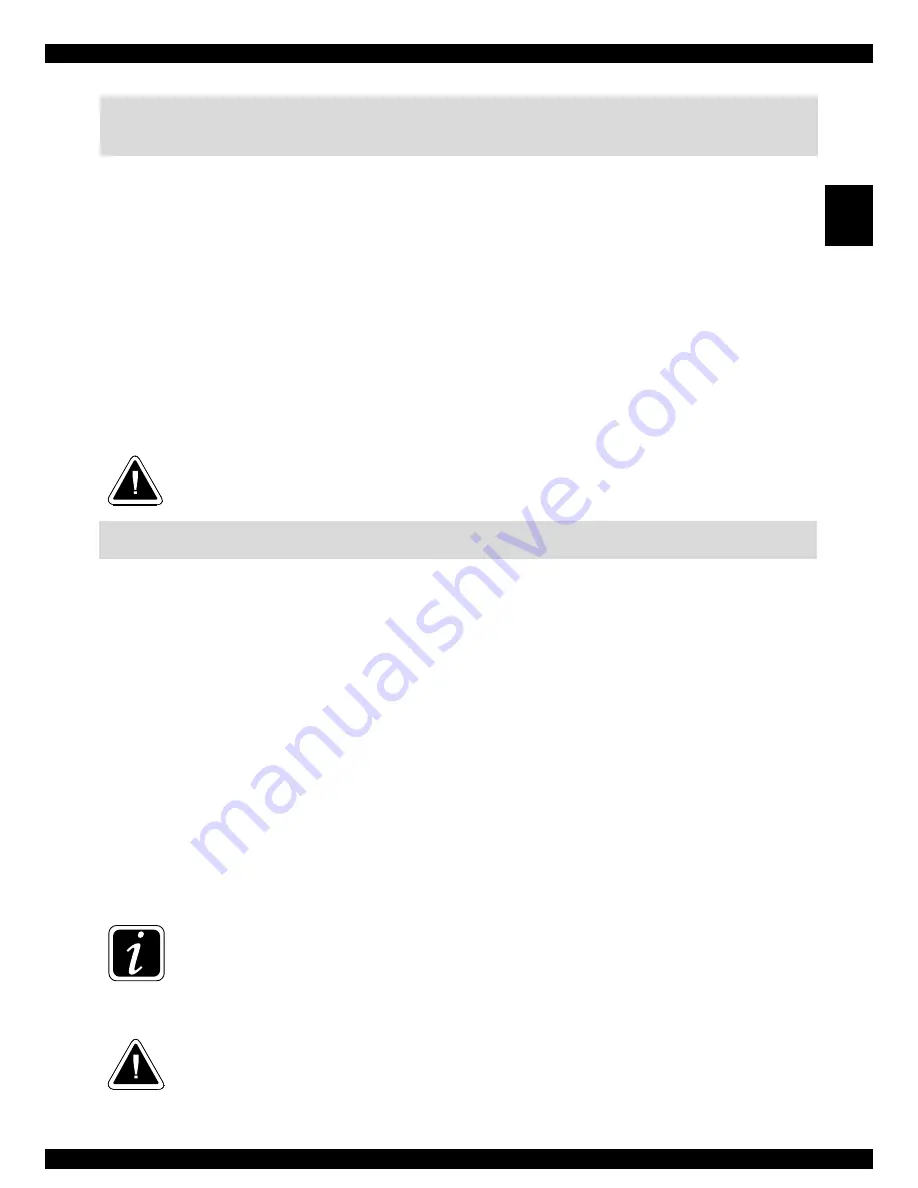
www.atmos.cz
GB-17
GB
Instruction manual - GB
14. Obligatory ČSN EN standards related to boiler designing
and installation
ČSN EN 303-5
- Solid fuel boilers for central heating
ČSN 06 0310
- Central heating, designing and assembly
ČSN 06 0830
- Safety devices for central heating and hot potable water heating
ČSN EN 73 4201 - Designing chimneys and flue-gas ducting
ČSN EN 1443
- Chimney structures – General requirements
ČSN 06 1008
- Fire safety of local appliances and heat sources
ČSN EN 13501-1 -
Fire classification of construction products and construction of buildings - Part 1
ČSN EN 1264-1
- Floor heating – Systems and components – Definitions and symbols
ČSN EN 1264-2
- Floor heating – Systems and components – Heat output calculation
ČSN EN 1264-3
- Floor heating – Systems and components – Designing
ČSN EN 442-2
- Heaters – Testing and test analysis
Standards for evaluation of conformity and other technical standards:
ČSN EN ISO 12100:2012, ČSN EN 953+A1:2009, ČSN EN ISO 11202:2011, ČSN EN ISO
3746:2011, ČSN ISO 1819:1993, ČSN EN 60335-1ed.2:2003
CAUTION – the boiler must be installed in compliance with a design prepared in ad
-
vance. Installation may only be carried out by persons trained by the manufacturer.
15. Choice and connection method of control and heating elements
Boilers are provided to the user with the basic boiler performance control elements compliant with
requirements for convenient heating and its safety. The regulation ensures that the required temperature
of the water exiting the boiler (80 - 90 °C) is adhered to. The boiler is equipped with two thermostats
(70 °C and 95 °C ) for switching the boiler-circuit pump. The 70 °C thermostat switches the boiler-circuit
pump on as soon as the temperature exceeds this value. The 95 °C thermostat is a safety component.
It protects the boiler against overheating in case of incorrectly set waste-gas thermostat (it switches the
boiler-circuit pump on always when the boiler water temperature exceeds 95 °C). Connection of these
elements is illustrated in the wiring diagram. General rule is that every pump in the system must always
be controlled by a separate thermostat to avoid a temperature drop of water returning to the boiler un-
der 65 °C. After the boiler has been installed, the pump situated in the heated-building circuit must be
switched by means of a separate thermostat or electronic regulation. Setting the required water tempera-
ture for the building is always achieved by means of a three-way mixing valve. The mixing valve can be
regulated manually or by electronic regulation, which contributes to a more convenient and economical
operation of the heating system. The connection of these additional elements is always designed by a
specialist designer to suit specific conditions of the heating system. Electric installations related to the
additional equipping the boilers with the above mentioned elements must be carried out by an expert in
compliance with valid ČSN EN standards.
When installing the boiler, we recommend using an opened expansion tank. However, a
closed tank may also be used if permitted in the standards of the specific country. The
boiler must always be installed in a way which prevents overheating (and subsequent
damage) even during a power cut. It is because the boiler has certain momentum. Boiler
should always be connected with accumulation (buffer) tank with minimal volume 1000 l.
There are several ways of protecting the boiler against overheating. Connecting an over-
heat prevention cooling loop with a TS 131 3/4 A (95 °C) or WATTS STS 20 (97 °C) valve
to the public water system. In cases when the user has his/her own well, the boiler can
be additionally protected by using a back-up power supply (battery with an exchanger)