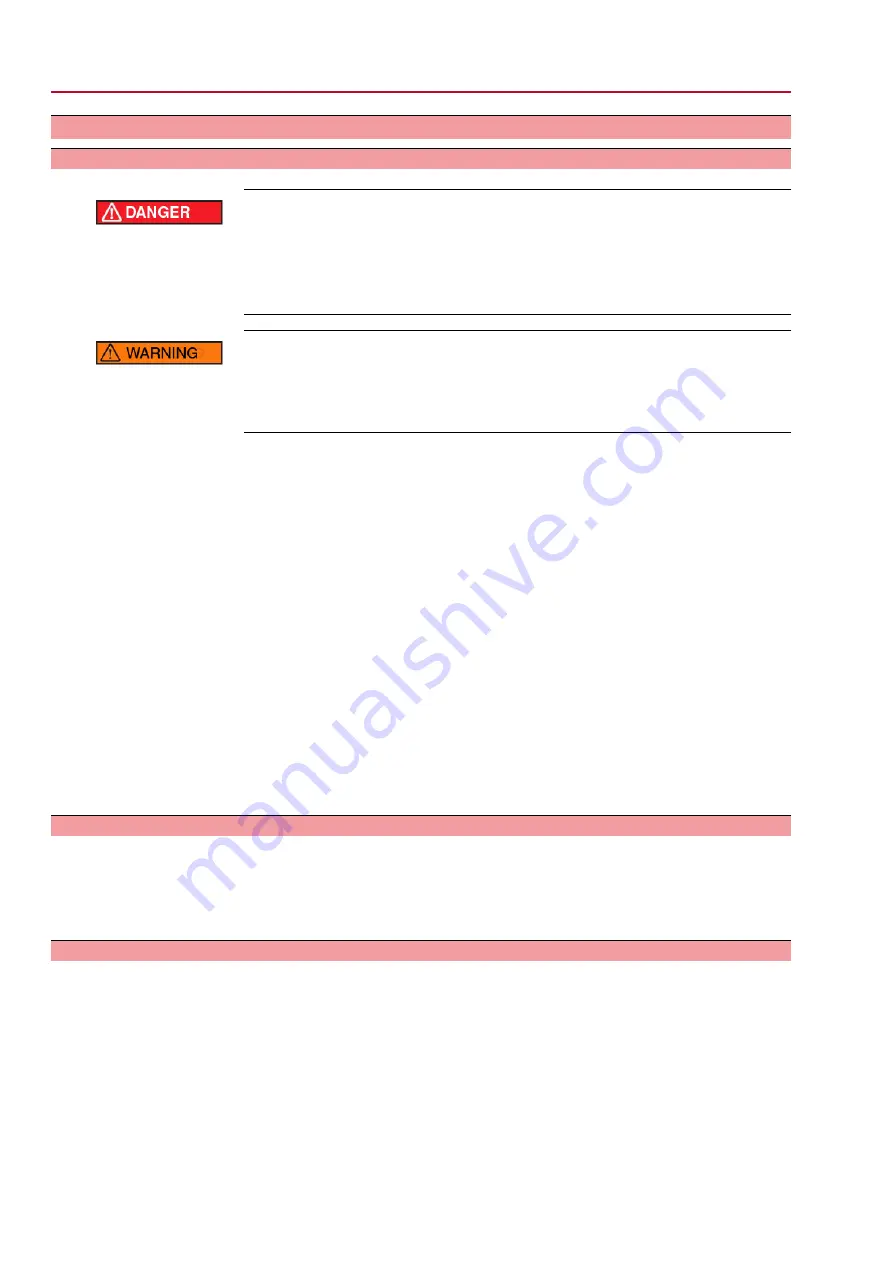
5.
Electrical connection
5.1.
Basic information
Electric shock due to presence of hazardous voltage!
Death or serious injury.
→
Disconnect device from the mains before opening.
→
When operating in potentially explosive atmospheres: Before opening, ensure
that there is no explosive gas and no voltage.
Electric shock due to incorrect electrical connection!
Risk of death or serious injury!
→
The electrical connection must be carried out exclusively by suitably qualified
personnel.
Wiring diagram/terminal
plan
The pertaining wiring diagram/terminal plan (in German or English) is attached to
the device in a weather-proof bag, together with this operation manual. It can also
be requested from AUMA (state order number, refer to name tag) or downloaded
directly from the Internet (http://www.auma.com).
Protection on site
For short-circuit protection and for disconnecting from the mains, fuses and disconnect
switches have to be provided by the customer.
The current values for respective sizing are derived from the current consumption
of the motor (refer to electrical data sheet), the current consumption of the actuator
controls, plus the current consumption of the fail safe unit. Please refer to the
operation manual pertaining to the actuator for information on the current consumption
of actuator controls.
When providing joint protection for actuator, actuator controls and fail safe unit, the
maximum power consumption of 360 W for the fail safe unit has to be accounted
for. In case separate power supply for the fail safe unit is provided, 360 W have to
be accounted for FQM protection.
Consider increased power supply starting current when selecting the circuit breaker
characteristic. We recommend tripping characteristics D or K for circuit breakers in
accordance with IEC 60947-2. To avoid spurious action, fuses with values below 2
A are not recommended.
5.2.
Electrical connection of actuator/actuator controls
The customer connection for valve control during standard operation (power
connection and signal cables) is made via the electrical connection of the actuator
or the actuator controls. Any procedures for opening/closing the terminal compartment
and for connecting the cables are described in the operation manual pertaining to
the actuator.
5.3.
Electrical connection for fail safe unit
On delivery, the electrical connection of the fail safe unit is already equipped with
the power supply for FQM and the signal cable for actuator controls.
The tripping signal (
ESD
) for a fail safe operation as well as direct feedbacks (e.g.
end switch signals
LSO/LSC
) have to be connected in compliance with the wiring
diagram at the customer’s.
A KES-Exd type electrical connector will be provided for electrical connection.
18
FQMEx 05.1 – FQMEx 12.1
Electrical connection
FM version (Class/Division System)