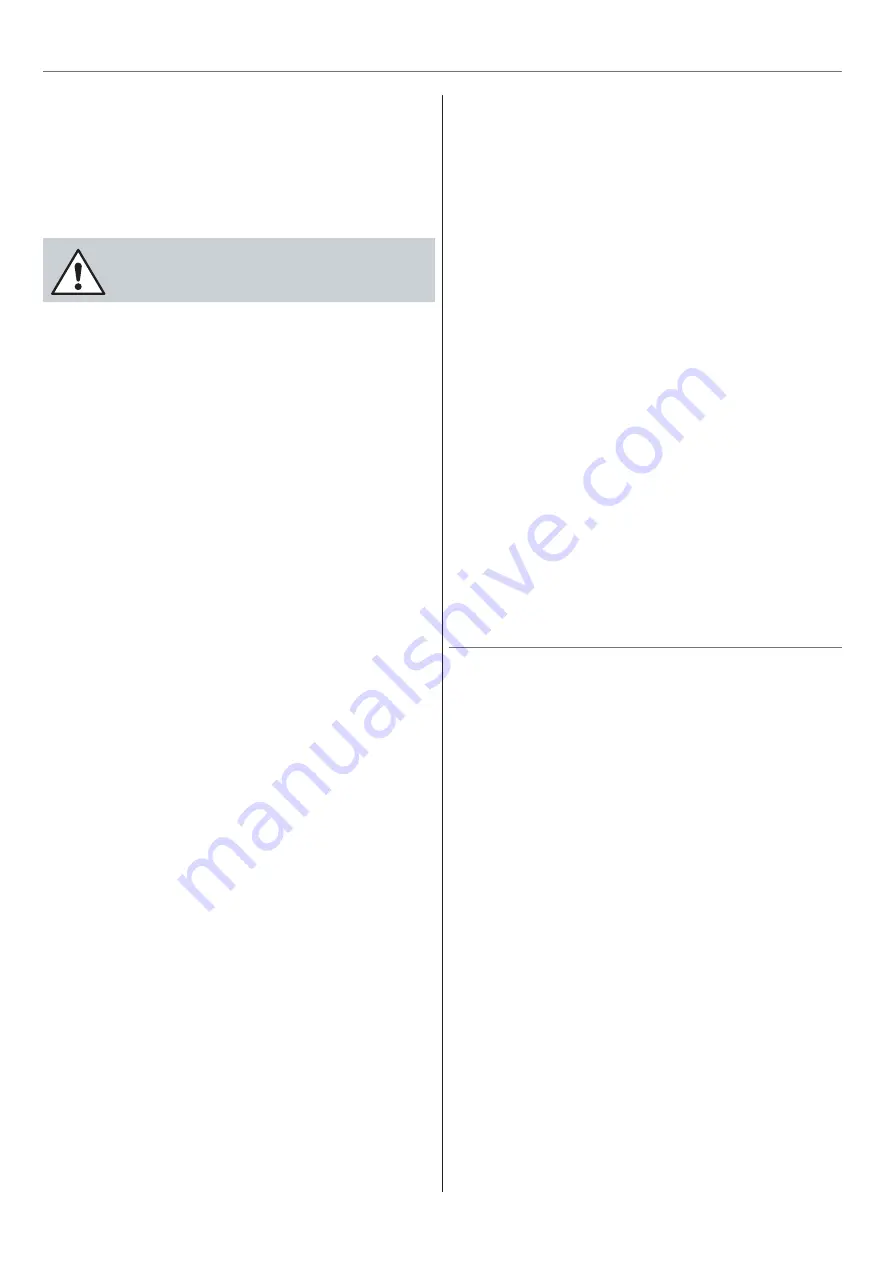
General Instructions for 230V Machines
6
The following suggestions will enable you to observe
good working practices, keep yourself and fellow
workers safe and maintain your tools and equipment
in good working order.
This machine is supplied with a moulded 16 Amp. Plug
and 3 core power cable. Before using the tool inspect
the cable and the plug to make sure that neither are
damaged. If any damage is visible, have the tool
inspected/repaired by a suitably qualified person. If it is
necessary to replace the plug, it is preferable to use an
‘unbreakable’ type that will resist damage on site. Only
use a 16 Amp plug, and make sure the cable clamp is
tightened securely. Fuse as required. If extension leads
are to be used, carry out the same safety checks on them,
and ensure that they are correctly rated to safely supply
the current that is required for your machine.
If the machine gets wet; dry it off as soon as possible
with a cloth. Do not use 230V a.c. powered tools in damp
locations and do not trail extension cables across wet
areas. Keep the tools clean, do not use any solvents or
cleaners, as these may cause damage to any plastic parts
or to the electrical components.
Keep the work area as uncluttered as is practical, this
includes personnel as well as material.
Under no circumstances should CHILDREN be allowed
in work areas.
It is good practice to leave the machine unplugged until
work is about to commence, also make sure to unplug
the machine when it is not in use, or unattended. Always
disconnect by pulling on the plug body and not the
cable. Once you are ready to commence work, remove
any tools used in the setting operations (if any) and
place safely out of the way. Re-connect the machine.
Carry out a final check e.g. check the cutting tool, drill bit
etc., are securely tightened in the machine, check you
have the correct speed and function set, check that the
power cable will not ‘snag’ etc.
Make sure you are comfortable before you start work,
Good Working Practices/ Safety
Mains Powered Tools
Work Place/Environment
Mains Powered Tools Primary Precautions
WARNING! KEEP TOOLS AND EQUIPMENT
OUT OF THE REACH OF YOUNG CHILDREN
balanced, not reaching etc. If the work you are carrying
out is liable to generate flying grit, dust or chips, wear the
appropriate safety clothing, goggles, gloves, masks etc. If
the work operation appears to be excessively noisy, wear
ear-defenders. If you wear your hair in a long style,
wearing a cap, safety helmet, hairnet, even a sweatband,
will minimise the possibility of your hair being caught
up in the rotating parts of the machine, likewise,
consideration should be given to the removal of rings
and wristwatches, if these are liable to be a ‘snag’ hazard.
Consideration should also be given to non-slip footwear,
etc. If you are allowing another person to use the
machine, ensure that they are suitably qualified to use it.
Do not use the machine if you are tired, your attention is
wandering or you are being subjected to distraction. A
deep cut, a lost fingertip or worse is not worth it!
Check that cutters, drills etc., are the correct type and
size, are undamaged and are kept clean and sharp, this
will maintain their operating performance and lessen the
loading on the machine. Above all, OBSERVE…. make
sure you know what is happening around you, and USE
YOUR COMMON SENSE.
Make sure the saw blade is the correct type for the job in
hand.
Do not force the saw, if the saw begins to ‘stall’ you are
‘forcing the cut’ or over working the saw. Ensure that
the saw blade is clean and sharp. Resin build up on
the blades will increase the friction of the saw passing
through the timber, and cause over heating of the blade,
blunt teeth will work harder tearing the fibre of the
timber as opposed to shearing it, also with subsequent
overheating. Both faults unnecessarily load the machine
beyond normal usage, and shorten its longevity.
Do not use blades that are damaged in any way.
Do not remove the blade guard. The design of the riving
knife on the machine will not allow for slotting or ‘blind’
grooving, so there is no reason to remove the guard.
There is adequate clearance under the guard for the
capacity of the machine.
Do not use any blades that cut a smaller kerf than the
riving knife thickness. Make sure the riving knife is
correctly adjusted to the blade and is securely fastened.
If the table insert becomes damaged or broken, and will
not support the timber ‘up close’ to the blade, replace it.
Specific Safety Precautions
Содержание 107715
Страница 1: ...AT254PS13 Panel Saw AT 13 01 2021 BOOK VERSION 5 Code 107715 Original Instructions...
Страница 4: ...What s Included 4 11 23 10 19 9 7 8 30 16 6 2 27 17 13 2 2 28 3 5 4 22 24 26 12 14 15...
Страница 21: ...Machine Footprint 21 3 210mm 3 720mm 1 120mm 1 Metre extension...
Страница 22: ...Machine Footprint 22 Rear Extension Table Right Hand Table 3 210mm Sliding Table Extension Table...
Страница 39: ...Exploded Diagrams Lists 39 DIAGRAM A Continues over...
Страница 41: ...Exploded Diagrams Lists 41 DIAGRAM B Continues over...
Страница 43: ...Exploded Diagrams Lists 43 DIAGRAM C Continues over...
Страница 45: ...Exploded Diagrams Lists 45 DIAGRAM D Continues over Continues over...
Страница 47: ...Exploded Diagrams Lists 47 DIAGRAM E Continues over...
Страница 49: ...Notes 49...
Страница 50: ...Notes 50...
Страница 51: ...Notes 51...