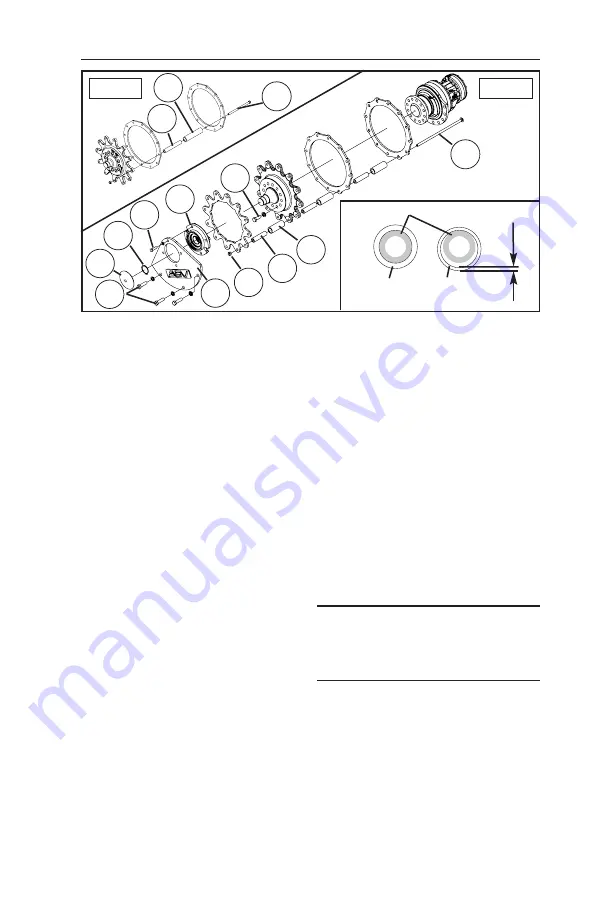
MAINTENANCE
Drive Sprocket Rollers
56
Drive Sprocket Rollers
ASV rubber track loaders utilize
rollers on the drive sprockets to
drive the track. These rollers
help minimize friction between
the track and the drive sprocket
to prolong track life.
The rollers rotate around hard-
ened steel pins and usually wear
on their inside surfaces. As they
wear, the rollers become thinner,
but will continue to function as
long as they rotate freely around
the pins. Sprocket rollers should
be inspected every 50 hours of
operation and replaced if
cracked or worn to less than
35% of original thickness. (.088”)
To replace worn rollers:
1.
Begin by performing steps 1-
4 in the track removal proce-
dure on page 52 to allow the
sprocket to be removed.
2.
Remove the seven bearing
plate mounting bolts (A, I),
then remove the plate (B)
from the drive table.
3.
Remove the bearing cap
(G) by tapping around the
bulged area of the cap with
a hammer. This will relieve
the outward pressure on the
cap and allow for removal.
4.
Remove the external snap
ring (H) from the bearing
shaft.
5.
Using a puller, remove the
bearing assembly (J) from
the shaft.
6.
Remove the sprocket
mounting bolts (C), then
remove the sprocket.
Note:
You may need to pry or lift
the track upwards with a hoist
above the drive sprocket to pro-
vide clearance for removal.
7.
Remove one bolt (F) holding
the steel pins (D) and rollers
(E) in place. Install the new
rollers over the pins, then
slide the bolt back through
the sprocket and pins and
secure it with the nut (K).
A
H
F
E
D
New Roller Normal Wear
35% life
Steel Pin
(.088”)
C
PT-70
D
E
F
PT-80
J
I
G
B
K
Содержание PT-80
Страница 6: ...5 ...
Страница 14: ...13 ...
Страница 32: ...31 ...
Страница 68: ...SERVICE LOG 67 Hours Service Performed Notes ...
Страница 69: ...SERVICE LOG 68 Hours Service Performed Notes ...
Страница 70: ...SERVICE LOG 69 Hours Service Performed Notes ...
Страница 71: ...SERVICE LOG 70 Hours Service Performed Notes ...