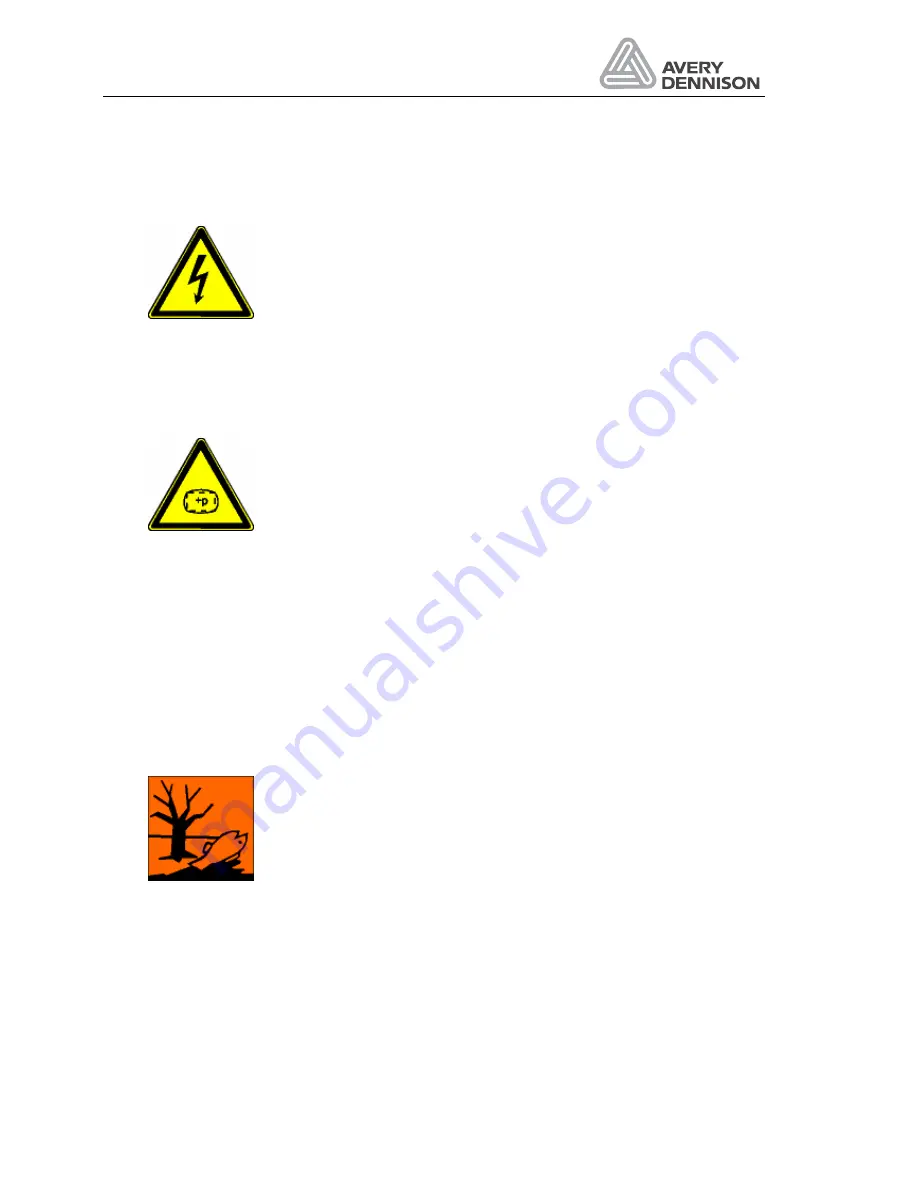
Operators Manual
ALS 330/430
Release 8/07
Page 10
Important Notes
1.2.7
Work on the electrical equipment
Repair work on the electrical equipment of the machine may only be
performed by a trained electrician!
Electrical equipment must be checked on a regular basis!
Loose connections must be fixed again!
Exchange damaged lines/cables immediately!
Always keep the switch cabinet closed! Access is only allowed to
authorised personnel with keys/tools!
Never wash down switch cabinets and other housings of electrical
equipment with a water hose for cleaning!
1.2.8
Work on pneumatic equipment
Maintenance and repair work on pneumatic equipment may only be
performed by specially trained personnel!
Before starting maintenance and repair work, depressurise the
pneumatic equipment of the machine!
By way of precautionary maintenance, exchange hose pipes on a
regular basis, even if there is no damage to be detected!
(Observe the manufacturers’ instructions!)
Before setting into operation after maintenance or repair works
•
check if loosened screwed connections are tight
•
make sure that removed coverings are re-installed
After termination of maintenance and repair work and before re-
starting the production, make sure that
•
all materials, tools, and other equipment required for maintenance
and repair work are removed from the operating area of the plant
•
all safety devices of the plant function in a faultless manner!
1.2.9
Observe environmental regulations
During any and all work on and with the machine, the statutory duties
concerning prevention of waste and the proper waste
disposal/recycling regulations must be observed.
Especially in the case of installation, repair and maintenance work,
substances which are hazardous for the water, such as detergents
containing dissolvents, may not pollute the soil or get into the sewage
system!
These substances must be stored, transported, collected, and
disposed of in appropriate containers!
Содержание ALS 330
Страница 1: ...Ausgabe 08 07 Artikelnummer 0089999 06...
Страница 2: ......
Страница 6: ...Operators Manual ALS 330 430 Release 8 07 Contents...
Страница 18: ...Operators Manual ALS 330 430 Release 8 07 Page 16 Description...
Страница 37: ...Operators Manual ALS 330 430 Release 8 07 Page 35 Operation...
Страница 38: ......
Страница 50: ......
Страница 73: ...Operators Manual ALS 330 430 Release 8 07 Page 65 Connections and signals l Figure 29 Internal I O connector...
Страница 75: ...Operators Manual ALS 330 430 Release 8 07 Page 67 Connections and signals 8 5 Electronic diagrams...
Страница 76: ...Operators Manual ALS 330 430 Release 8 07 Page 68 Connections and signals Figure 30 Wiring diagram...
Страница 79: ...Operators Manual ALS 330 430 Release 8 07 Page 71 Connections and signals...
Страница 80: ......
Страница 84: ...Operators Manual ALS 330 430 Release 8 07 Page 76 Errors and warnings...
Страница 92: ......