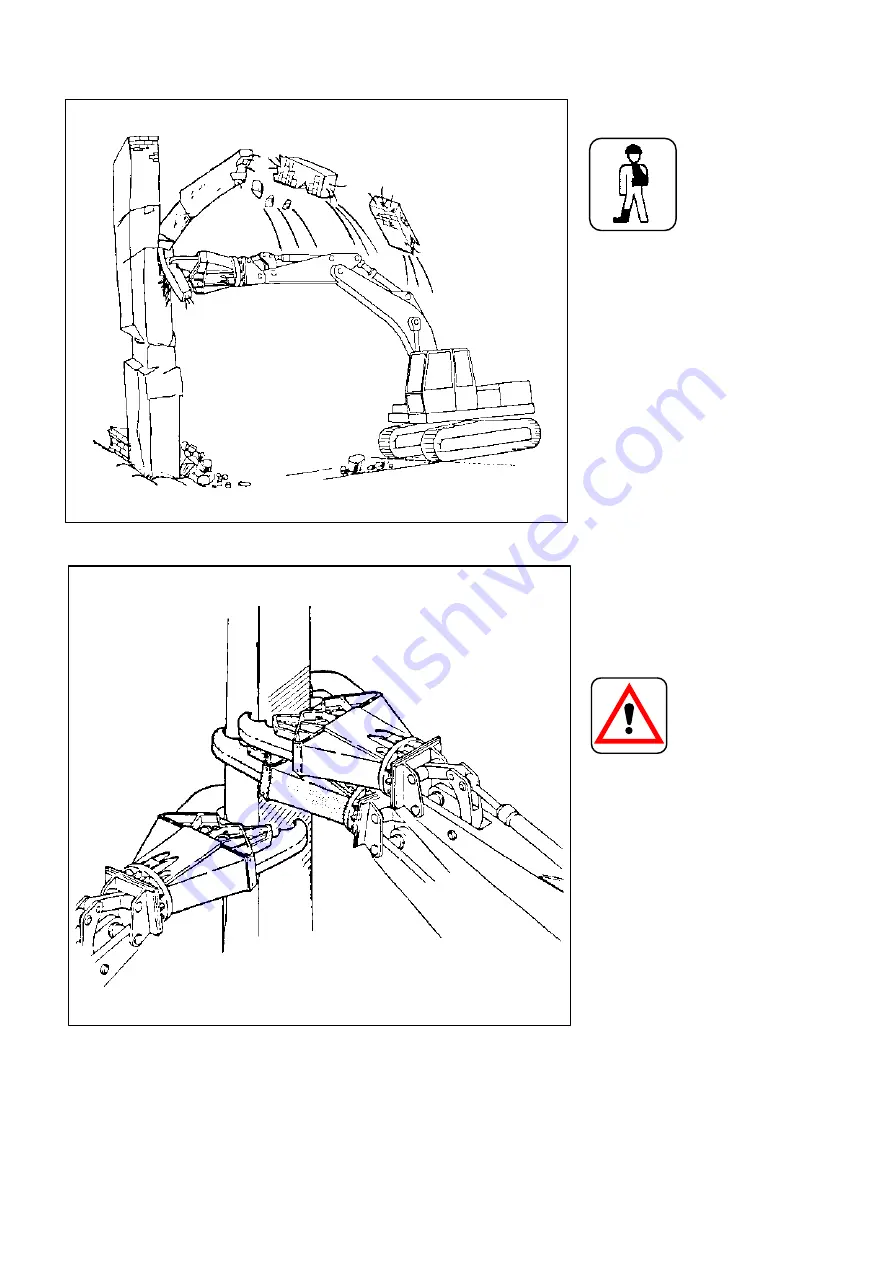
22
Instructions on the correct use of the hydraulic cutter
When demolishing col
umns, supports and brick
work, always start break
ing from the top down
wards.
Large chunks of the bro
ken material may other
wise fall onto the cutter or
carrier and cause dam
age. If necessary, larger
elements should be se
cured beforehand.
Caution!
K
Fig. 13
Warning!
K
Fig. 14
Change the hydraulic cut
ter’s point of attack in good
time. Wherever possible,
demolition should be
started on narrower faces.
Содержание CombiCutter CC 1501
Страница 2: ......
Страница 42: ...Bild 40 4 5 1 6 3 2 A B CC 2100 42 ...