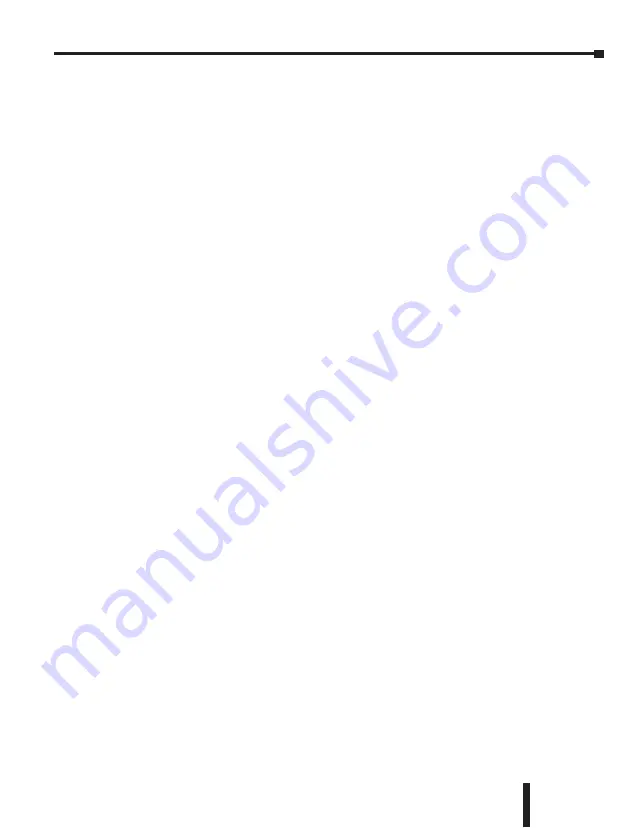
3–11
3.3.4 – Electro-Mechanical Methods Of Starting
Method A: Direct-on-Line
The most simple means of controlling energy flow to an induction motor is to interrupt the power
supply by a single contactor. Very widely applied, the method is known variously as “direct-on-
line”, “across-the-line”, “direct”, etc., and is the usual form of control where low cost is the first
and most important consideration. As a result, it is most often used on small motor sizes (up to
approx. 22 kW [30 hp]), or where the supply is strong enough to withstand the inrush and starting
current surges without causing unacceptable voltage drops.
The harsh, damaging effects described earlier are all imposed by direct-on-line starting and, as a
control method, it is the most destructive of equipment. Its simplicity and apparent low cost,
although attractive at first sight, hide large cost penalties in the shape of increased maintenance,
reduced transmission equipment life, and higher risk of motor failure, particularly when frequent
starting and stopping is needed. In larger sized motors, special strengthening is necessary, at
higher cost, before they can be safely used with direct-on-line starting.
However, the shortcomings of the direct-on-line starter have been recognized ever since motors
have been used, and alternative systems have been developed over the years to reduce the
damaging effects of this form of control.
Method B: Wye-Delta and other Reduced Voltage Starting Systems
Reduced voltage starting makes use of the fact that motor torque is proportional to the square of
the terminal voltage. The most familiar type of reduced-voltage starter is the wye-delta, or star-
delta starter.
Consisting of three contactors and a time switch (which can be mechanical, pneumatic, electrical,
or electronic), the wye-delta starter changes the motor winding configuration from an initial wye
connection to a delta connection as the motor accelerates. The change-over or transition point is
controlled by the time switch and is usually arranged to be approximately at 80% of full speed.
The effect of starting in the wye connection is to alter the voltage across each stator winding to
58% of normal. This reduces the starting torque to a third of locked rotor torque (LRT) with a
consequent reduction in starting currents and acceleration forces.
Although an apparent improvement over the direct system, significant disadvantages still remain.
The transfer from wye to delta momentarily removes the motor from the supply. During this time
the motor is under the mechanical influence of the rotating load and, at the instant of
disconnection, current will still flow in the rotor bars due to the time delay necessary for the
magnetic flux to die away. Therefore, there is a residual flux “frozen” on the surface of the rotating
rotor, which cuts the stator windings, generating a voltage whose frequency depends on the rotor
speed. If the load inertia is small, such as in a pump, or if the friction is high, there could be a
significant loss of speed during the time the supply is disconnected. In this case, when the
reconnection to delta is made, a large phase differential can exist between the supply and the rotor
fluxes. This can give rise to very large current surges (as much or more than full-voltage locked
rotor current), together with massive transient torque oscillations, which can peak at levels in the
region of fifteen times full-load torque. Although the effects described are only present for a very
short period of time (about one fifth of a second), they are sources of great stress and damage to
the whole drive system, and where frequent starting is necessary, invoke high maintenance costs.
The current surges, in the form of very high-level short-duration “spikes”, are an increasing
problem for computer control systems and other sensitive electronic equipment. The voltage
disturbance on the supply is very difficult to filter out and can cause severe problems, especially
when larger motors are involved.
Chapter 3: Applications
SR44 Series Soft Starter User Manual
1st Ed, Rev B 07/31/2019
Содержание Stellar SR44
Страница 1: ...STELLAR SR44 SOFT STARTER USER MANUAL SR44 M WO 1st Edition Revision B...
Страница 2: ...BLANK PAGE SR44 Series Soft Starter User Manual 1st Ed Rev B 07 31 2019...
Страница 6: ...SR44 Series Soft Starter User Manual 1st Ed Rev B 07 31 2019 w 4 BLANK PAGE...
Страница 8: ...BLANK PAGE SR44 Series Soft Starter User Manual 1st Ed Rev B 07 31 2019...
Страница 12: ...Table of Contents BLANK PAGE SR44 Series Soft Starter User Manual 1st Ed Rev B 07 31 2019 t 4...
Страница 20: ...Chapter 1 Mechanical Installation BLANK PAGE SR44 Series Soft Starter User Manual 1st Ed Rev B 07 31 2019 1 8...
Страница 23: ...ELECTRICAL INSTALLATION 2 CHAPTER CHAPTER 2 2 CHAPTER BLANK PAGE 2 1c...
Страница 42: ...Chapter 2 Electrical Installation BLANK PAGE SR44 Series Soft Starter User Manual 1st Ed Rev B 07 31 2019 2 20...
Страница 66: ...Chapter 3 Applications BLANK PAGE SR44 Series Soft Starter User Manual 1st Ed Rev B 07 31 2019 3 22...
Страница 75: ...KEYPAD MENU ITEMS AND PARAMETERS CHAPTER 5 CHAPTER CHAPTER 5 BLANK PAGE 5 5 1c...
Страница 188: ...Chapter 6 Serial Communications BLANK PAGE SR44 Series Soft Starter User Manual 1st Ed Rev B 07 31 2019 6 34...
Страница 194: ...Chapter 7 Optional Hardware BLANK PAGE SR44 Series Soft Starter User Manual 1st Ed Rev B 07 31 2019 7 6...
Страница 224: ...Appendix B Applications Data BLANK PAGE SR44 Series Soft Starter User Manual 1st Ed Rev B 07 31 2019 B 6...
Страница 228: ...Appendix C Technical Hints BLANK PAGE SR44 Series Soft Starter User Manual 1st Ed Rev B 07 31 2019 C 4...
Страница 237: ...BLANK PAGE SR44 Series Soft Starter User Manual 1st Ed Rev B 07 31 2019...
Страница 238: ...SR44 Series Soft Starter User Manual 1st Ed Rev B 07 31 2019...