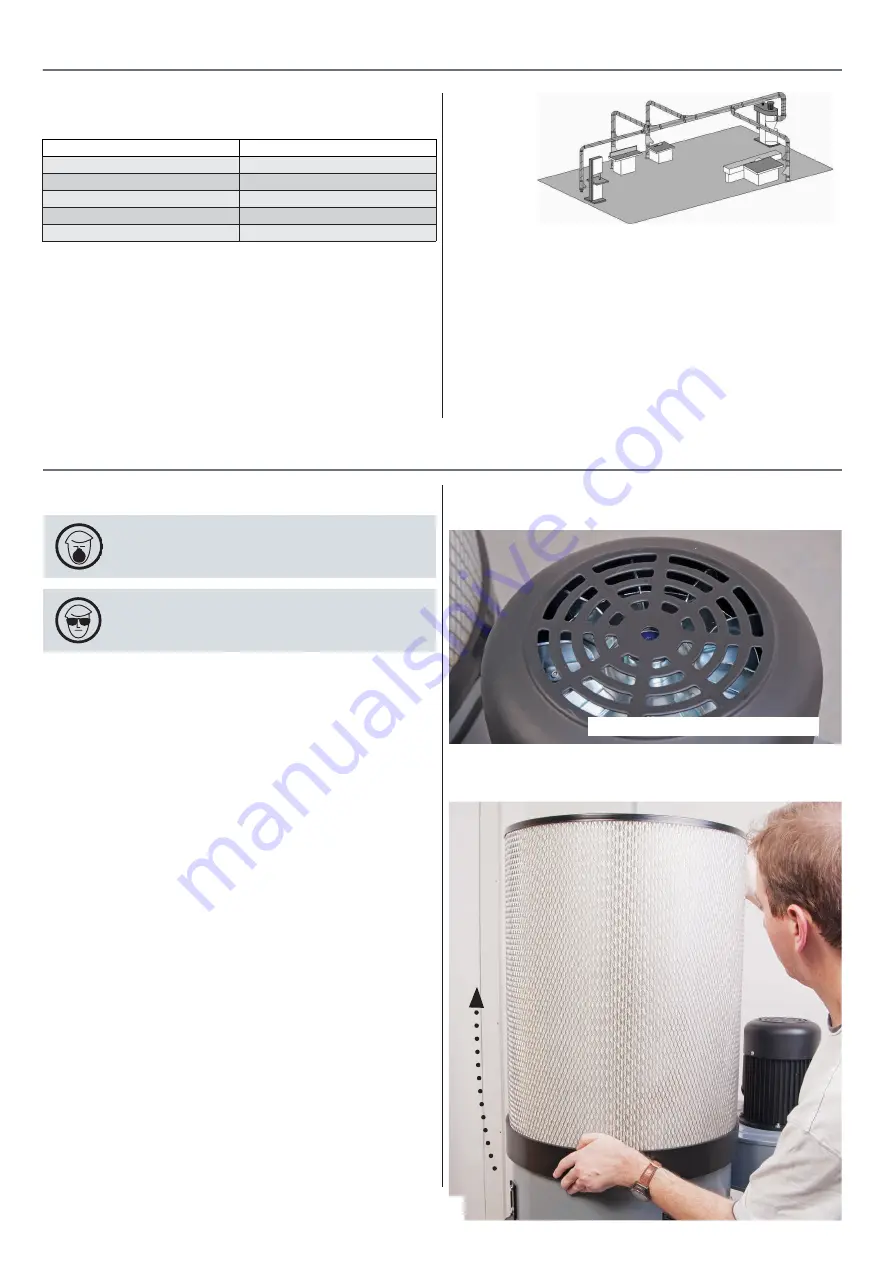
20
Ducting System
Ducting System
Maintenance
20
WARNING! always wear a dust mask
WARNING! Always wear eye protection
Daily
• Empty the collection bag before it overflows, wear a dust mask
whilst removing and emptying the bag.
Weekly
• Check the inlet and outlet duct and remove any accumulated
sawdust.
•Check the inlet hoses for splits and cracks, repair as necessary.
• Check the dust collection bag for wear and tear, especially
around the neck of the retaining belt. If wear
or fraying is occurring, replace the bag.
• Check the motor for dust, sawdust, shavings etc, build up. If
this has occurred, clean with a vacuum cleaner, see fig 45.
• Move the shaker paddle handle back and forth to remove any
built up dust and debris from inside the filter.
Monthly
• Remove the filter securing belt and remove the filter assem-
bly, see fig 46 using an ‘M’ class vacuum cleaner, clean inside the
filter.
Basic Maintenance
Fig 45
Fig 46
Clean the motor housing vents
Many manufacturers will state the volume of air required for each machine in their manual. If
not, note the size of the extraction port and use the chart below
Basic design
• Keep it simple, don’t over complicate the system.
• Keep it straight, ducting runs should all be straight with as few bends as possible.
• Keep transfer duct as big as required by the extractor, this should get larger towards the
extractor.
• Keep flexible duct to a minimum. If the machine cannot be connected to the system by
solid ducting only then should flexible ducting be used for the final connection.
• Keep branches joining the duct to a maximum of 45° When branches join the main duct
ideally they must enter at the side or the top at an angle of a maximum of 45° towards the
direction of flow.
• Fit Blastgates to maximise efficiency and balance the system.
The negative pressure inside the ducting draws air into the system. Incorrect sizing of the
duct, too many bends coupled to lots of flexible hose induces losses into the system and in
badly designed systems this is akin to leaving the hand brake on in a vehicle.
Example: for a single machine with a 100mm port an extractor of a minimum of 700m³/hr
will be sufficient. For multiple machines count the number of extraction ports per size, multi-
ply the number of each size by the volume of air required. Then add the results per outlet size
to give you a total volume of air required. This total is for all the machines operating at the
same time. You then must decide which and how many machines will be used at the same
time. Divide the total volume of air required by this number and add 500m³/hr. Choose an
extractor that gives the airflow required by your calculations. Look at the main inlet size of the
extractor, this is the size of the main duct to be used. In larger systems the ducting should get
larger towards the extraction unit as more machines that are in use are added to maintain the
correct air speed in the duct. This is very important; if the airflow is too low a build up of dust
and debris will occur and is a fire and explosion risk. If the air speed is high then the system
will be noisy but there will be no deposits in the ducting. Always use blastgates to close off
airflow to machines that are not in use.
outlet size
volume of air required
50
200 m³/hr
100
700 m³/hr
125
1100 m³/hr
150
1600 m³/hr
200
2800 m³/hr
Gerneral Info
Содержание AT170E
Страница 4: ...4 What s Included AT60E Extractor 1 6 7 8 9 10 11 12 2 3 4 5 ...
Страница 6: ...6 What s Included AT170E Extractor 23 26 27 a b c d e f g h i j k 24 25 l m 29 n ...
Страница 24: ...24 Exploded Diagrams Parts Lists AT60E ...
Страница 26: ...26 Exploded Diagrams Parts Lists AT170E ...
Страница 27: ...27 Exploded Diagrams Parts Lists AT60E Filter Assembly AT170E Filter Assembly Continues Over ...
Страница 30: ...30 Notes ...
Страница 31: ...31 Notes ...