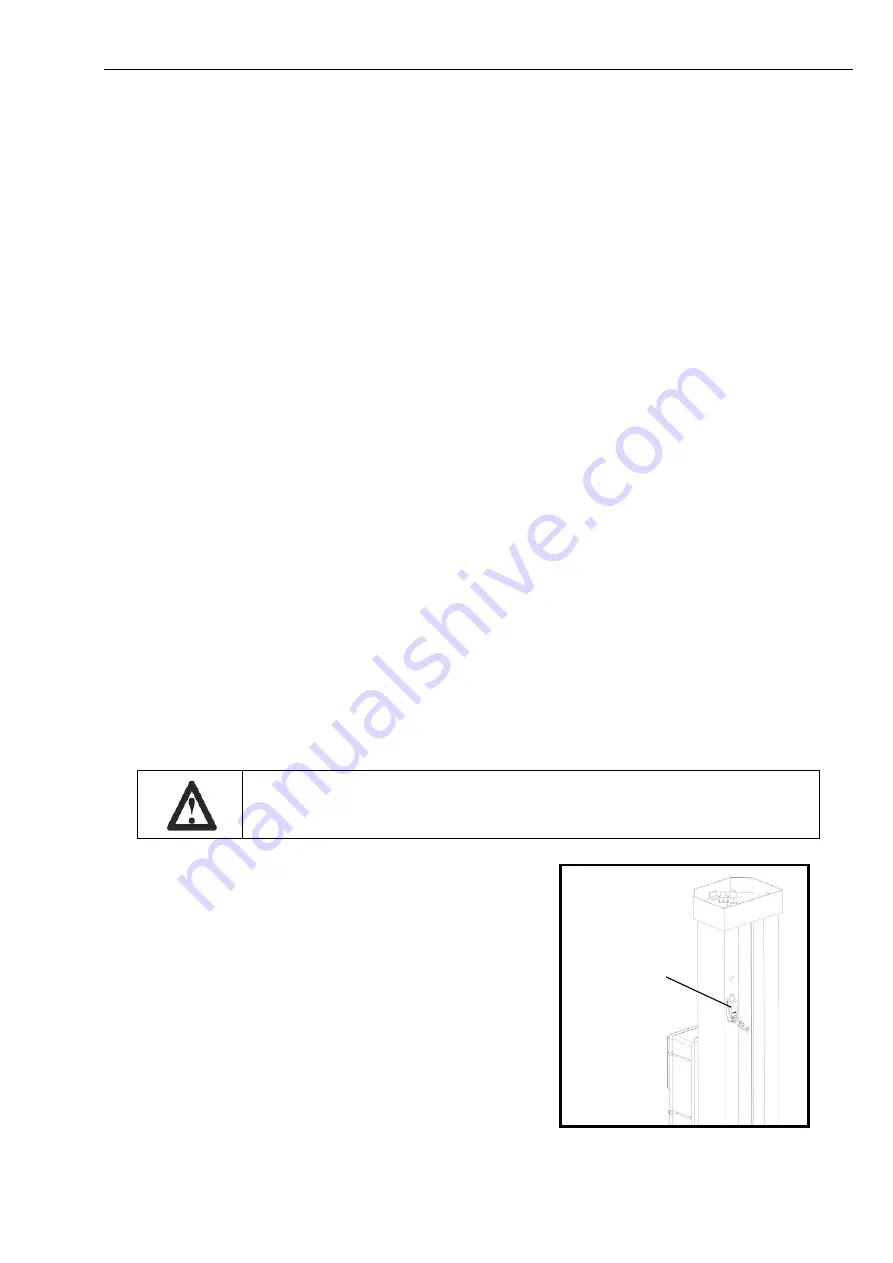
27 / 32
•
Make sure the electrical system feeding voltage is equal to that specified in the nameplate
on the motor
•
Make the lift is connected to the ground
•
Make sure the working area is free from people and objects
•
Grease sliding blocks placed on transverse beams
•
Verify that the control unit is powered
•
Pour oil in the tank (about
more than 10 liters one time
)
•
Feed the lift by switching on the power switch
•
Feed the lift with air supply
•
Verify that the motor direction of rotation is that shown on the label by pushing the
lifting button. If motor get hot or sounds peculiar please stop immediately and recheck the
electrical connection.
•
Raising the lift slowly by pressing the lifting button until the lift reaches the full height. Do
not continue pressing button after lift reaches full height. Damage to motor can occur if
continued.
•
Repeat raise and lower the lift completely at least 3 times to bleed the trapped air inside
the cylinder.
7.16
Check and adjustment
During the Start up procedure, check and make adjustments:
•
Level of runways. Adjust the cable in the equal tension;
•
Make sure the safeties are engaging uniformly and four safeties can engage in the
same position of the safety rack in the column.
•
Make sure the safety mechanisms are functioning properly. Adjust it if necessary by
screwing or loosing the nuts on the safety hook
•
Proper oil level in the tank, refill if needed;
•
Cylinder operation;
•
No leakage in hydraulic line;
•
The lift for reaching its maximum height;
7.17
Limit switch installation
Only skilled personnel must be allowed to carry out this operation. An
improper adjustment of limit switches could cause damages to the lift,
objects and people.
•
Fix the maximum height limit switch on the
power side-column in the right position using
the included screws. When routing the electric
cable of limit switch in the column, make sure
to go though the clip placed in the column to keep
it clear of any moving.
•
Carry out the complete cycle of lowering and
lifting and check for proper installation and for
reaching the
Maximum working height (1850mm), adjust it if
necessary.
Limit
switch
Содержание YL5000
Страница 1: ...1 32 jj YL5000 Wheel Alignment Four Post Lift Capacity 5000Kg USER S MANUAL ...
Страница 10: ...10 32 ...
Страница 12: ...12 32 5 4 Electrical Drawing 380V 400V 3Ph ...
Страница 13: ...13 32 5 5 Wiring Diagram ...
Страница 14: ...14 32 ...
Страница 20: ...20 32 ...