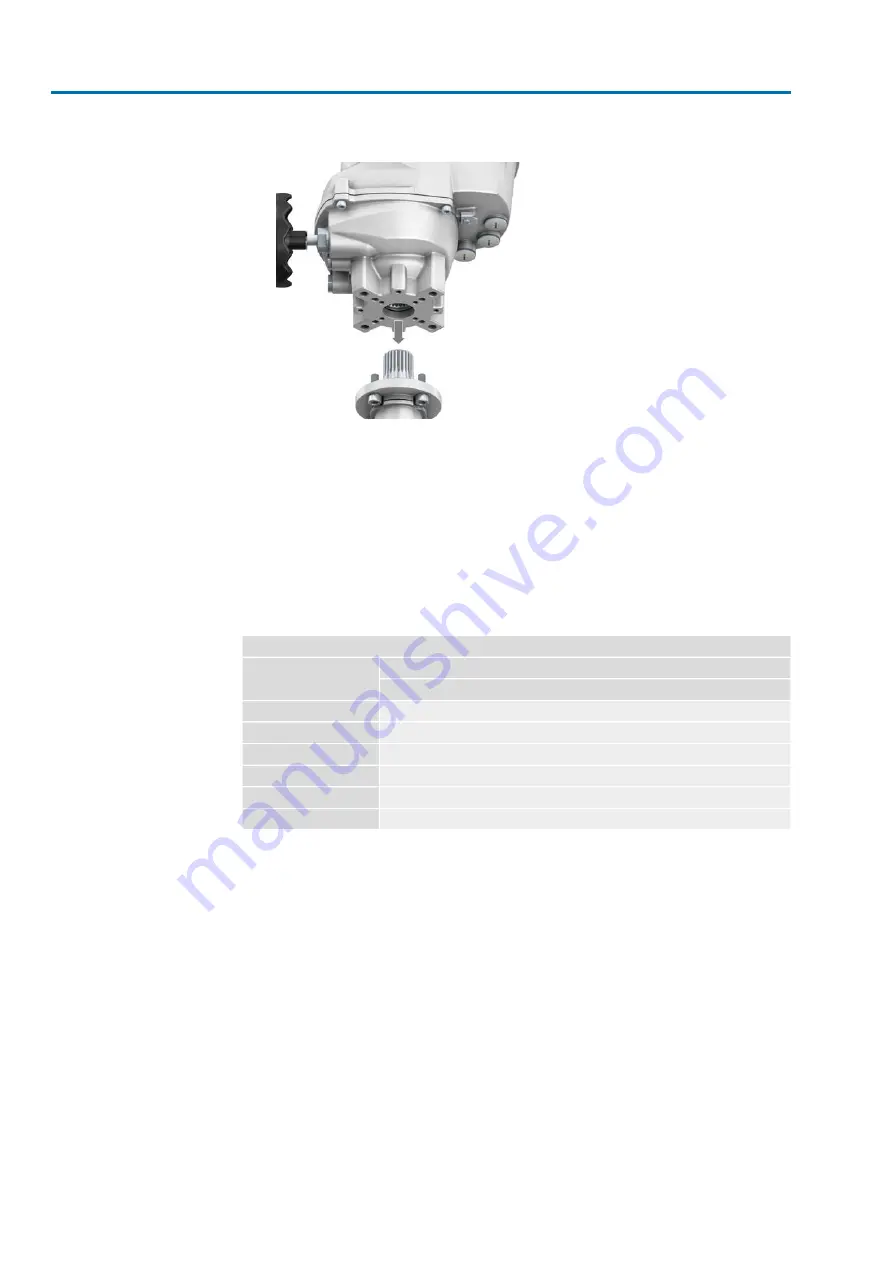
6.
Fit actuator. If required, slightly turn actuator until splines of coupling engage.
Figure 10: Mounting the actuator onto valve
Information
Ensure complete contact of flanges.
7.
If flange bores do not match thread:
7.1 Slightly rotate handwheel until bores line up.
7.2 If required, shift actuator by one tooth on the coupling.
8.
Fasten actuator with screws.
Information: We recommend applying liquid thread sealing material to the
screws to avoid contact corrosion.
9.
Fasten screws crosswise to a torque according to table.
Table 4:
Tightening torques for screws
Tightening torque [Nm]
Threads
Strength class A2-80/A4–80
10
M6
24
M8
48
M10
82
M12
200
M16
392
M20
16
PF-M25X – PF-M100X
Assembly
Parallel
Содержание PROFOX PF-M100X
Страница 9: ...3 Name plate Figure 4 Name plate arrangement 9 PF M25X PF M100X Parallel Name plate ...
Страница 49: ...15 Spare parts 15 1 Multi turn actuators PF M25 PF M100 49 PF M25X PF M100X Parallel Spare parts ...
Страница 51: ...51 PF M25X PF M100X Parallel ...
Страница 52: ...52 PF M25X PF M100X Parallel ...
Страница 55: ...55 AUMA worldwide ...